Belt grinder side quest #2......
I've been thinking round and round in circles the past few days about how to make my drive wheel, while chipping away at the other components. The leading method was to roll one from flat, similar to how I made my
other steel wheels, but with a machined hub/keyway. I wasn't really opposed to that, I think it's a pretty viable option, but for some reason I couldn't figure out why I wasn't 100% on it.....Then it hit me. I didn't need anything to do that. I have everything here, I have the tools, the material, the method figured out, I could crank one out in an afternoon, and it's the easiet path to victory. But where's the fun in that? The majority of time, I choose my projects and methods for specific reasons. I'm always trying to expand the capabilites of the shop and to further my own knowledge and experience learning new things. It's not always about making "the thing". It's also about the journey to get there.
Back at the start of this, I'd given a quick thought to casting one. Not a bad idea, but how? My little electric foundry is too small. I've always wanted to build a bigger one, and have had a collection of parts lying around acclimatizing for years, but it's a tall task to get up and running and too big of a side quest to just to do one wheel.....What about the coal forge? Or the ribbon burner forge? I'd have to make a steel crucible, but either would work to heat up a suitably sized crucible to cast the wheel. Great, now about molding. My homemade greensand sucks, I don't want to buy any right now either. I'd also have to build a new flask, make a pattern etc.....Lost PLA? I don't have a kiln to burn it out, but lost foam? Hmmmm. Always wanted to try it, but haven't had the right project to give it a go. The wheel seems like as good a project as any. But how do I cut the foam pattern......CNC?, lathe? Too easy. Hot wire would work great, but I don't have one....Perfect.
Started mulling over a design the past couple days. Wanted it it to be a quick and simple build and was simply going to hack together something out of plywood but once I got going on it, I start gravitating in a diferent direction....one thing led to another and now I have a hot wire cutter....
I didn't really take a lot of pics along the way, and this was very much a build from the junkpile with minimal effort type of build.
This is the frame underneath. I tried to make it stout, but adjustable in every which way. The wire is clamped to the lower frame with a homemade clamp, it runs through a steel tube (inflator needle) pressed into the table, and then through the same, but curved 90* in the upper arm. A simple loop hooked on a spring completes the connection. The table is adjustable so I can line up the lower bushing with the upper one for square cuts. The arm is adjustable in/out so I can cut a taper if I want to.
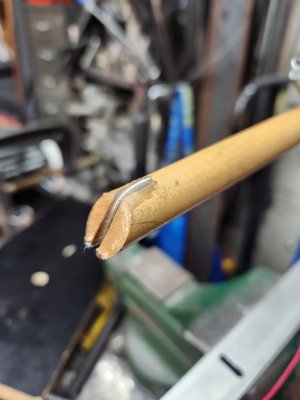
I'm pretty happy with it. Still need to make a fence, and adjustable pivot for cutting circles, but that shouldn't be too bad. Right now I'm using 0.02" stainless lock wire, but have a few other types of old guitar string to try out too. Using an adjustable bench power supply to power it.
And a shot of the bench while I was building this, just to appease the resident squatch. This is pretty normal around here. A project on top of a project, on top of a project.....
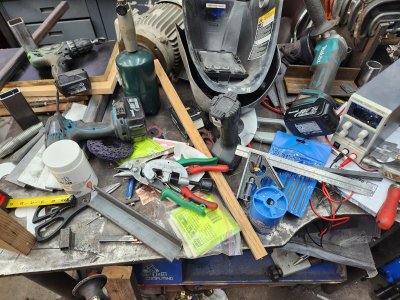
Well, at least I got one project finished on the bench today.....