I don’t put bolts into the parts I model, just the holes.
My next experiment with “large” Fusion assemblies will be to export them as a STL or STEP and then see if that makes it easier to use them without bogging my computer down.
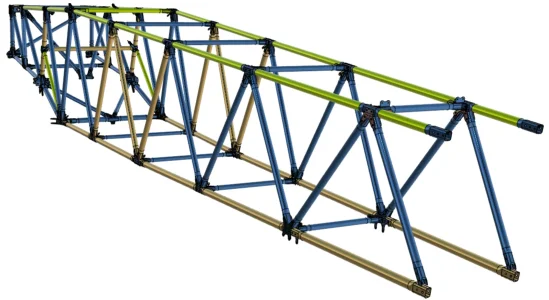
Above is about as complicated as I can go before my computer craps out…
My next experiment with “large” Fusion assemblies will be to export them as a STL or STEP and then see if that makes it easier to use them without bogging my computer down.
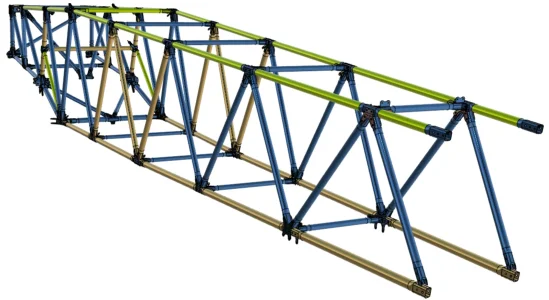
Above is about as complicated as I can go before my computer craps out…