I ordered this spindle motor from bangood today. Just need to find an ER11 1/4" collet to accomodate better grinding stones.
Gotta be better than a Dremel.....
m.banggood.com
Gotta be better than a Dremel.....
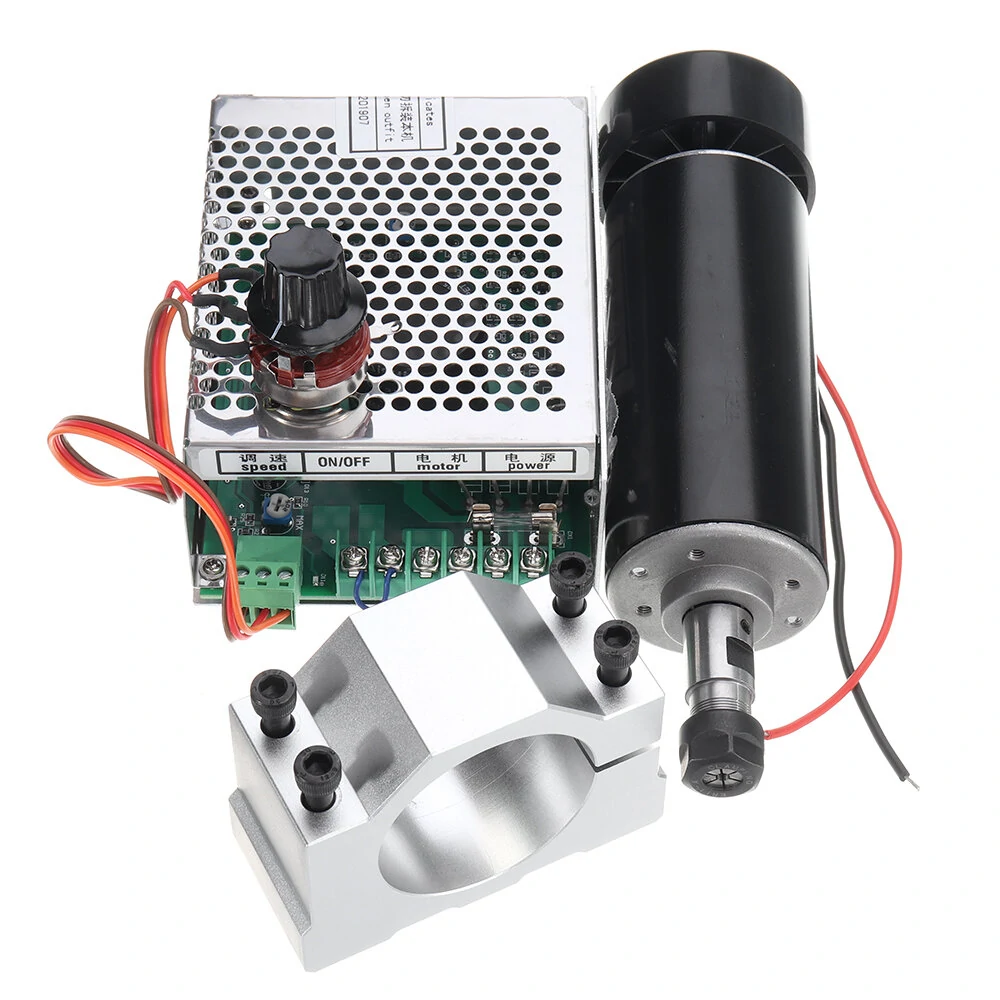
[CA$96.84 32% OFF] Machifit ER11 Chuck CNC 500W Spindle Motor with 52mm Clamps and Power Supply Speed Governor Machine Tools & Accessories from Tools on banggood.com
Machifit ER11 Chuck CNC 500W Spindle Motor with 52mm Clamps and and Power Supply Speed Governor For CNC Machine, Air cooled 0.5kw Air cooled spindle ER11 chuck CNC 500W Spindle Motor + Power Supply
