Had a good almost 4hour forging session this afternoon. I think my arm might be too tired to lift a Guinness. But I'm trying. This is pretty much being the 3rd time I've lit this forge and actually used it to make something, and the first session setup in the smithy with hood etc. I have gained a whole new appreciation for the youtubers that film their projects, and do a good job of it. I had such a hard time timing the heats and being able to take pictures that I kinda gave up trying to get progress pics, and just focused on the task at hand. It was just too difficult to maintain heat etc while trying to snap pics along the way. I'll try and get better....I need a good tripod, or articulating arm setup.
Anyway, the goal of today was to forge down a leaf spring into a spring for the post vise. But first I had to make some tongs to hold the spring. My tong selection thus far is terrible. A few weeks back I bought some cheap amazon plasma cut tong blanks. I figured this was the path of least resistance to get going quickly. They're a bit small, but adequate. The set came with 5 types, but I just finished the flat jaws for today. First I forged a taper on the tip, then twisted the jaw, drilled a rivet hole (I don't have punches yet.....) and then rounded the reins a bit, and riveted them together.
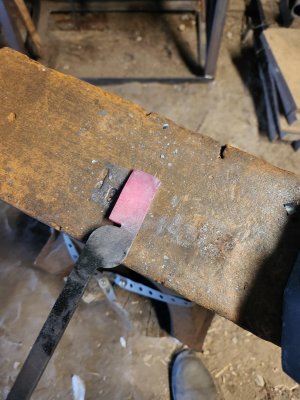
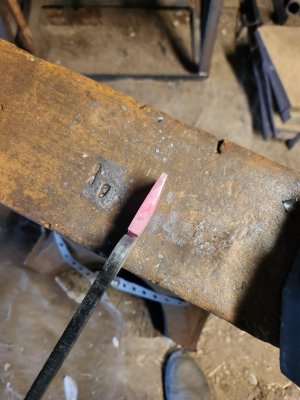
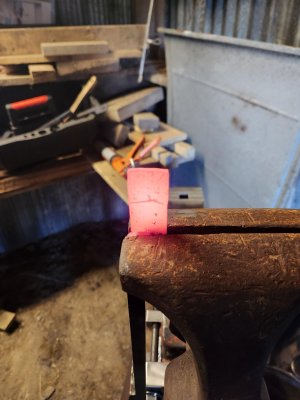
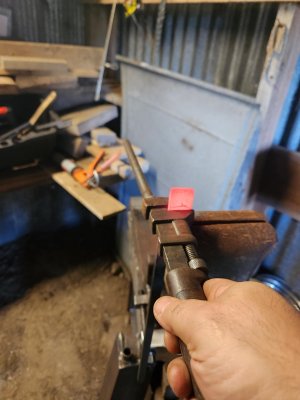
This is where I said eff it lol, and just put the phone down and got to business. Having to take extra heats because I couldn't do all the work in one because I was taking pictures.....I made a quick rivet punch this morning by plunging a ball enmill into the end of some O1, but I did such a terrible job of riveting this that it doesn't show lol. They work......(I will probably re-revit them at some point in the future). I didn't use the rivets that came with them, just some 1/4" rod.
Tongs done it was onto the spring. First I forged the thickness down to go under the clamp (2"-1.25"), then the curve. Took a few heats to get it all done, but it sure was fun
😀. Still have to do some fitting, and may have to take another heat to adjust, but it went pretty good. Once I get the size and fit right, I'll quench and temper. I don't think it's super critical in this application, I've seen guys make them from mild steel, but I want to anyway.
My Son popped out for a bit to crank the blower, and he took a few pics. In this one I had just hot cut the end to length, and am bending it back to snap off before turning the bend on the end. again, sorry for the lack of progress pics. I need to up my game in the photo dept and make it easier to get some good in progress pics....
And here's a finished pic. Vise is still assembled so it's tough to really check fit, but holding it up and measuring with the eyecrometer says it's close enough that it shouldn't need much work to fit.
It's funny. Setting up this shop has been a big job this past year. Feels like all my free time I've been making stuff, the forge(s), the hood, tools etc. Finally getting to use it all to actually make something was pretty awesome today. A big relief that all the hard work was worthwhile. Also as a beginner smith, with no experience, I skipped the whole beginner brake drum/hairdryer/charcoal stage, and jumped right in the deepend. A big commitement when one doesn't even know if they'll even enjoy it yet......BUT, all it really did was add about 10 more things to the "need to build" list lol. I need an oil quench tank, bucket of ashes to normalize stuff, Proper anvil stand, a bunch of bottom tooling, fullers, drift plates, drifts, punches.....etc. I come up with projects at a rate that far outpaces my ability and free time to finish them.
Soooo with that in mind, I decided to keep going, and forge some basic punches from coil spring.
First job was to straighten them out
Then I hot cut them in half
Then it was go time. You know that old saying too many irons in the fire? Ya, 4 at a time was a bit too much lol. Bumped it down to two at a time and it was enough to keep me busy working one while the other was heating up. I made a simple round punch, slot punch, round chisel, and ball punch. Just a few random pics when I had a break in the action....The round ones I tapered to square, then octagon, then round.
Then I turned them around and made a small octagon taper on the struck end.
and here's the days work. 4hours of hammering was about all my right arm could take. I dislocated my shoulder a few weeks ago doing something stupid, and while it's healing up fine, I don't want to push it. I'm not as young and in shape as I still think I am.....
Pretty productive day. I will grind the punches to shape, and harden/temper them after a first build a quench tank. I feel like there are a lot of rite of passage blacksmith projects, so I'm going to try and incorporate a few of those into every time I'm out there. Also make a pair of tongs everytime too......
Another thing I need out there is lighting. Pics make it seem a lot brighter than it actually is, but it's pretty damn dark in there. I ordered these for the garage shop yesterday, and they were here when I came back in the house. This is why I don't buy prime. Once I replace the florescent tubes in there with the LEDs, I'll put a couple of them out in the shed. I'll see if I have the motivation after dinner......I'm not banking on it.
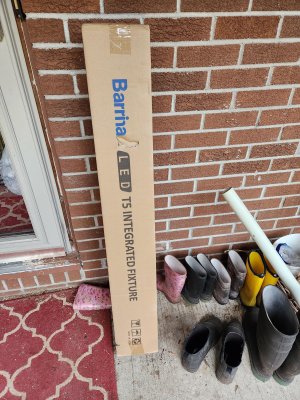