Yes. The Gecko manual says don't put more than 12V on the pin 9 VFD 10V. That's the clue that the power for the PWM circuit comes from the VFD (or motor driver). Recall message #4 above where the MACH screens are set for PWM.Ok but I don't understand where the pwm signal comes from? it was my understanding the power supply was separate? in my "box" that the G540 is located in the power supply for the G540 is inside, the 0 to 48V supply is pin 11 and 12. according to the pinout 7 is vfd grounf 8 is vfd output and 9 is VFD 10V
In this case the spindle step pin would be set to pin 14 and no direction output.
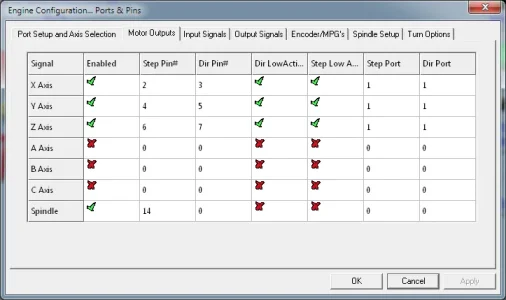
Then under spindle set use Spindle Motor Output and PWM control and 5 kHz

Now MACH will create a PWM signal on pin 14 that is 0 when spindle off and fully at the Pin 7 VFD-10V value at full speed.
I believe you can set the VFD pin to 5V and that would now create 0V to 5V output.
A 50% PWM signal (50% ON at 5V or 10V and 50% OFF at 0V results in half the analog voltage out. So either 2.5V if terminal 9 is 5V and 5.0V if terminal 9 is 10V.
So I believe, but I'd have to check further,
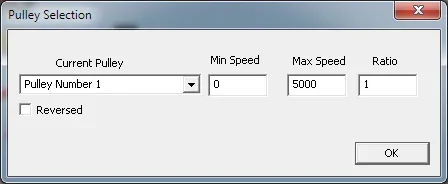
if this is how your spindle speed is configured then if you do an S2500 M3 the PWM rate from MACH will be 50%, the output voltage for the 10V system will be 5V and theoretically a VFD that uses 0-10V for Motor Speed control will recognize the 5V input value as the command to spin at 2500 RPM.
If you are applying 5V to terminal 9 then theoretically you'd see 2.5V which your motor controller will interpret at 50% of the full speed and also 2500 RPM.
Does this make more sense?