Spent the day prepping this backplate that I sourced from @140mower (Thanks Don).....
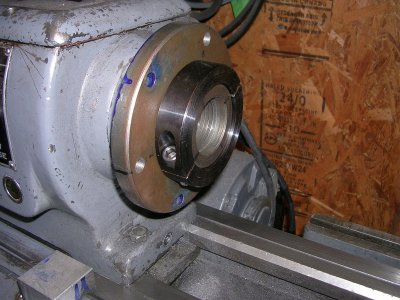
Had to turn the registration down and re locate/drill the mounting holes. Then I turned the spigot/boss down to accommodate a 2.25" clamping collar. Tomorrow I'll source a 1/16" thick slitting saw to slot the spigot/boss with and will see if I can set her up on the mill using a angle plate. I'm left hand challenged right now and I don't think I can mount the RT due to it's weight. We will see.
@dfloen will 1/16" be wide enough? Your images look a lot wider than that.
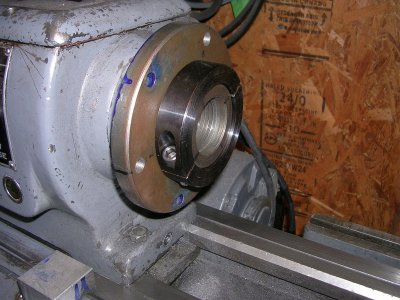
Had to turn the registration down and re locate/drill the mounting holes. Then I turned the spigot/boss down to accommodate a 2.25" clamping collar. Tomorrow I'll source a 1/16" thick slitting saw to slot the spigot/boss with and will see if I can set her up on the mill using a angle plate. I'm left hand challenged right now and I don't think I can mount the RT due to it's weight. We will see.
@dfloen will 1/16" be wide enough? Your images look a lot wider than that.
Last edited: