@That-Guy, thank you for the kind words.
I put the gearbox back together minus the one missing gear, so I only have 2 high and 2 low.
It's enough to get it spinning under power, man is this machine loud, I've never run a gear driven lathe before so I'm sure they are louder than belt driven but this is so loud I have to wear ear muffs.
I also noticed while cleaning everything up that there are few other gears inside that have been remade, that is probably where the noise is coming from.
Also drilled out the drive pulley to 3/4" and tried my hand at broaching, it needed some fine tuning with a file but it's running true.
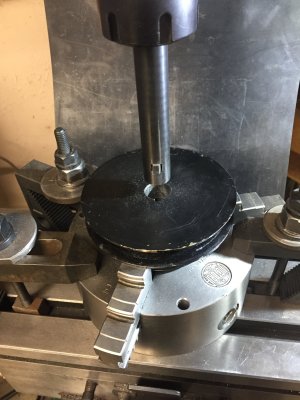
I finished up the tail stock today and mounted it, it looks a little strange being a completely different design than the original, but only me and some of you guys would notice it.
The base ended up just a hair lower than I wanted but a 0.008 shim took care of that. The first time I have ever used a fly cutter for the final cut on the tail stock base and wish I had set up a shower curtain around me and the mill, little crumbs of cast iron everywhere, 20ft. away.
I'm making chips!
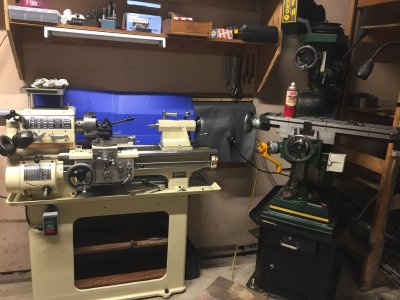
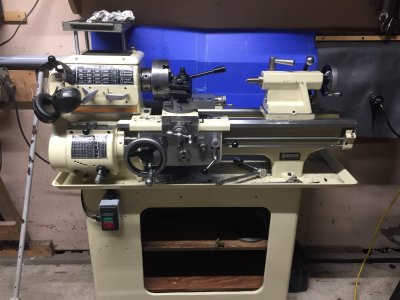
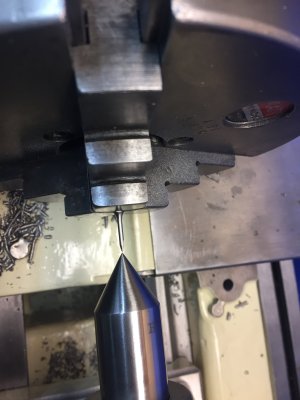
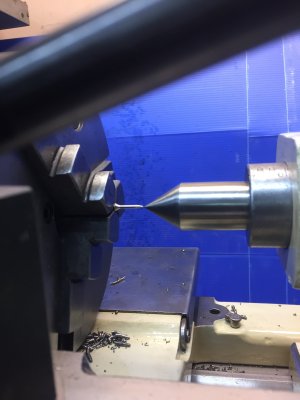
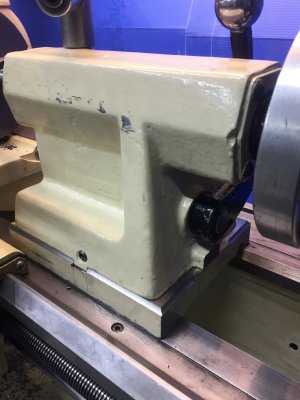
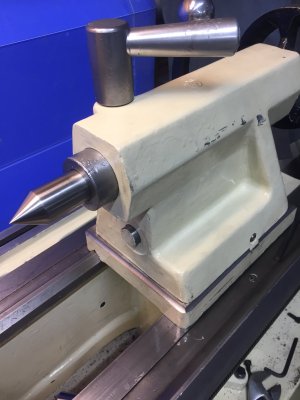
I put the gearbox back together minus the one missing gear, so I only have 2 high and 2 low.
It's enough to get it spinning under power, man is this machine loud, I've never run a gear driven lathe before so I'm sure they are louder than belt driven but this is so loud I have to wear ear muffs.
I also noticed while cleaning everything up that there are few other gears inside that have been remade, that is probably where the noise is coming from.
Also drilled out the drive pulley to 3/4" and tried my hand at broaching, it needed some fine tuning with a file but it's running true.
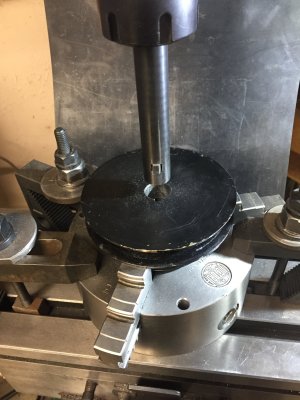
I finished up the tail stock today and mounted it, it looks a little strange being a completely different design than the original, but only me and some of you guys would notice it.
The base ended up just a hair lower than I wanted but a 0.008 shim took care of that. The first time I have ever used a fly cutter for the final cut on the tail stock base and wish I had set up a shower curtain around me and the mill, little crumbs of cast iron everywhere, 20ft. away.
I'm making chips!
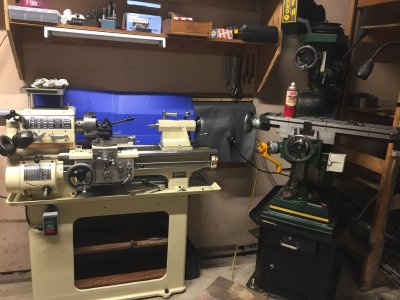
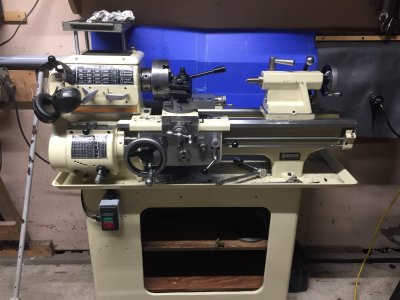
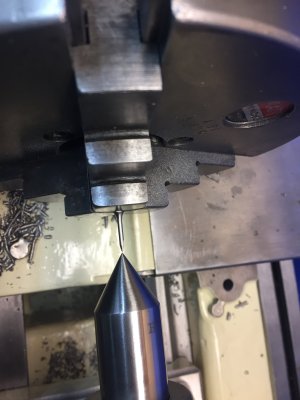
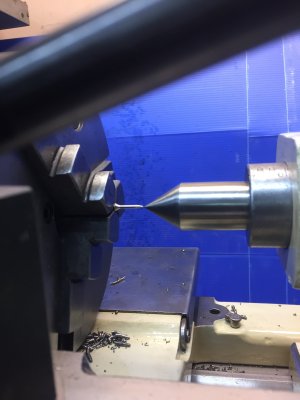
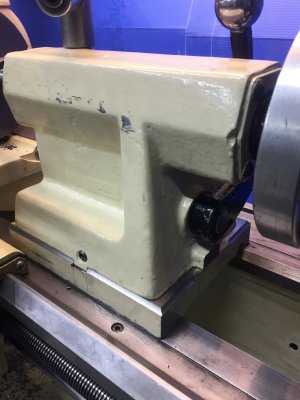
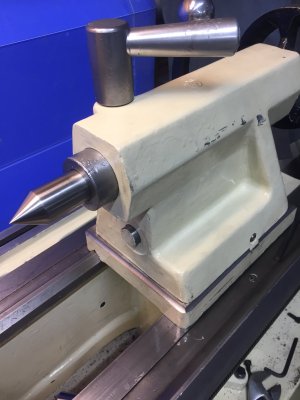