JohnW
(John)
Here is another minor issue and the fix my lathe got a couple of weeks ago:
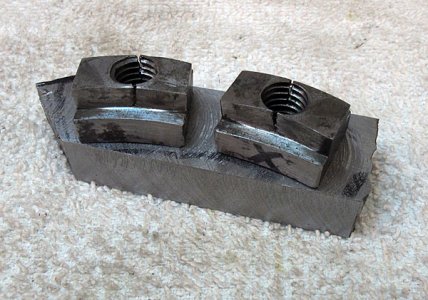
The curved t-nuts that hold the vice to the cross slide were both cracked and a bit bent from over-tightening over the years. Here are the old nuts on top of a piece of hot rolled scrap that has already been through the mill to square it up and remove the scale.
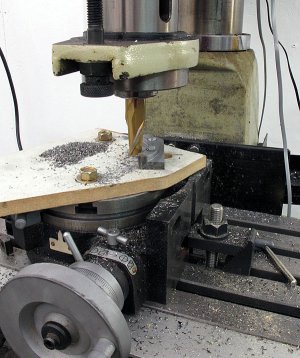
I drilled and threaded the two holes first, then bolted it from the bottom with countersunk heads into to a sacrificial piece of MDF that I bolted to my rotary table at exactly the radius of the circular vice hold down slots in the cross slide. This lathe has a strange mixture of metric and SAE fasteners. The vice t-nuts are 3/8-16. There are lots of 1/4-20's holding on access panels yet most of the other bolts are 5mm, 6mm and 8mm.
Once I had it carefully mounted in position it was just a matter of taking a bunch of small passes with an end-mill while rotating the table to hew out one large curved t-nut. I had a lot of vibration from the MDF flexing. I should have used 3/4" instead of 1/2", but that is what I had lying around. Still, it worked OK by keeping the cutting passes less than about 0.020" of Z motion.
This time I remembered to grab the camera in the middle of the machining operation. This is when the narrow part of the nuts have been cut. I then moved the table in the X direction and cut the curves for the shoulders of the nuts. Since it was mounted on MDF, I just cut right into the MDF to finish the sides.
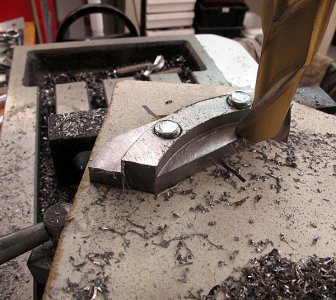
I cut the piece in half and got two nicely fitting curved t-nuts. The nuts sit about 0.020" below the surface when they are pulled up so they will allow the vice to be clamped down nicely. They are a bit longer than the originals, and are as long as they can be and still fit through the slot in the bottom that they must be inserted through.
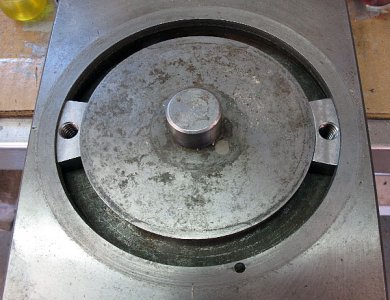
Here is a comparison of the old and new parts:
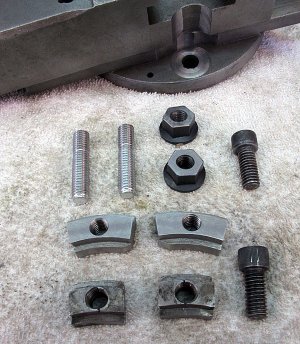
The originals used bolts that threaded into the t-nuts. I think that contributed to the failure since it eventually wore out the threads, and forced the bolt to hold in the top, very thin portion of the nut.
Instead, I made a couple of studs out of two grade five 3/8" bolts with rolled threads. I have lots of 3/8" ready rod around, but I do not think they are made of very strong metal. I had to extend the threads on the bolts a bit to make the studs - you can see where that started since the bolt is a little bit small right at the end of the rolled threads and leaves a short bit of missing thread on the stud.
I put the studs into the t-nuts and glued them in place with JB weld while keeping a bit of tension on the studs so they would be metal-to-metal while under tension. That way the rolled threads are sticking up and will see the stress and wear instead of my cut threads, the studs won't loosen, and the JB will add some strength to help stop the nuts from splitting like the previous ones. There is still very little metal on each side the threaded holes near the top.
The chamfered edges of the t-nut shoulders was not intentional. That was just the edge of the original metal. The new nuts still have a longer shoulder than the originals.
I had a couple of nice 3/8" shoulder nuts from a small hold-down kit I have for my rotary table. I'll e-bay some replacements out of China some day, but this was a better use for them for now. The nuts were just a bit too tall to fit properly on the vice, so I did two things there. I milled down the nuts a bit, and I took a 1" end mill and cleaned up the mounting surface on the vice by cutting out 0.040" or so. The vice mounting flange was a bit beat up at the edges of the holes by the small surface area of the original hex head mounting bolts.
The other reason I went with the studs is that I prefer to be able to use a wrench to tighten the vice over using an Allen key. With a nice polished surface on the bottom side of the nuts, and a large smooth surface on the vice mounting flanges, the vice can now be tightened very smoothly without moving while the nuts are turned.
And the final result:
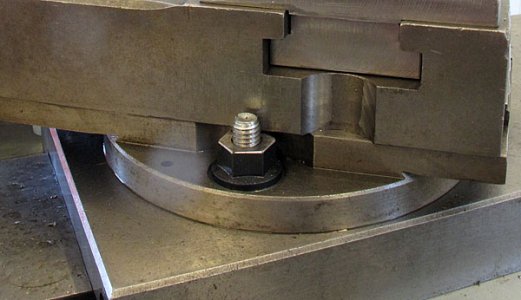
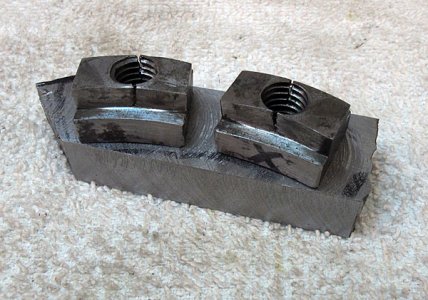
The curved t-nuts that hold the vice to the cross slide were both cracked and a bit bent from over-tightening over the years. Here are the old nuts on top of a piece of hot rolled scrap that has already been through the mill to square it up and remove the scale.
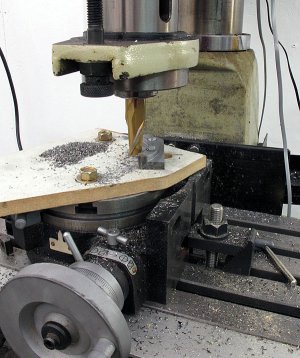
I drilled and threaded the two holes first, then bolted it from the bottom with countersunk heads into to a sacrificial piece of MDF that I bolted to my rotary table at exactly the radius of the circular vice hold down slots in the cross slide. This lathe has a strange mixture of metric and SAE fasteners. The vice t-nuts are 3/8-16. There are lots of 1/4-20's holding on access panels yet most of the other bolts are 5mm, 6mm and 8mm.
Once I had it carefully mounted in position it was just a matter of taking a bunch of small passes with an end-mill while rotating the table to hew out one large curved t-nut. I had a lot of vibration from the MDF flexing. I should have used 3/4" instead of 1/2", but that is what I had lying around. Still, it worked OK by keeping the cutting passes less than about 0.020" of Z motion.
This time I remembered to grab the camera in the middle of the machining operation. This is when the narrow part of the nuts have been cut. I then moved the table in the X direction and cut the curves for the shoulders of the nuts. Since it was mounted on MDF, I just cut right into the MDF to finish the sides.
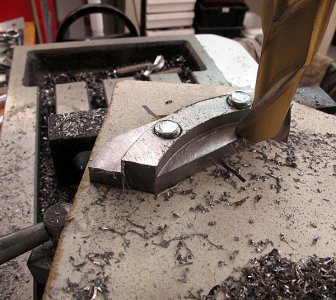
I cut the piece in half and got two nicely fitting curved t-nuts. The nuts sit about 0.020" below the surface when they are pulled up so they will allow the vice to be clamped down nicely. They are a bit longer than the originals, and are as long as they can be and still fit through the slot in the bottom that they must be inserted through.
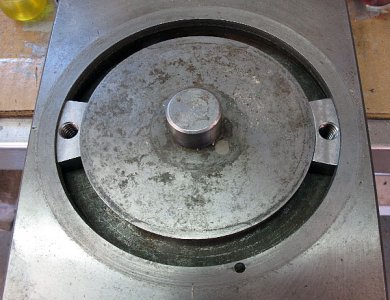
Here is a comparison of the old and new parts:
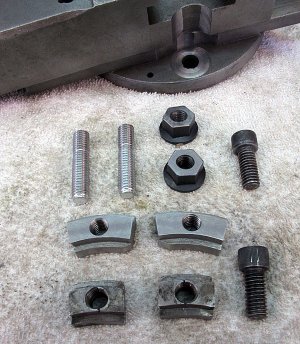
The originals used bolts that threaded into the t-nuts. I think that contributed to the failure since it eventually wore out the threads, and forced the bolt to hold in the top, very thin portion of the nut.
Instead, I made a couple of studs out of two grade five 3/8" bolts with rolled threads. I have lots of 3/8" ready rod around, but I do not think they are made of very strong metal. I had to extend the threads on the bolts a bit to make the studs - you can see where that started since the bolt is a little bit small right at the end of the rolled threads and leaves a short bit of missing thread on the stud.
I put the studs into the t-nuts and glued them in place with JB weld while keeping a bit of tension on the studs so they would be metal-to-metal while under tension. That way the rolled threads are sticking up and will see the stress and wear instead of my cut threads, the studs won't loosen, and the JB will add some strength to help stop the nuts from splitting like the previous ones. There is still very little metal on each side the threaded holes near the top.
The chamfered edges of the t-nut shoulders was not intentional. That was just the edge of the original metal. The new nuts still have a longer shoulder than the originals.
I had a couple of nice 3/8" shoulder nuts from a small hold-down kit I have for my rotary table. I'll e-bay some replacements out of China some day, but this was a better use for them for now. The nuts were just a bit too tall to fit properly on the vice, so I did two things there. I milled down the nuts a bit, and I took a 1" end mill and cleaned up the mounting surface on the vice by cutting out 0.040" or so. The vice mounting flange was a bit beat up at the edges of the holes by the small surface area of the original hex head mounting bolts.
The other reason I went with the studs is that I prefer to be able to use a wrench to tighten the vice over using an Allen key. With a nice polished surface on the bottom side of the nuts, and a large smooth surface on the vice mounting flanges, the vice can now be tightened very smoothly without moving while the nuts are turned.
And the final result:
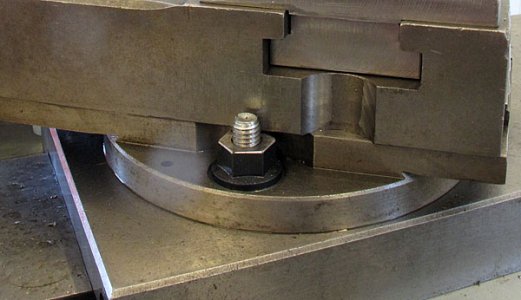
Last edited: