SparWeb
Active Member
I bought a CNC router!
It's old!
No it's not that bad, but it's a DIY project that the guy has picked at for almost 20 years. Still works, and tonight I have cut wood by jogging the cutter, just trying it out. Learning as I go.
The CNC software is installed on a geriatric Windows XP computer. Eventually the nostalgia will wear off, and I will want to upgrade to a newer machine and Mach4. For now it works so I'll be happy for a long time using it as-is.
I'm new to Mach3 and CNC in general, but in a previous life I worked with engineers programming and operating CNC machining centers. When I sent them a drawing I liked being involved with getting it right and asked a lot of questions. Let's see if I remember any of what they told me.
Are there any other Mach3 users out there, or has everyone moved over to Mach4?
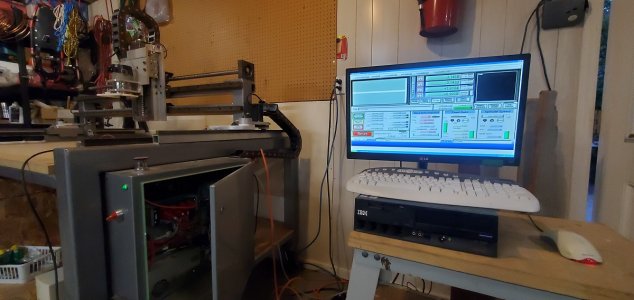
It's old!
No it's not that bad, but it's a DIY project that the guy has picked at for almost 20 years. Still works, and tonight I have cut wood by jogging the cutter, just trying it out. Learning as I go.
The CNC software is installed on a geriatric Windows XP computer. Eventually the nostalgia will wear off, and I will want to upgrade to a newer machine and Mach4. For now it works so I'll be happy for a long time using it as-is.
I'm new to Mach3 and CNC in general, but in a previous life I worked with engineers programming and operating CNC machining centers. When I sent them a drawing I liked being involved with getting it right and asked a lot of questions. Let's see if I remember any of what they told me.
Are there any other Mach3 users out there, or has everyone moved over to Mach4?
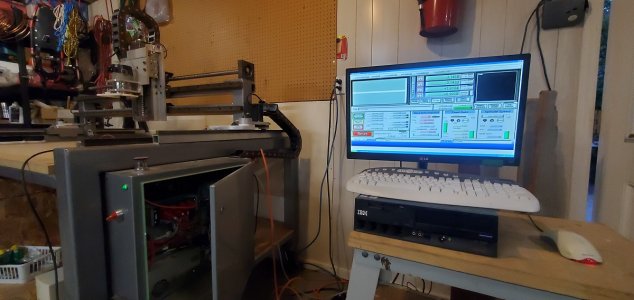