It's fixed , a long time and a parts sourcing nightmare but it runs again .
Lot's of the participants here have helped to solve the issues , I thank each and every one of you.
From the beginning I struggled with this , I'm a low voltage DC guy , my inexperience with AC circuits and this type of equipment made me look and feel like a bozo.
Things I did wrong .............
I bought a motor that I didn't need. $360.00 !!!
I activated contactors manually and damaged / killed components that may have otherwise been OK , I fried two contactors , this is the result of my poking around in there.
I ordered parts from suppliers that I shouldn't have ( more on that later )
I used a multi meter that was faulty and had no capacitance test function , once I had the correct meter, things changed , actual progress was made.
Things that I did right ..............
In an effort to get a better understanding of how this machine is wired and how it works , I followed every wire and drew out a proper wiring diagram so I could actually see the circuit and how it works. I've never been a fan of simplified wiring diagrams , where several wires are drawn as one for the sake of clarity.
I took my time working through this , and with the help of several of the members here was able to learn about some fundamental motor operation theory and to learn about testing capacitors.
After mulling it over , I decided to not take the easy way out and cave in to the pressure to strip all the Chinese crap out and change to a drum switch , even though I was close to doing this to save time , also I know I could have made this work , the start button I was going to use has thermal overload protection just like the starter on my mill and a drum switch would have been installed between that and the motor.
I did take the time to clean up the wiring while I was in there and replace the cheesy broken din rail terminal strip.
Parts sourcing was the biggest hurdle to get over with this .
I should say right now , at the end of the day , Busy Bee was who got me all of the parts , I paid dearly for them but they got me what I needed .
It took some negotiating at the local store here , at first they were just not interested , "the machine was too old " , once I proved to them that the current version of this machine is very similar , shares all of the same switching , same transformer and same motor , they were able to order the parts through the Concord store. It only took two months for them to "get it" and place the order .
I think the staff here may have learned some customer service lessons in the process , or I hope they did.
However , before I was able to convince Busy Bee that this old lathe was worth saving ...............
This happened ..............
I ordered contactors , off of ebay , a set of three from Trillium controls in Concord Ont . , they were the wrong ones , they never did reply to any of my messages , to please get me the correct contactors , I could not return them because of this , I'll not be buying anything else from them , I'm stuck with the contactors they sent.
I also bought a thermal overload relay off of ebay , that came out of China too but arrived quickly , I didn't need one but now I have a spare, the good thing is , this part is correct.
I ordered a second set of contactors from a vendor based in China on ebay , this was even more frustrating , it took weeks for them to even ship them because of Chinese new year . The picture in the ebay listing showed the exact contactor I needed , I ordered three , eventually after waiting over a month , I got them , only to find out the idiot who packed the order threw the wrong contactors in the box. I worked with them , as difficult and frustrating as that was , they recognized the mistake and have partially refunded my money , I can keep the contactors.
There isn't an English catalog that I know of where you can look at these specific contactors and choose the exact replacement .
I should mention , yes I ended up with a bunch of contactors I couldn't use , the upside is , they were $15 each from China , $30 each from Trillium , the down side is the Busy Bee contactors were priced at $65 each !!!
There are some space limitations inside the electrical box, so to subsitute in a different contactor or three isn't really an option I was willing to entertain.
I ordered new motor capacitors off of Amazon , changed those out and made the original motor a working unit again.
I ordered new terminal strips off of Amazon , to replace the cheesy cracked din rail Chinese crappy ones that the machine came with.
Busy Bee got me the exact contactors I needed , they were very expensive , they also got me a pair of directional switches and an "E" stop switch , I only used the contactors , the other switches are spares.
My theory on switches is ........ every time you activate a switch , it's one less time it's going to work.
So , to summarize the parts list , the parts I actually changed to get this repaired.................
Motor start Capacitor
Motor run Capacitor
All three contactors
Terminal strips where all the connections entering or leaving the electrical box are made.
I replaced the terminal strips that were in poor condition , relocated the one and only fuse the machine came with and relocated the ground terminal strip , while i was cleaning up the messy electrical box.
I have spare parts now , new and used .
I have a spare motor too ( hangs head in shame )
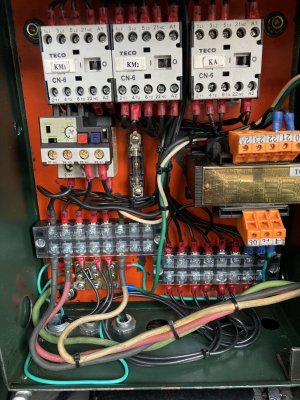