So after much dithering I finally decided to convert my mill to 3 phase with VFD speed control.
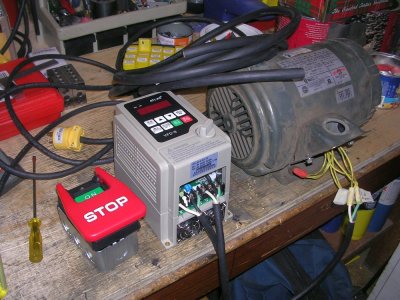
Pretty much have everything I need now
2 HP 3 PH motor $60 from Kijiji
4 HP VFD $75 from Amazon
ESD switch $18 from BB
12' of 14AWG 4 strand electrical cord $23 from Home Depot
I was going to wire the ESD into the singe phase side and use it double duty as an ESD and an on/off sw for the VFD but I noticed it's capable of handling 3 phase so now I'm not sure what to do? Should I wire it to the 3 phase side or to the single phase side? Do you think it really matters?
Craig
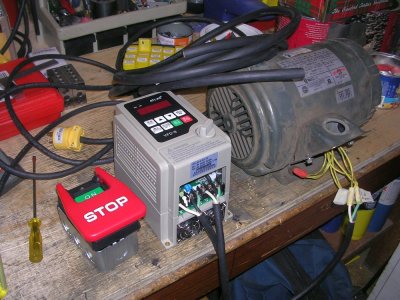
Pretty much have everything I need now
2 HP 3 PH motor $60 from Kijiji
4 HP VFD $75 from Amazon
ESD switch $18 from BB
12' of 14AWG 4 strand electrical cord $23 from Home Depot
I was going to wire the ESD into the singe phase side and use it double duty as an ESD and an on/off sw for the VFD but I noticed it's capable of handling 3 phase so now I'm not sure what to do? Should I wire it to the 3 phase side or to the single phase side? Do you think it really matters?
Craig
Last edited: