slow-poke
Ultra Member
Just for fun I made a list of the Pi4 LinuxCNC system costs that I play with on my bench. Really need to mount it all on a board and wire it up permanently. Anyway, also attached is the list of prices. There are some additional costs for cables that I didn't include. Often these can be sourced cheaply or even free.
View attachment 38375
BTW, not trying to convince anyone. Just information about this sort of system. For this touch screen I should probably install one of the touch screen user interfaces instead of the standard AXIS one.
John,
Thanks for posting the shopping list, very useful information. If I ever decide to "come over to the other side" I should be able to continue using the existing touchscreen monitor. I rigged up a small programmable keypad for common commands and easier numeric entry, unlikely I could get that working on a PI. Also not sue if I could get Linux running on the SBC that is currently running Win-16?
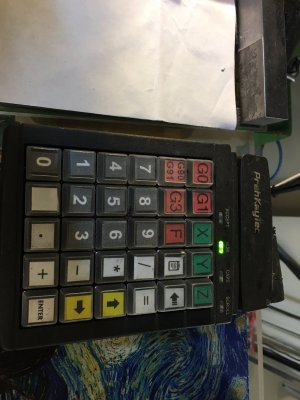
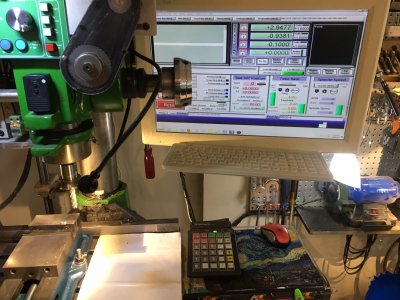