I'm considering purchasing a new lathe before I retire in June and this one is on my short list. I think someone on the forum must own on these machines, the Modern Tools version and the PM one are very similar. I'd like to hear your impressions if you have one. This machine is also sold by Jet as model GH1440W. I don't really have a good reason to buy a new lathe other than this will be my last opportunity to buy NEW.
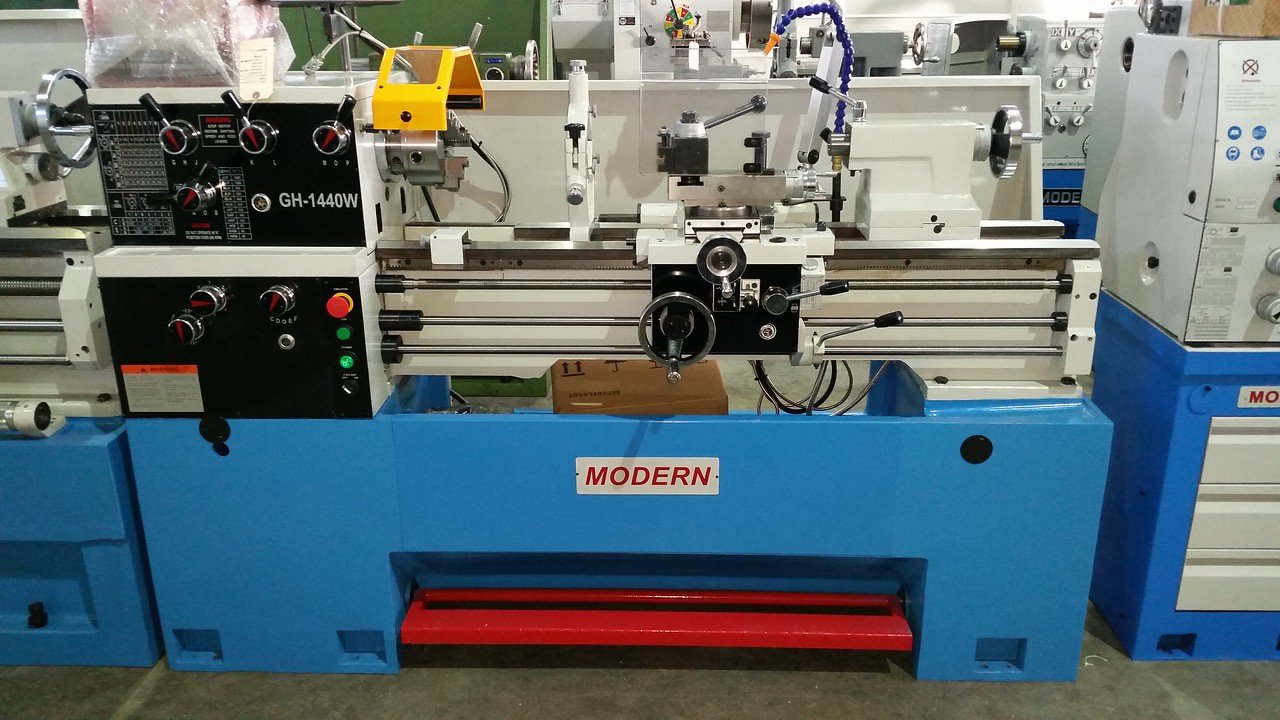
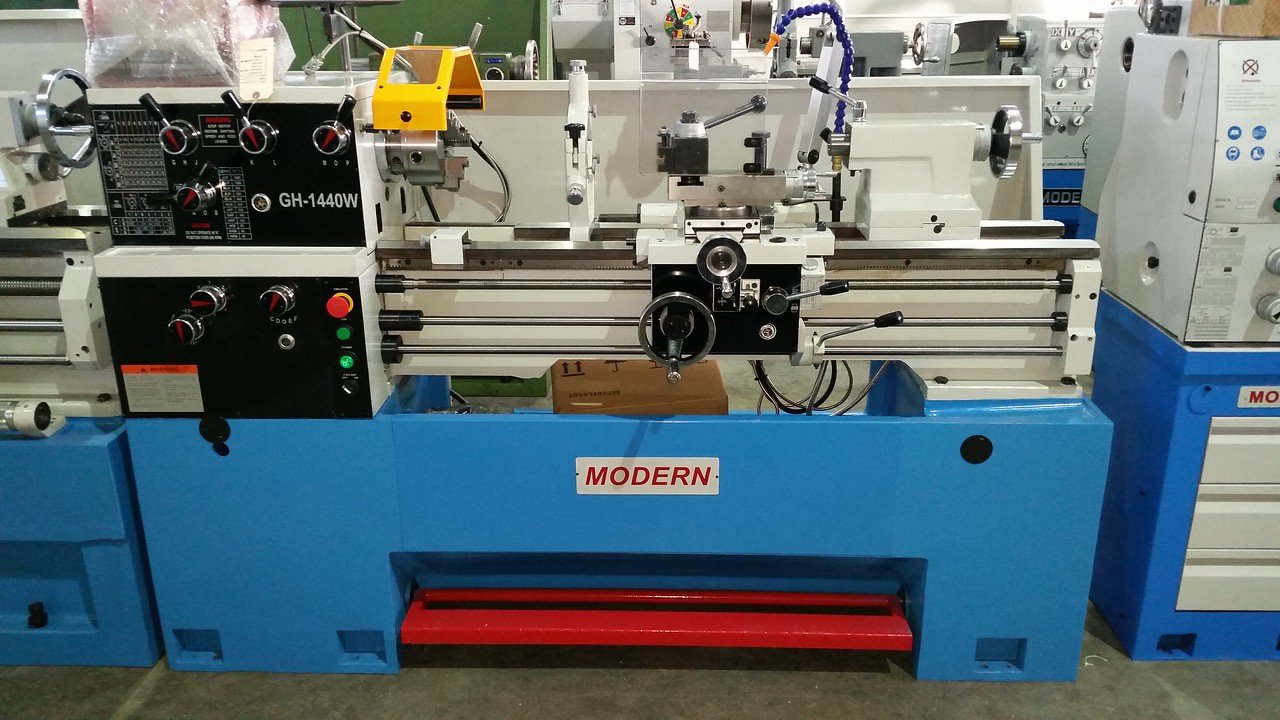
Last edited: