The next issue at hand is the side cover. I have noticed that many old machines like these are missing the side cover. Options, do nothing, a sheet metal cover, cast an aluminum cover. Option number 3 it is.
There is a fair bit to cover here and it will take me several posts. Here I go. I did this based on pictures and video that I have seen on YouTube and the internet. It is a guess for sizing.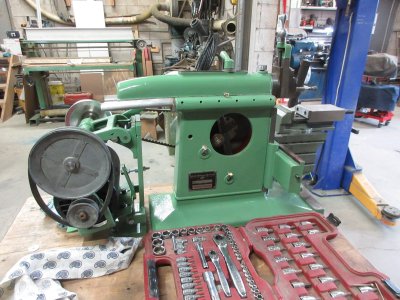
Patterns are normally made from soft tight grain wood like basswood or willow. I have some basswood in the shop that is big enough for this small pattern I will be making and I do not need to joint and glue boards together. A 7" square blank 2" thick is cut and fastened to the Harrison face plate.
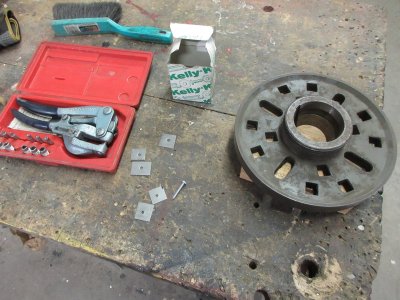
I know some will say you should not turn wood on a metal lathe, soaks up the oil, jams under the ways. Okay that is correct, but I sold my Beaver bench top wood lathe years ago, that did not go well, but that is for another time.
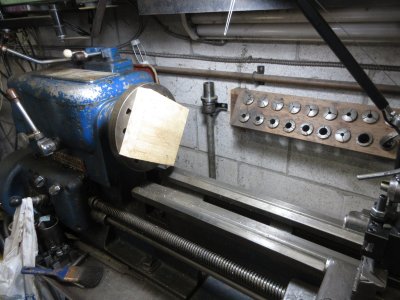
The blank is faced to make it flat and then turned to size.
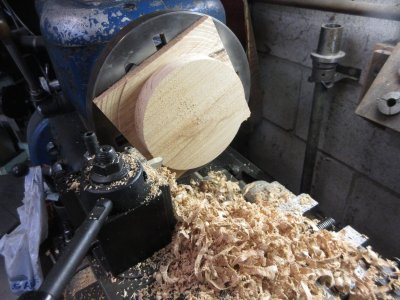
Then turned over and turned to size of the opening, minus the flange.
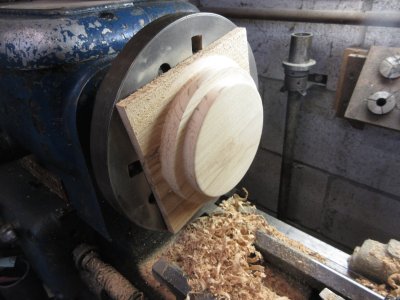
Then cut from the blank, remember one of these. My arm is sore and I had to stop 4 times. The saw is a bit dull as well, but I managed.
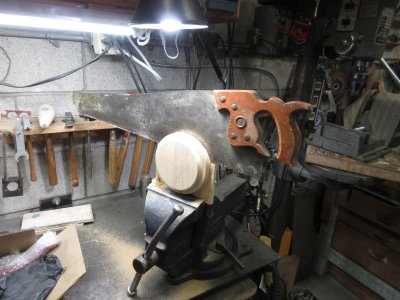
The part is too big to chuck in my Harrison as I don't have outside jaws for the chuck so I fastened it to the face plate of my Myford ML7.
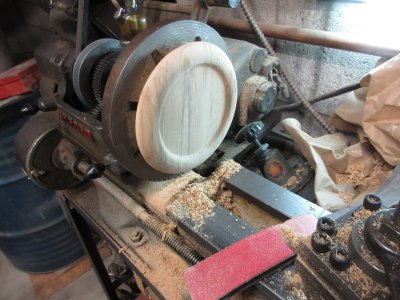
Test fit on the shaper.
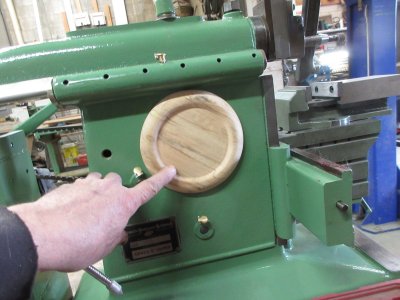
Looking at old pictures a section remains for the fastening knob. It is easier to install with a bit of bondo then mill the centre.
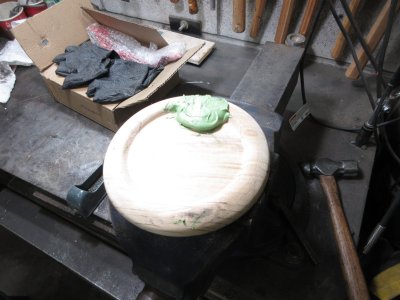
Ready for some paint. I just use engine enamel from a spray can.
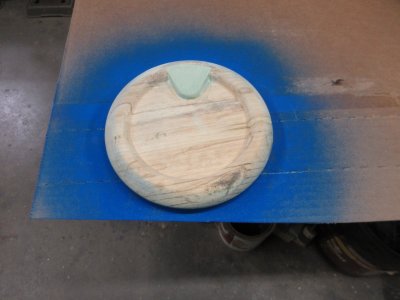
Several coats of paint are required to seal the grain on the wood. A removable Tang is fitted, as it needs to be removable for ramming the sand around the pattern.
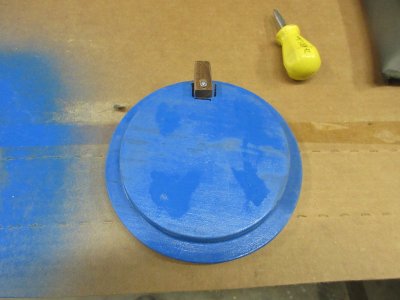
A nail board is used so that I can paint of both sides without waiting for one side to dry.
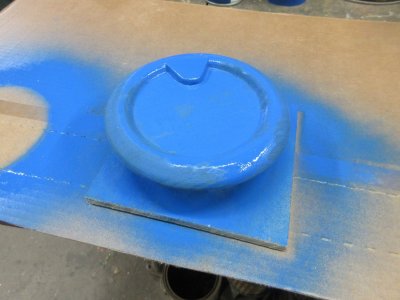
There is a lot still to come on this, but that is the way it goes. I did shoot video as well, when I get a chance I will assemble and post to my YouTube channel.
TonyK.
Grimsby Ontario Canada.
There is a fair bit to cover here and it will take me several posts. Here I go. I did this based on pictures and video that I have seen on YouTube and the internet. It is a guess for sizing.
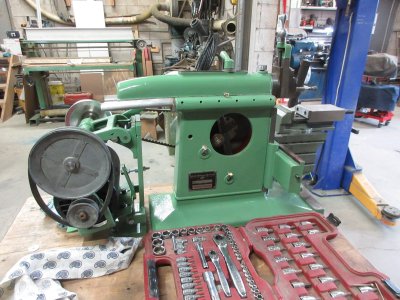
Patterns are normally made from soft tight grain wood like basswood or willow. I have some basswood in the shop that is big enough for this small pattern I will be making and I do not need to joint and glue boards together. A 7" square blank 2" thick is cut and fastened to the Harrison face plate.
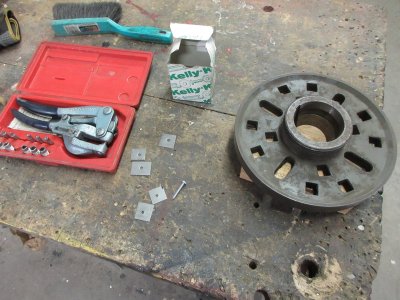
I know some will say you should not turn wood on a metal lathe, soaks up the oil, jams under the ways. Okay that is correct, but I sold my Beaver bench top wood lathe years ago, that did not go well, but that is for another time.
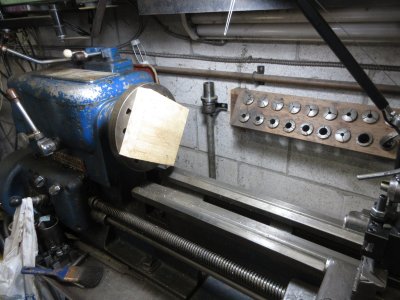
The blank is faced to make it flat and then turned to size.
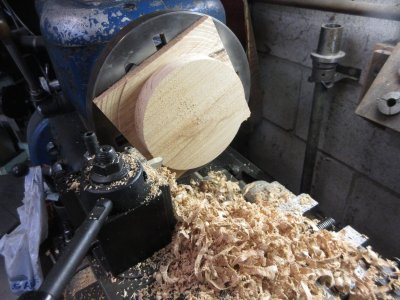
Then turned over and turned to size of the opening, minus the flange.
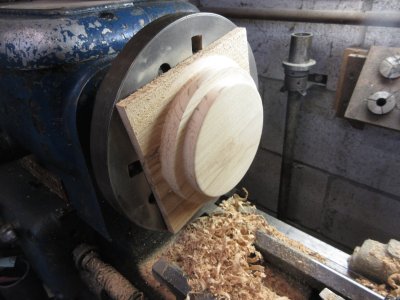
Then cut from the blank, remember one of these. My arm is sore and I had to stop 4 times. The saw is a bit dull as well, but I managed.
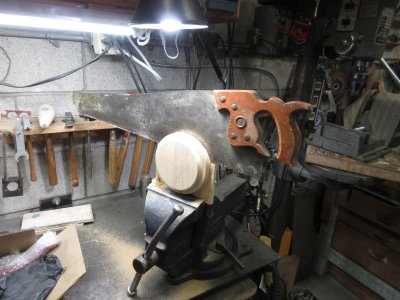
The part is too big to chuck in my Harrison as I don't have outside jaws for the chuck so I fastened it to the face plate of my Myford ML7.
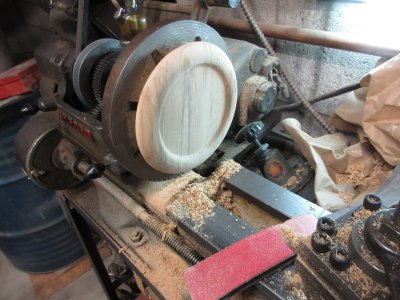
Test fit on the shaper.
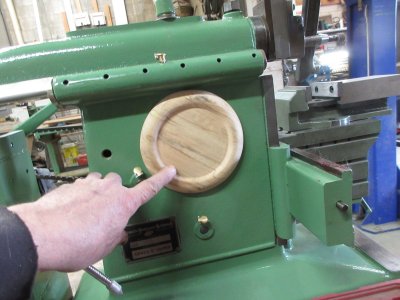
Looking at old pictures a section remains for the fastening knob. It is easier to install with a bit of bondo then mill the centre.
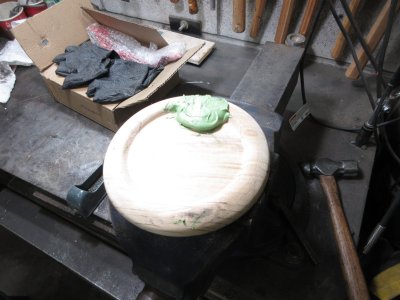
Ready for some paint. I just use engine enamel from a spray can.
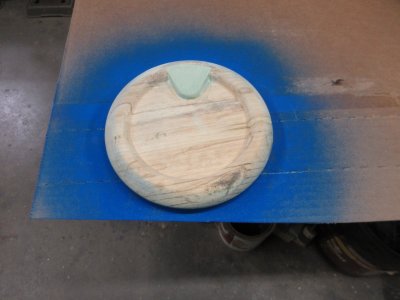
Several coats of paint are required to seal the grain on the wood. A removable Tang is fitted, as it needs to be removable for ramming the sand around the pattern.
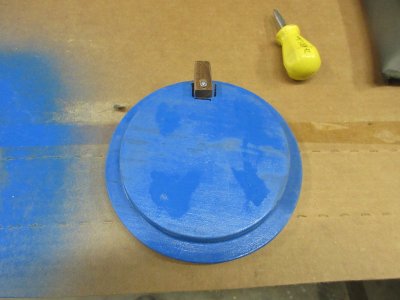
A nail board is used so that I can paint of both sides without waiting for one side to dry.
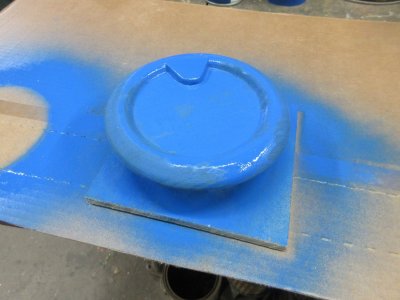
There is a lot still to come on this, but that is the way it goes. I did shoot video as well, when I get a chance I will assemble and post to my YouTube channel.
TonyK.
Grimsby Ontario Canada.