Here's my next revision and why one shouldn't really do things in the machine shop it there's even the slightest idea there might be COVID brain fog.
I found a short piece of 1/2" stock. Long enough to hold in the 1/2" 5C Collet for transfer to the Spin Indexer on the mill.
I was careful. Used my ELS for the exact metric lengths required. Came out perfect. The XL series pulley that needs a keyslot slid on with no friction and no play. I'm usually never that good.
Then on to the mill. First I put a 7/8" rod about 16" long into the spin indexer. Used my probe to ensure it was parallel to the X axis on the table so the key slot I'd eventually carve would be straight. Perfect!
Swap in this little guy. Find the center line by probing front and back using the probe on either side icon.
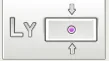
Well that operation wiped off the probe needle so fast I couldn't get to the ESTOP fast enough. No idea why. Luckily it didn't shatter the probe like I did the last time.
I used my old standby that makes electrical contact to find the center. Then positioned the touch probe again over the center line this time to establish the Z=0 position. This is where the brain fog starts to show.
Click on on the probe surface button. Perfect.

Do a tool change to remove the probe and insert the 3mm end mill holder. Verified the length was correct in the tool table. All looked good.
Jogged a line at a time in the G-Code.
The G0 Z0.235 should have put the tool bit just above the part and then stopped so I could measure and check clearance.
BANG!
Bits of HSS embedded in the softer steel. Collet has marks (it was turning) against the 5C collet.
AC Servo on Z axis faulted out for encoder not going where motor was told to go. Possibly even the spindle faulted. By then I'd hit the ESTOP.
I tried to clean up the area on the but it's not as pretty as it used to be.
So what went wrong?
Late tonight I finally figured it out. To make this long story short, after I had damaged my first 3 way probe I made a spindle button probe just to be able to set Z=0. That probe was much shorter. The new replacement probe arrived in June or July. I did testing and then went on and did other things.
Totally forgot to change from the short Z axis button probe to the longer (by 2" needle probe). The system thought the 3mm mill was 2" further from the part than it actually was. ie. At about 2.235" and it was trying to reach 0.235". At 150 ipm.
Once I edited the tool table and the INI file parameters for this expensive fixed length probe I went down and tried it again. This time the probing and tool length works.
I'll go through and do a full calibration again just to get the precise value but moral of the story. Don't play in the shop with COVID fog brain.