Is this a slinger ring which is part of a case labyrinth seal?
View attachment 63970
Could it be that the negative pressure (slipstream) created by the prop is “pulling” the oil past the seal when doing static runs?
This could go away once the plane has some forward velocity and the pressure around the hub changes to positive?
Maybe you have too much blow-by in your cylinders, pressurizing the crankcase?
Yes the slinger is the oil seal, the only thing i do not have is a left hand thread on the exterior of the prop hub, and i knew that would create some level of oil loss, but it should not be as bad as im witnessing
this is a picture of the aerovee, they do not use a seal (i emailed them), you can see the very slight left thread cut into the od
i did not do a leak down, so i cannot say for sure the blowby is not significant, i do not believe it to be significant, compression test numbers were all very good, and it does have good compression pulling the prop through. I think i will run the breather into the airbox, that should provide some negative pressure and help with some crankcase pressure, its currently vented
This is another option, sealant blocking this return passage, i feel this is very unlikely, this appears to be silicone, i used Permatex aviation form-a-gasket, it is very thin, and drys very thin, that passage is relatively large, i dont think i could plug that passage with aviation form-a-gasket even if i tried
I did not consider the slipstream causing a negative pressure, i could see this being possible, the oil doesnt just seep out and leak down the front of the engine, it is thrown all the way out onto the right exhaust pipe, thats a pretty long ways so its possibly making its way into the slipstream
this is the oil seal that is/was used by great plains, National 6815, it has the right ID, is inexpensive, it is 6.35mm tall overall, thats the only issue. I think i could modify it by cutting down the height and installing it "backwards" to the conventional install (into a wheel shaft or whattever). I of course would need to cut it in half, but this has been done successfully by others. i think this might be worth a shot, that combined with routing the breather into the airbox and maybe ? i will need to get a seal and do some measurements to see if the rubber will end up where i want it
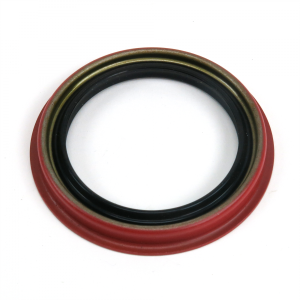
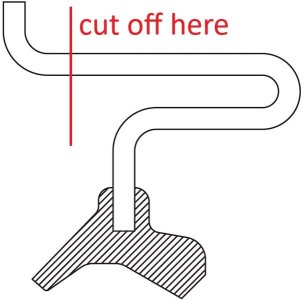