TorontoBuilder
Sapientia et Doctrina Stabilitas
The grinds:
Front grinding fixture cuts the end cutting edge and the axial primary relief angle with the slight concave angle by positioning the end mill at a slight angle to the vertical flat face of the grinding wheel.
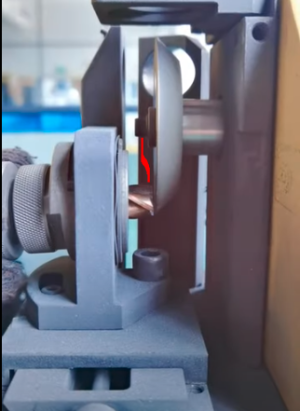
The A tool plate grinds the end gash and the axial rake angle of the cutting edge by positioning the end mill against both the front of the vertical flat face and rear bevel of the grinding wheel. I believe that the positioning pins in the top of the tool insert sets the gash angle while the tilt of the plate insert sets the axial rake angle.
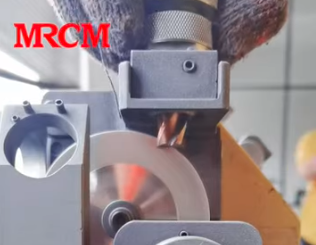
One of two other grinding fixtures cut the secondary axial clearance angles. The choice of which fixture to use depends on the cutter diameter.
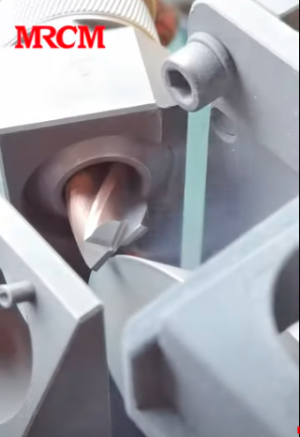
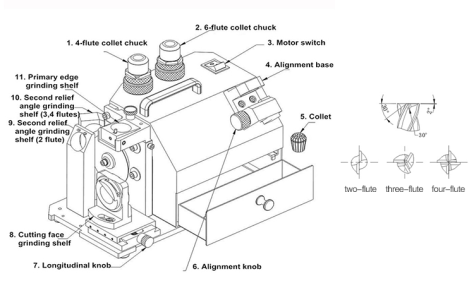
Front grinding fixture cuts the end cutting edge and the axial primary relief angle with the slight concave angle by positioning the end mill at a slight angle to the vertical flat face of the grinding wheel.
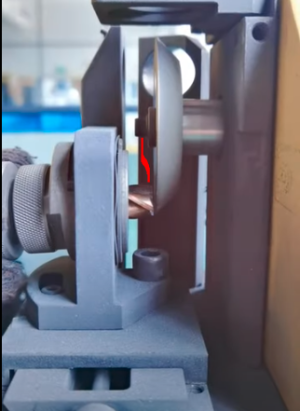
The A tool plate grinds the end gash and the axial rake angle of the cutting edge by positioning the end mill against both the front of the vertical flat face and rear bevel of the grinding wheel. I believe that the positioning pins in the top of the tool insert sets the gash angle while the tilt of the plate insert sets the axial rake angle.
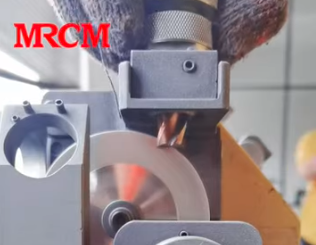
One of two other grinding fixtures cut the secondary axial clearance angles. The choice of which fixture to use depends on the cutter diameter.
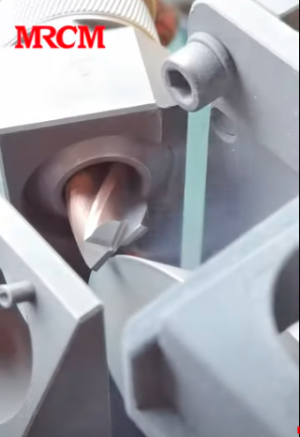
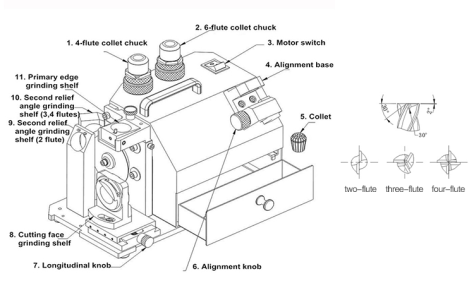