I've noticed that the headstock on this lathe is taller from the centerline of the chuck to the top of the lid and adding the tool tray had made it taller still. The consequence of that is the chuck keys are too short so the T handles interfere with the tray. I have quite a bit of 1" cold rolled so I made up 2 new handles. Of course the 3 jaw and 4 jaw chucks take different sizes😕. I was able to improve the fit of the square end of the keys over the originals also.
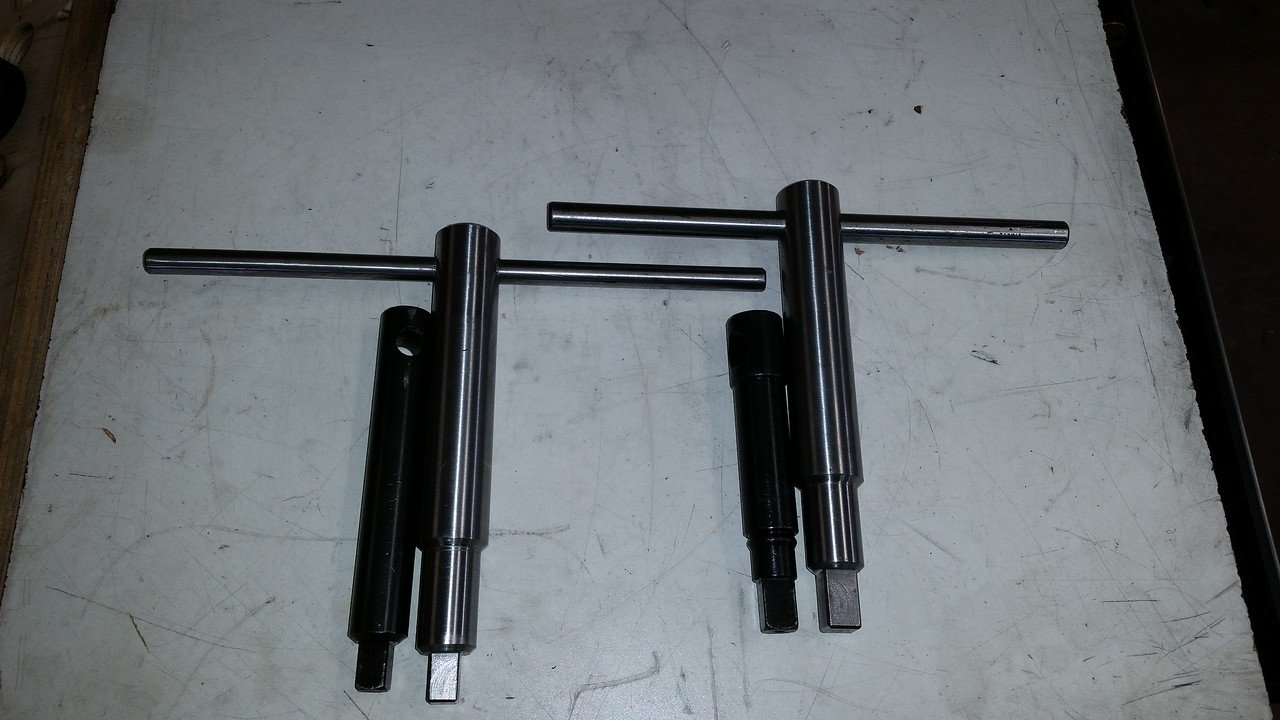
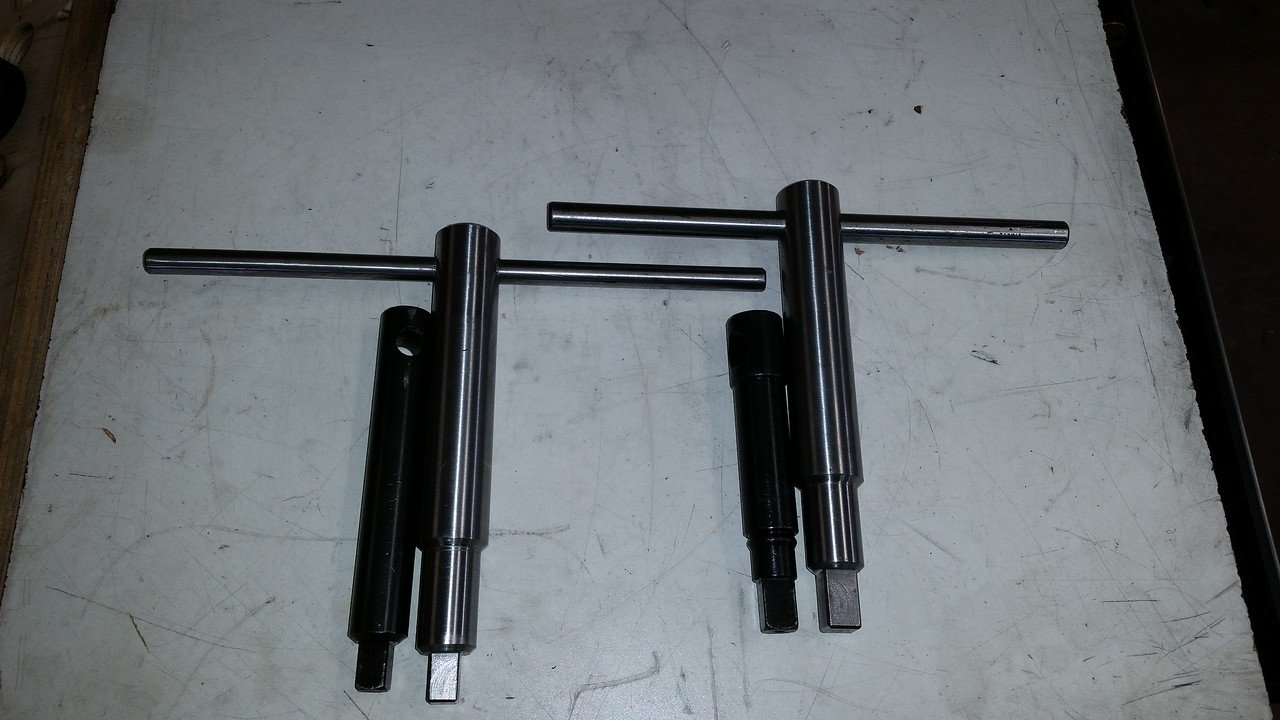
Last edited: