Success.... I got the chuck mounted.

Here are my transfer punches ready to rock.

And the resultant punch marks.

Nailed the bolt holes.
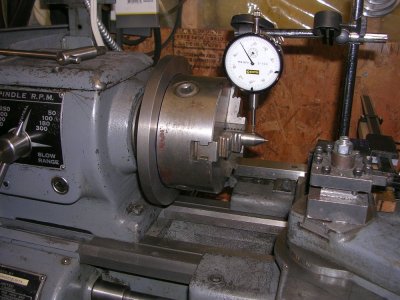
And the chuck mounted on the lathe.
The runout on the mounting plate and chuck body are about the same as my PRAT. 0.004" (high-low) so didn't really gain anything there. The runout on mounted stock is significantly worse. 0.015" v.s. 0.005"🙁
I'm now wondering if the jaws are mounted in the wrong scroll slot. The jaws and slots aren't numbered or keyed to each other.
Craig

Here are my transfer punches ready to rock.

And the resultant punch marks.

Nailed the bolt holes.
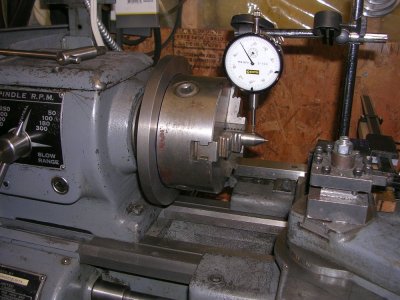
And the chuck mounted on the lathe.
The runout on the mounting plate and chuck body are about the same as my PRAT. 0.004" (high-low) so didn't really gain anything there. The runout on mounted stock is significantly worse. 0.015" v.s. 0.005"🙁
I'm now wondering if the jaws are mounted in the wrong scroll slot. The jaws and slots aren't numbered or keyed to each other.
Craig