deleted_user
Super User
@TorontoBuilder check these out....
![]()
Mill Speed Controller
My BB CT129 milling machine uses a 90 volt DC motor with a KBIC-120 variable speed control. Speed is set using a simple rotary pot. There is an auxiliary input that stops the motor without disconnecting power to the speed control. My last project was to build a non-contact tachometer with a...canadianhobbymetalworkers.com
![]()
Bridgeport Mill Tachometer
I am pulling together a control box for my Bridgeport Mills. It is mainly to facilitate VFD controls like a fwrd/rev switch and a frequency Potentiometer. But I have a hankering to be able to see the actual spindle speed. My best idea to do this so far is a hall effect transducer on the nose...canadianhobbymetalworkers.com
Thanks for the links. I'll read them shortly.
Have a look at these for my current lathe project:
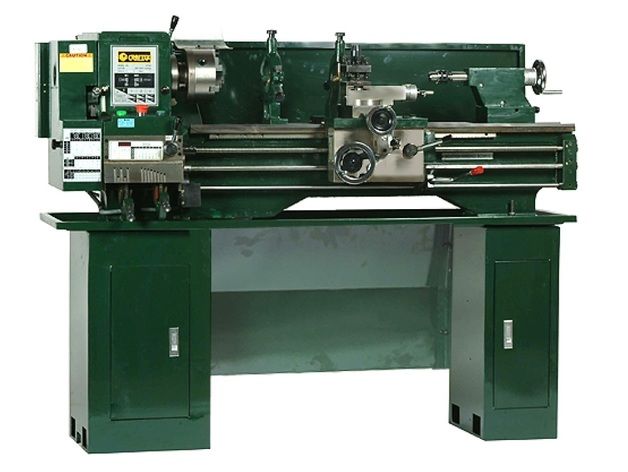
12" x 36" metal lathe VFD conversion and upgrades by TorontoBuilder
When the motor died on our Craftex CT041 12" x 37" gap bed metal lathe my brother and I took the opportunity to make a few planned upgrades including converting the lathe to a 2 HP 3 phase motor with an AT1-2200X variable frequency drive for greater speed control and low end torque. Such a lathe...
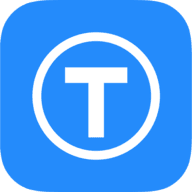
and
https://www.thingiverse.com/thing:5178575
I just can't leave it alone. I'm just sitting watching my 3d printer print a new front panel for my control box because I decided to add forward and reverse jog buttons. Why? Well I ordered what I thought were latching switches and I got momentary switches. So I couldn't let them go to waste.