I still have not found the original info I was looking for but I did find this. From
https://modelenginenews.org/meng/quorn/drilljig.html
First, we probably should define just what "4 facet" sharpening is, and how it differs from conventional "conical back-off" sharpening. In order to cut, a twist drill, like any tool, requires a relief behind the cutting edge. This prevents the area of the drill behind the cutting lip from rubbing on the end of the hole as it turns and advances. But we also want a strong, long lasting cutting edge, so excessive relief will make the edge more acute, and hence more susceptible to wear and damage. Let's consider the "standard" drill sharpening method first.
Conical Back-Off
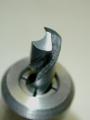
Standard conical sharpening produces a point angle of 118 degrees, but it's not a cone. The actual tip is a straight line when viewed end-on, and an arc when viewed from the side. This is called the "chisel edge" (
ref [WSP12]). This is an artifact of the sharpening process and is formed by the intersection of two conical sections. This achieves what we are after: a strong cutting edge (called the "lip"), with a "land"—the area behind the lip—that falls away at an increasing rate to provide the lip relief angle necessary if the drill is to cut. Jigs to produce this shape are straight forward (relatively
) and a good one will produce a good result quickly—just the ticket if you are a drill manufacturer, or a user how just wants a hole and does not particularly care if it's a bit oversize, and may not be totally straight. The downside is that chisel tip. Unless the work carries a center-pop mark that is at least as wide as the chisel, the drill tip is going to wander all over the place when presented to the work. And if it starts crooked, you can be sure it's not going to get any better. This is why we generally drill a pilot with a "center" or "Slocumbe" drill (as they as called in England and her former colonies). This provides a cavity to clear the chisel point so that by the time the chisel actually reaches metal, a hole has been formed to guide the drill and there's some kind of chance it will stay on track.
Four Facet Sharpening
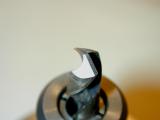
The 4 Facet point, as seen here, is formed by grinding two flat areas (facets) on each land. The first is shallow; 80 degrees relative to the drill axis, representing a relief of 10 degrees from the plane of the drill tip. Behind this is ground a secondary relief of 25 to 30 degrees. The important part (and why you will not produce this kind of tip, hand held against the bench grinder in a hurry) is that all 4 facets MUST intersect at a single point. However, given a Quorn and some
accurate, concentric way of holding the drill in the precise axis of the Toolholder Bracket, the Quorn will produce this tip perfectly with very little effort. The steps are: