Sorry for the departure, back to making a side cover for the Ammco shaper. The heat. To the left a bucket of anthracite coal, takes a bit to get it going but once fired you can cut a tree limb and put it on top and it will burn. Next a spreader hook to lift the melting bucket or crucible ( not really) and hanging on the wall another single hook to tilt the bucket for the pour and finally a brick lined stove. That too came from the fellow that sold me the lathes on condition if he wanted it back he could have it. Seeing that he died in 2015 that deal has expired.
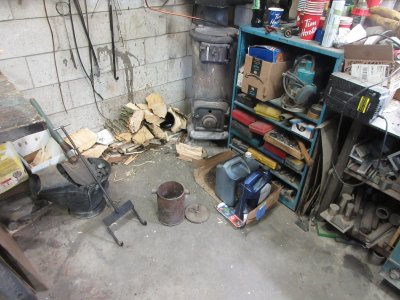
A small bucket of scrap aluminum. Part of it is a cylinder head cut up which tend to be 7000 series aluminum, but for this project it really doesn't matter.
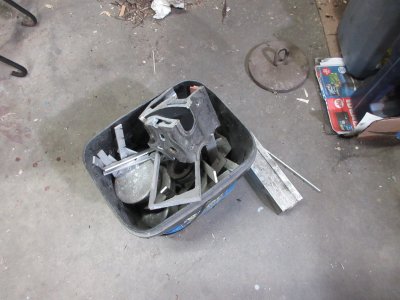
Starting of the melt.
At this point it is really better to have 2 people working as one can ram sand while the other tends to the fire. It is easy to get distracted and the fire dies down and it takes time to melt the aluminum.
I was having difficulty parting the molds without collapse, (3rd attempt) and because the flask was so big for the part ramming the sand just takes time. I decided to do a bit of a repair and move on as the aluminum was now ready to pour.
The short section of steel pipe is the funnel for the pour. I ram it up and then push that length of .010" wall stainless steel tube through the sand to make the gate or sprue. It is faster then trying to ram sand around a length of dowel. ( It is documented better in the video I took, still pending)
The casting floor. A sheet of metal is laid down on the concrete to prevent any molten aluminum should it leak from the pour will cause the concrete to spault and explode. ( not good) Fire bricks are used to set the melting pot on since the bottom is red hot and another section of metal pipe is used to pour the left over aluminum into an ingot. Aluminum, will shrink 2% from poured and will slide out of the pipe when cold without any effort.
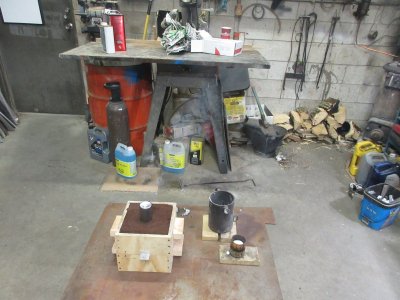
Digging out the part. As long as the part is left to cool, smoke is not an issue, it is the air getting to the hot sand and oil that will start to smoke. I left the part for 4 hours and dug it out.
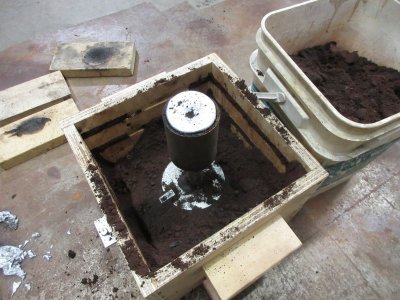
Here is the part, not my best work, a bit porous, I should have baked the sand that was rammed against the pattern a bit to dry out any moisture in the sand. The part is usable. Since it is not a structural part, a bit of bondo will make it look good.
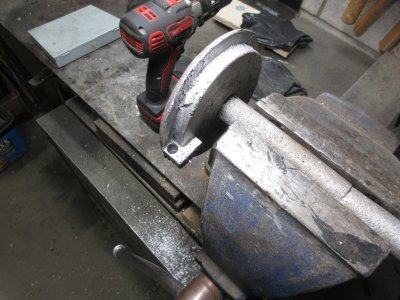
A bit of clean up with a rotary burr and I was ready for a test fit. Yes there was a bit of interference with the stroke adjusting nut to be covered in the next post.
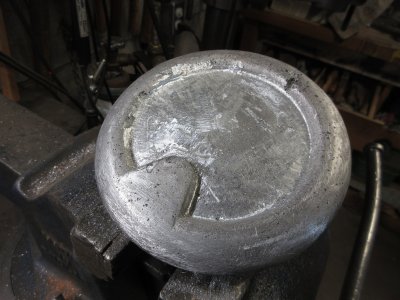
I will fill the bad spots with some bondo. I have done better casting than this. Been awhile.
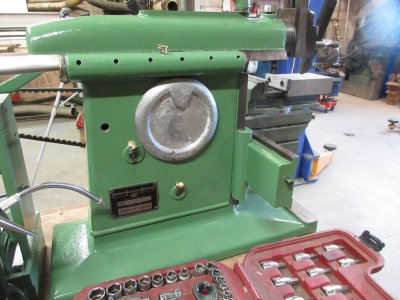
More to come, shower time.
TonyK.
Grimsby Ontario Canada.