Like most of you , I have a list of things to do and stuff to build , the list never really gets smaller . This list has enough on it to keep me busy , when I get spare time.
I just started another engine rebuild on a 44 year old Shovelhead 1200 , that's going well , I did a couple of re-bores on the Van Norman , they were already + .010" oversize , it is going to +.020" over bore and finished on the Sunnen hone.
Lot's of wear on several items , the rods were not straight and were out of round , The beauty of old Harley engines is , if you have Sunnen hone you can hone the rods to make them straight again and use oversize rollers to hand "fit" the big end , this set straightened out nice at .0005" over the size they were. You can get several sizes of oversize rollers starting at +.0002" , in .0002" increments all the way up to +.001" and then the sizes go to steps of +.002" & +.003" . The crank pins come in a few sizes too if you need to hone the rod races out larger to straighten them or make them round again . You can also press in new races and go back to standard if that's what you want to do , the possibilities are huge ! . The small end bushings were bad too , rebuilding rods involves pressing in new bushings and honing them to fit the wrist pins . Back in the past this used to be common , guys having engines rebuilt like this , labour was not super expensive like it is now , parts were reasonable too , then labour rates climbed up & up . People then turned to crate engines and rebuilds became not so much an every day thing. Now parts are very expensive , lots of stuff is double what it was 5 - 10 years ago. The skills to do this kind of work are not easily found today , think about it , who even does a valve job anymore ?
The crank is supported on the left side in two Timken bearings which also control end play . The rh main bearing is a caged double roller arrangement .
The outer race , if it gets out of round or develops a taper can be lapped back into a serviceable dimension and oversize rollers fit . You can also change that shaft or bearing race .
This is the lapping tool , it pilots off the left main , it's cranked by hand and is adjusted to size by two nuts that draw the lap head on to a taper and expand it.
One item on the list is to restore this valve spring tester , I may reach out to Rimac to get a new lens and bezel .
I need to take it completely apart and de-rust a few things , paint it and get a calibration spring .
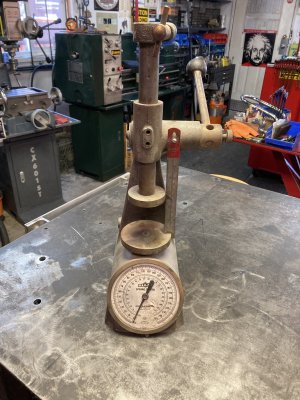