Shop made wheel dresser example
canadianhobbymetalworkers.com
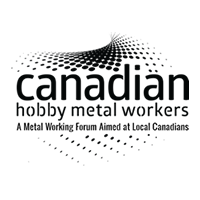
Toolpost grinding wheel dresser
I wanted something rigid & adaptable I could set up quickly on the lathe for wheel dressing in whatever orientation the wheel diameter happened to present. Then knock it down quickly without fuss but preserve the height setting if required again. The parts are just from scrap box metal on hand...
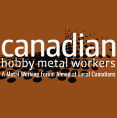