Xyphota
Ultra Member
I've read the water freezing trick in a few places, but maybe it just shouldn't be done on .6mm tubing. Filling the tube with sand and then welding caps on the end is supposedly a good bet, but that seems like a lot of work. I've read a few suggestions about just stuffing the tubes full of brass brazing rod or TIG filler wire, so maybe I'll try that if I decide to try a 5"R bend on this tubing again. Although, I really should get the proper tubing diameter die first.
I kind of want to try and make a mandrel attachment for my di-acro no.2 bender. It'd have to be a bit convoluted as the mandrel would have to rotate with the handle as the bending die is stationary. I haven't seen it done before so maybe that implies its a dumb idea LOL.
Alternatively, maybe I should sell my di-acro bender and buy one of these:
stakesys.co.uk
A bit pricey, but if I can make the dies it wouldn't be too bad.
I kind of want to try and make a mandrel attachment for my di-acro no.2 bender. It'd have to be a bit convoluted as the mandrel would have to rotate with the handle as the bending die is stationary. I haven't seen it done before so maybe that implies its a dumb idea LOL.
Alternatively, maybe I should sell my di-acro bender and buy one of these:
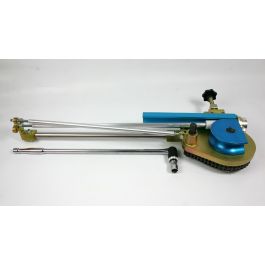
MK5 Mandrel Tube Bender
For tight radius bends in thin walled mild steel, stainless and aluminium tube and pipe
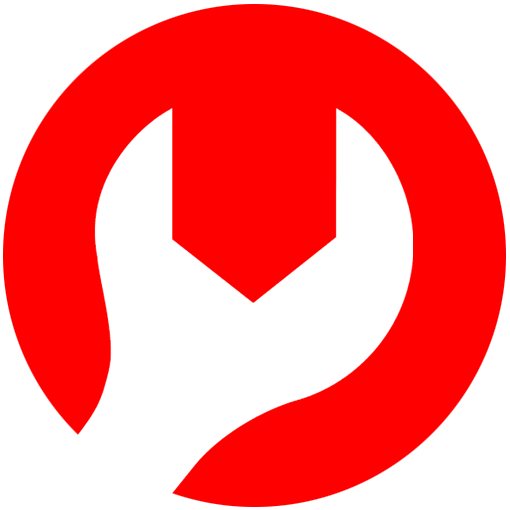
A bit pricey, but if I can make the dies it wouldn't be too bad.
Last edited: