Here is the process of how I laid out the propeller airfoil profiles in order to obtain an even pitch angle along the length of the propeller blades.
To prep for this I first laid out the primary loop shape on the bottom plane looking down from the top. The highlighted blue lines will be the trailing edges of the blades and the lower rails to guide the loft. The other two edges of the propeller outline need to be projected to 3D planes done in two separate steps.
Most of the dashed construction lines are to align construction planes perpendicular to the bottom plane to perform section analyses to check that the blades lofted correctly, and as planes to sketch the 5 airfoil profiles on.
Then I sketched the side view profile.
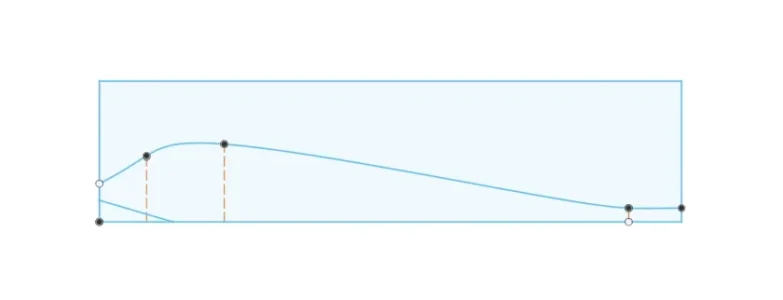
Then I extruded the left lobe of the plan view upwards to create a body...
Then I used the upper section of the side view to extrude a cut thru the left lobe body.
Below is the resulting body. These two extrusion processes were to get the 3 dimensional representation of the leading edge of the left side lobe which will later be projected onto a plane. You can see the curved line highlighted in light blue.
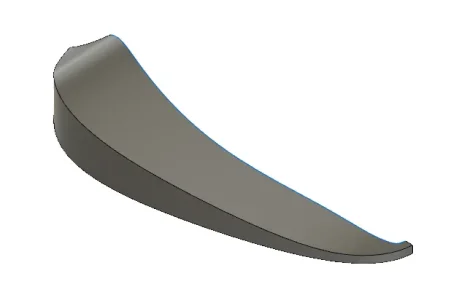
You cannot do both lobes at once because the leading and trailing edges are reversed for the right side lobe. The next step is to lay out 3 sketches for the loft, starting with selecting the construction planes, starting a new sketch on the plane, and then projecting lines to where the body intersects each plane.
Select the previously constructed plane. Select create sketch.
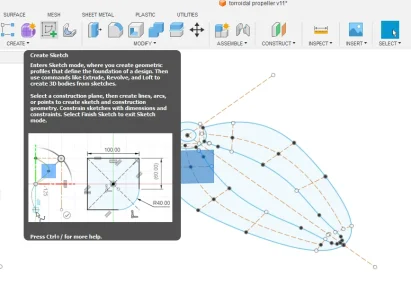
Select create, project/include, intersection. Select the geometry to intersect, in this case the left side body. Make sure the selection filter is on body and not edges. To facilitate the sketching it is best to keep the body set to not visible, and just select if from the left side menu.
The selection should look something like as follows, convert all four lines to dashed construction lines, feel free to erase the upper and lower lines if you wish. Place your airfoil sketch inside the construction box being mindful that the profile sketch MUST have a point touching the lower left corner and the upper left corner or the the leading and trailing edge rails will not intersect with the profile sketch making it impossible to loft the blades along the rails.
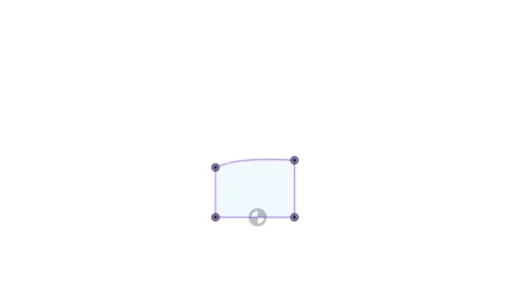
You can see my starting blade root profile where it intersects the hub touches both corners as required. I calculated the required pitch angle for this radius and laid a construction line at that angle to ensure my airfoil closely aligned with the pitch angle. I sketched a base line the width of 2 extruded walls from a 0.4mm nozzle as a printing base. Then I sketched an ideal airfoil using a construction line and then sketched an adjusted airfloil in a solid spline starting at the lower left base corner and ending at the right side of the base line. I then adjusted the spline to match the ideal airfoil as closely as I could.
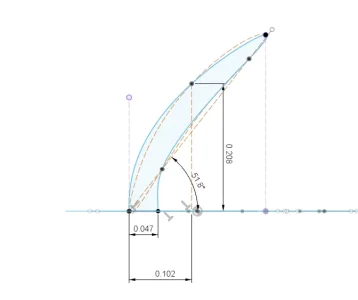
Then I repeated the process for the end airfoil using the same methodology as above. The result looks like this:
Then I created a blade tip profile that is common for both left and right portions of the bi-loop propeller. I deleted all the intersection lines but the four spline points are located at each corner of the intersection.
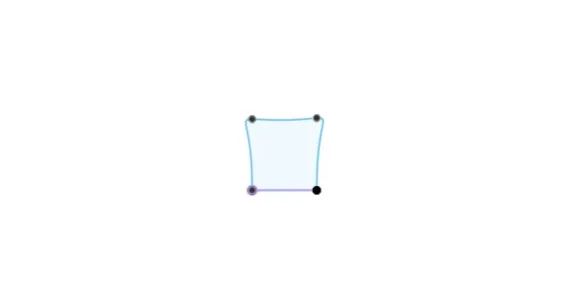
Next up are the right side profiles. But if you use the same method you will get this as your intersection result:
The leading edge and the trailing edges are reversed... if you were to copy and then mirror the profile from the other side the leading edge will not intersect the projected rail you will make next.
Modifications are required to draw a new side profile to use for the right side. I'll cover that in a new post later.