Tomc938
Ultra Member
I have my esp32 dev boards flashed and working with my Tablet - it connects anyway.
I spent the last two days using Fusion 360 electronics project design to reproduce Yuriy's schematic for the ESP32 scale adapter (https://www.touchdro.com/resources/adapters/diy/esp32-diy-dro.html) and figuring out how to find components, define components, place components (in the schematic and the PCB board) and all the other little things I needed to learn to use Fusion 360. Some things were not intuitive - once you choose a component, you hit "return" and then you can place the component. No click and drag option. but I gotta say, when it comes to figuring out the traces for the PCB board, Fusion is a thing of beauty! I deleted the traces and had it re-wire things for me a few times. Sometimes because I made significant changes in components and layout, and sometimes just for the fun of watching it work.
I added 3.3 and 5v power, and LED to show when the unit is on, and switch to turn it on (and off - I thought of everything).
I a not sure what kind of connectors I will use. Yuriy suggests DB9, but the free version of Fusion only allows a maximum of 100 mm x 100 mm PBC, and there wasn't room on the back. So I went with small terminal blocks I can wire them, or whatever kind of connector I decide to use, after the board is built.
So here's the 3D rendering of the board. I'm open to any positive suggestions anyone may have. It's gone through a lot of revisions and I may do a few more tweaks before getting the boards made. I have enough material to make 2 adapters. One for my milling machine snd one for my lathe. Both will just have X and Y axis for now, but I can add more at any point.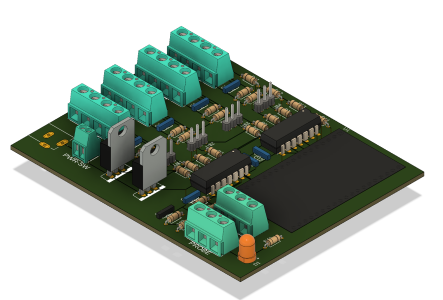
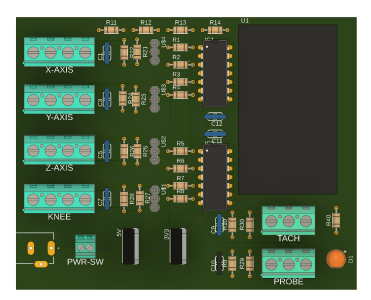

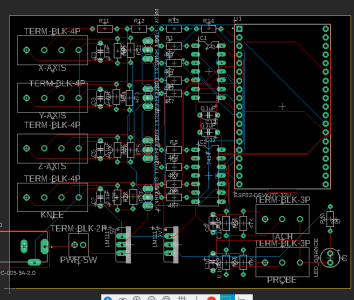
I spent the last two days using Fusion 360 electronics project design to reproduce Yuriy's schematic for the ESP32 scale adapter (https://www.touchdro.com/resources/adapters/diy/esp32-diy-dro.html) and figuring out how to find components, define components, place components (in the schematic and the PCB board) and all the other little things I needed to learn to use Fusion 360. Some things were not intuitive - once you choose a component, you hit "return" and then you can place the component. No click and drag option. but I gotta say, when it comes to figuring out the traces for the PCB board, Fusion is a thing of beauty! I deleted the traces and had it re-wire things for me a few times. Sometimes because I made significant changes in components and layout, and sometimes just for the fun of watching it work.
I added 3.3 and 5v power, and LED to show when the unit is on, and switch to turn it on (and off - I thought of everything).
I a not sure what kind of connectors I will use. Yuriy suggests DB9, but the free version of Fusion only allows a maximum of 100 mm x 100 mm PBC, and there wasn't room on the back. So I went with small terminal blocks I can wire them, or whatever kind of connector I decide to use, after the board is built.
So here's the 3D rendering of the board. I'm open to any positive suggestions anyone may have. It's gone through a lot of revisions and I may do a few more tweaks before getting the boards made. I have enough material to make 2 adapters. One for my milling machine snd one for my lathe. Both will just have X and Y axis for now, but I can add more at any point.
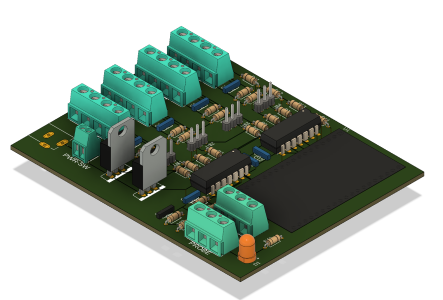
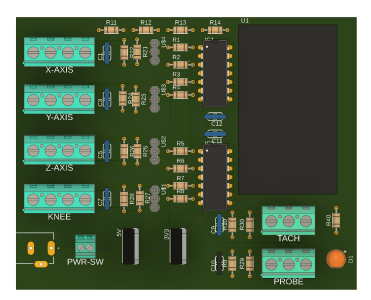

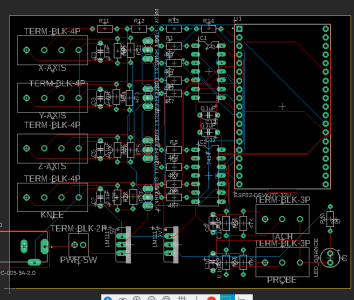