Here's a list of all the current activities. Like others, I jump around too much to have a dedicated thread for 1 activity, so I'll toss them together in this word salad of all things going on in my hobby shop.
The longest "active" project is the radial. Started it 10+ years ago. Didn't know squat about machining, cnc, etc. Been a learning experience. Lots of parts and need to remake a lot of them, but its getting closer. Optimistically - maybe a year or 2?
Next on the list is the B1 Springbok 5" gauge live steam locomotive. Bought as a chassis running on air. I've so far built the tender body 80%, and soldered up the insides of the boiler. Next up is boiler assembly, going to be a big job and waiting on spring weather to have a go.
After that is a Worthington duplex steam pump. I got distracted building the B1 boiler and needed some machining time, and the radial was at a difficult place for me so I started something new. This one is about 90% done. I may actually finish it...its all small but time consuming parts left (tube fittings, check valves and some silver soldering.)
Then its mostly either new things I shouldn't start yet, or tool / workshop fixes / upgrades etc.
In the list of things that I've started the mental exercises but really should not start until the above are done:
Gauge 1 (45mm between the rails) live steam "Green Arrow" locomotive (2-6-2) - fair amount of CAD done on parts I'd CNC
Some design work on making a functional direct injection diesel in small scale (~22cc - 28mm diam piston x 35mm stroke) - because I like a challenge...
I also have castings for a 1/4 scale Wright Whirlwind 9 cylinder for when I'm bored
A 3.5" gaugeBritannia Duchess part built chassis as received by my dad, who gave it to me to finish as he's smart enough to know when he has too many things to do.
Hopefully I'll be sharing some progress and wins along the way.
And pictures, always pictures. After this week at work I have had it reinforced in my head that nobody reads words
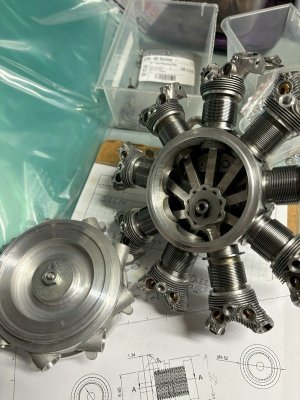
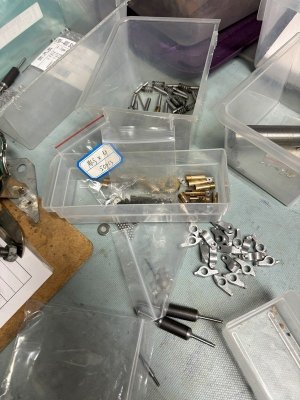
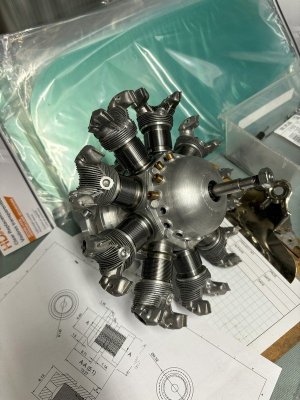
.
The longest "active" project is the radial. Started it 10+ years ago. Didn't know squat about machining, cnc, etc. Been a learning experience. Lots of parts and need to remake a lot of them, but its getting closer. Optimistically - maybe a year or 2?
Next on the list is the B1 Springbok 5" gauge live steam locomotive. Bought as a chassis running on air. I've so far built the tender body 80%, and soldered up the insides of the boiler. Next up is boiler assembly, going to be a big job and waiting on spring weather to have a go.
After that is a Worthington duplex steam pump. I got distracted building the B1 boiler and needed some machining time, and the radial was at a difficult place for me so I started something new. This one is about 90% done. I may actually finish it...its all small but time consuming parts left (tube fittings, check valves and some silver soldering.)
Then its mostly either new things I shouldn't start yet, or tool / workshop fixes / upgrades etc.
In the list of things that I've started the mental exercises but really should not start until the above are done:
Gauge 1 (45mm between the rails) live steam "Green Arrow" locomotive (2-6-2) - fair amount of CAD done on parts I'd CNC
Some design work on making a functional direct injection diesel in small scale (~22cc - 28mm diam piston x 35mm stroke) - because I like a challenge...
I also have castings for a 1/4 scale Wright Whirlwind 9 cylinder for when I'm bored
A 3.5" gauge
Hopefully I'll be sharing some progress and wins along the way.
And pictures, always pictures. After this week at work I have had it reinforced in my head that nobody reads words
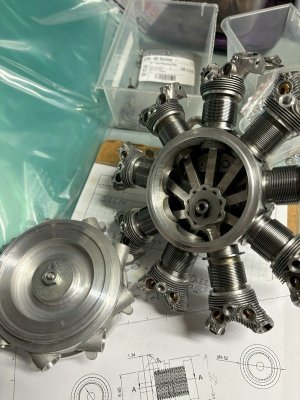
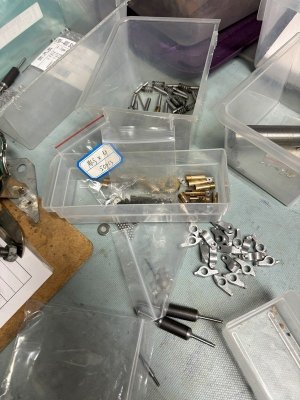
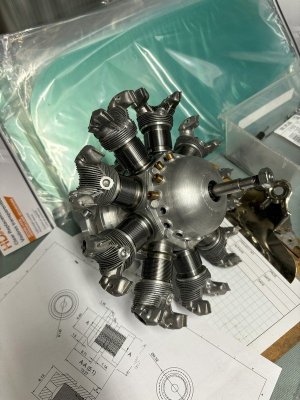
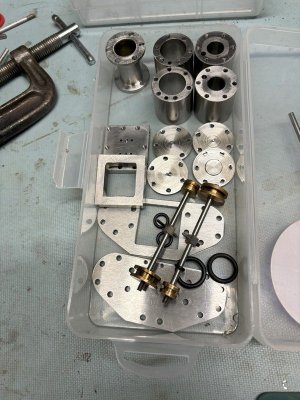
Last edited: