Xyphota
Ultra Member
After purchasing it, I realized it was the Bridgeport of contentious discussion in this forum haha:
canadianhobbymetalworkers.com
I'm into it for about $5K which included a bunch of accessories and more importantly delivery.
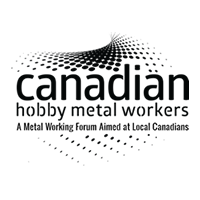
Colchester Student $3500 Calgary
https://www.facebook.com/marketplace/item/2147046365446629/?ref=browse_tab&referral_code=marketplace_top_picks&referral_story_type=top_picks Same seller has a bridgeport for $5000. Both are in the basement of a house.
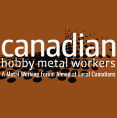
I'm into it for about $5K which included a bunch of accessories and more importantly delivery.