Hello folks.
My King USA mill started to act erratically for some time. I decided to have a look and yesterday removed table and started diagnosing. To my utter disappointment I discovered that nuts (there are two to take up a slack) are worn completely. I am not sure how this is happened - mill was always generously lubricated, anyway - here is a picture
I will have to rebuild it, so several questions -
1. Is that leadcrew 5 TPI or 6 TPI ? Seems to be right handed? I am a bit confused...
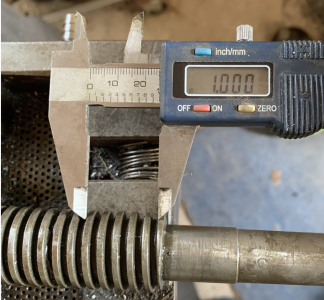
2. OD if this leadscrew is 1.129" - is there closest standard leadscrew. Nearest fractional size is 1 1/4 - does it look right to you, folks ?
3. Regarding fix - would be OK to bore internal diameter, have some decent wall thickness and then to make a threaded insert? OD of the threaded part is 1 3/4". Make a sliding fit, then to solder insert in pace ?
My King USA mill started to act erratically for some time. I decided to have a look and yesterday removed table and started diagnosing. To my utter disappointment I discovered that nuts (there are two to take up a slack) are worn completely. I am not sure how this is happened - mill was always generously lubricated, anyway - here is a picture
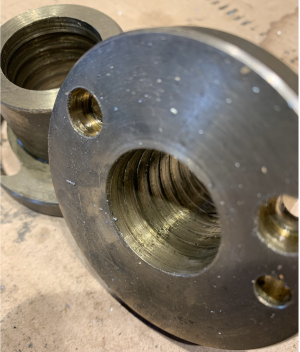
I will have to rebuild it, so several questions -
1. Is that leadcrew 5 TPI or 6 TPI ? Seems to be right handed? I am a bit confused...
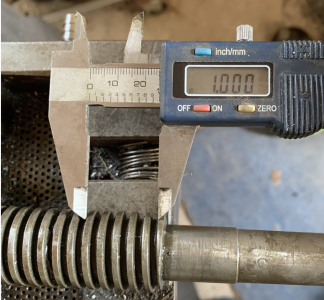
2. OD if this leadscrew is 1.129" - is there closest standard leadscrew. Nearest fractional size is 1 1/4 - does it look right to you, folks ?
3. Regarding fix - would be OK to bore internal diameter, have some decent wall thickness and then to make a threaded insert? OD of the threaded part is 1 3/4". Make a sliding fit, then to solder insert in pace ?