A couple of weeks ago I tried taking one of my contactors apart to get a look inside and stopped part way through , at that point I realized that further disassembly put the part at risk of being damaged or destroyed. These dinky little parts are throw away , non serviceable items , now , getting them is another entirely different challenge as I've discovered. I have no idea when I will be getting the set I ordered on the 28th of January , from what I am seeing on my ebay purchase history page is , the seller is away until Feb 7 , so when he sobers up and gets back to the office to fill all the orders placed over the two weeks he had off , that puts my delivery date well into March. The fact that Busy Bee has no parts sends a clear message as to where they stand on the customer service side , piss poor !!!
I should respond to the comment about how long this is taking.
I have lots of other things going on that eat up time , there's no doubt , my participation on this forum burns lots of it , when I sit down at my computer , the first thing I usually do is look at this forum . I feel welcome here , it's a great group of people and I'll be paying up to get a premium membership .
Other stuff I have going on , is often prioritized above the ongoing lathe issue , even though the end is near and a solution might be soon . I work on it when I have time and If I am not feeling up to it I do other things ...............
Like this ...................
I Started on this project last month , there has been a great deal of progress so far and yesterday I got the remaining parts needed to finish it.
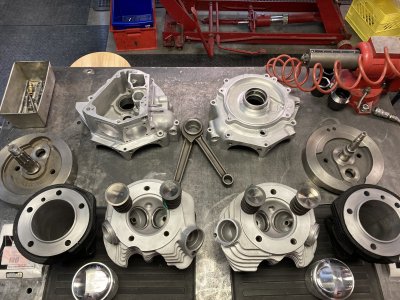
This one is a 1978 74 cubic inch Shovelhead
The cylinders have been painted , bored & honed to size , rings fit .
The rods are almost done , the bores on the big end have been honed straight again , they're round and honed to the the target dimension to accept oversized rollers .
I need to press in the bushings on the small end and hone those to the correct clearance and then I will be weighing some of the parts , both rotating & reciprocating , doing some math and then balancing the flywheels , it's labour intensive but worth it .
I have the crank cases cleaned , threads chased , mating surfaces prepped , the roller bearing main on the right side has been lapped to a custom fit with oversize rollers.
The crankshaft , once it has been balanced needs to be assembled , trued and installed into the crankcases.
The heads have been cleaned , bead blasted , the valves have been ground as well as the seats , ground to three angles , those need to be assembled with the new springs I just got yesterday .
Then there's the oil pump cam chest and top end that needs to be assembled . The rocker arms have had new bushings pressed in and sized .
All of this is done lovingly , each piece massaged , hand fit and measured to ensure it is right .
The lathe ?
pppppfffffff , I might work on it a bit today , or tomorrow or monday , tuesday its back to work .
Oh I almost forgot I have nine month old 100 lb puppy thats very mischievious and full of energy , she's my chief of security , in training .
So you see , I do have a full dance card