BXA (wedge style) QCTP dimensions:
What really matters... OEM tool post height in relation to chuck axis (I know for a fact that the tool is not in the chuck square - I didn't expect the dimensions to be this close to one another so I felt I was w/in a tolerable amount of precision when I did the setup).
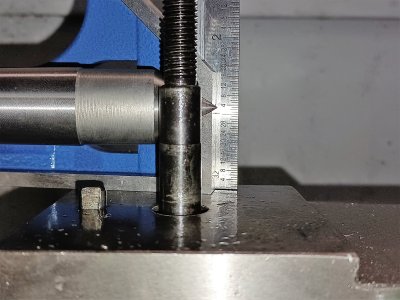
Taking into consideration the tooling heights from my previous post - IF I maintain this height, my 5/8" tooling will be right at/very close to lathe c/l (<---- that's the term you guys use, right?) - the 3/8" tooling should be ~ 1/10" BELOW lather c/l. That's not a tonne but in my non-educated mind, I'm "under" which I think is the important part.
Here's photos of the tool slide for familiarization (Ali* website has ones very similar that are "AT320 76mm Center Height Metal Lathe Tool Rest" for $150).
Note that the dovetail is very imprecise and relies on (please name that chunk of metal for me, gib?) and screws to tighten it up.
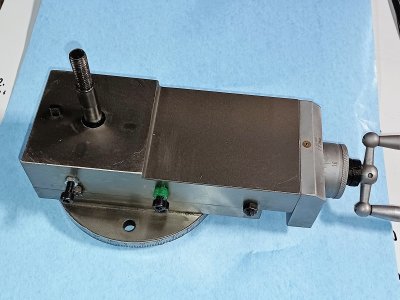
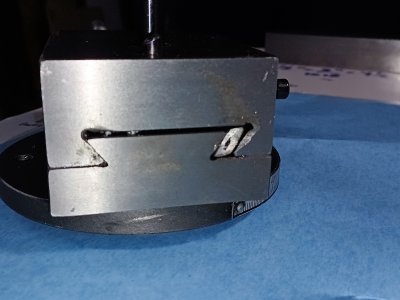
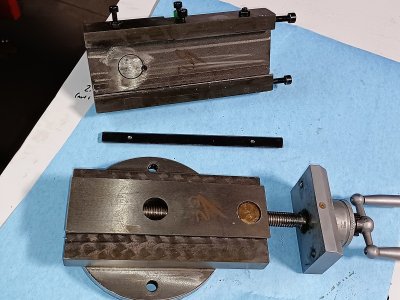
The 1018 block that I bought previously to machine a new tool slide from beside the stripped tool slide.
The 60° dovetail is slightly off the OEM angle that was (scrapped?) into the tool slide - I have the t-slot tool that's just slightly undersize of what the slot would need to be (a second pass I guess).
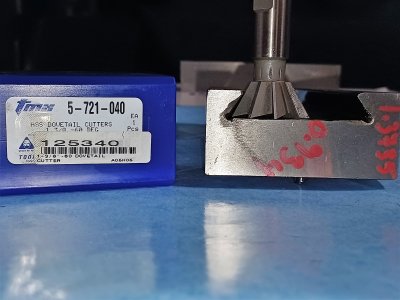
This is the tooling that I have for the milling machine (CX611) so that you can guys have an understanding of capabilities (not mine of course

)
I took all of the information I'm currently presenting and duplicated the OEM tool slide in SolidWorks (not shown, less some details) before "adjusting" it as a hypothetical part.
I AM GOING TO PRINT THIS PART on the 3D printer overnight as a cheap prototype (<$5). As a hypothetical part, it gave me something to create the blueprint from so I could share dimensions in an easy to follow manner.
The dimensions... all of the information... culminates here... remember, the 5/8" tooling on the BXA tool holders had a height of 1.09375", the 3/8" tools were at about 15/16"...
Thanks for sticking w/ me this far - I haven't decided whether or not to make this part yet - I'm soliciting for your thoughts on the dimensions (is there enough material in this hypothetical part?) and what kind of impact on my lathe capabilities would it create if I decided to make this part (like negatively).
Right now, my lathe work goals mostly revolve around being able to create bushings for different applications involved w/ the stock car stuff... bushings for the spherical bearings, pucks/bushings for welding fixtures, weldable inserts for round tubing, etc. In the future I would like to create external and internal threads, bore, create internal grooves for snap rings, etc.
Everyone's help is appreciated - the effort I placed in this is a reflection of the respect I have for it.