JohnW
(John)
Here is the next part of the brake mechanism. This is looking through the left hand pedestal from the end. You can see the brake lever from the previous post in the opening. This picture was taken before the braking resistors were installed. They would be in the upper right corner of this picture. I made up a new bracket to hold the brake switches. Originally there was only one switch and it used a bit of an ugly bracket that was mounted a bit further to the left than my new switches. The big spring is what keeps the brake held in the off position.
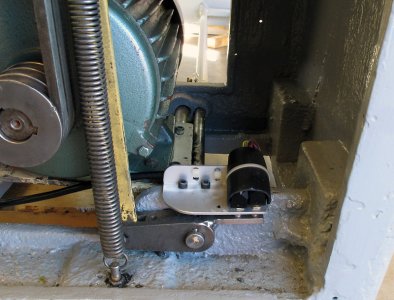
Here is a close-up of the switches and the brake lever. I added the tab on the right side of the lever to actuate the switches. The switches are setup up to provide two signals depending on how far the brake lever is pushed. The right hand switch clicks with the slightest movement of the lever. That way a light tap on the brake lever will tell the lathe to stop and use a normal decel curve (2-secs). A light tap is not enough to actuate the physical brake. The physical brake is applied by pushing the yellow bar up. Look way back to an early posting in this thread to see what happens up there.
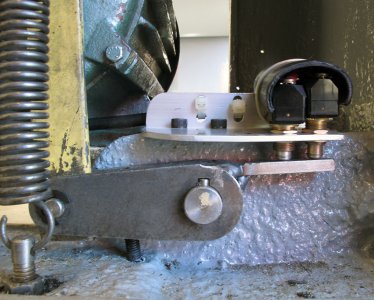
Pressing harder on the brake lever will actuate the physical brake and the left hand switch. That switch sends a DC braking signal to the VFD telling it to stop as quickly as it can.
The micro-switches have a short piece of (split open) plastic tubing tie-wrapped over them to protect them from stuff falling on them. If a big metal filing were to fall on top of them it could short the contacts, so this way that will not happen. The extra holes in the bracket are used as a stress relief for the cable running back to the control box.
So the manual brake works as follows:
Here is the wiring diagram for the brake switches:
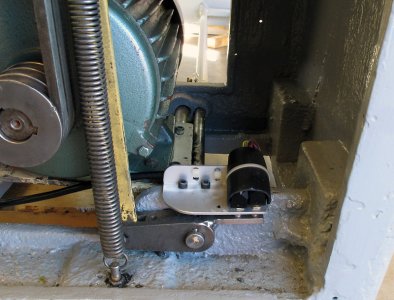
Here is a close-up of the switches and the brake lever. I added the tab on the right side of the lever to actuate the switches. The switches are setup up to provide two signals depending on how far the brake lever is pushed. The right hand switch clicks with the slightest movement of the lever. That way a light tap on the brake lever will tell the lathe to stop and use a normal decel curve (2-secs). A light tap is not enough to actuate the physical brake. The physical brake is applied by pushing the yellow bar up. Look way back to an early posting in this thread to see what happens up there.
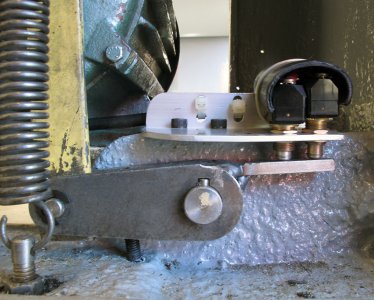
Pressing harder on the brake lever will actuate the physical brake and the left hand switch. That switch sends a DC braking signal to the VFD telling it to stop as quickly as it can.
The micro-switches have a short piece of (split open) plastic tubing tie-wrapped over them to protect them from stuff falling on them. If a big metal filing were to fall on top of them it could short the contacts, so this way that will not happen. The extra holes in the bracket are used as a stress relief for the cable running back to the control box.
So the manual brake works as follows:
- Press it lightly to stop the motor normally using a 2-second ramp-down. To restart, the FNR lever must be returned to N and then to F or R.
- Press it hard to both apply the physical brake and tell the VFD to stop the motor as quickly as possible. This is the real emergency stop mode since it is way more effective than just killing the power. The lathe is stopped as quickly as possible in this mode.
- Use this hard press on the brake for emergency stops, and to quickly stop when machining up to a shoulder
Here is the wiring diagram for the brake switches: