I'm using mostly white PVA "tacky glue". A small bit of hot glue also, but not much on this one. Both very recommended in the foam casting communities, and are supposed to burn out very similar to the foam with no issues. The wax should as well, as long as it's a lower melting temp wax. My fillets were a mix of parrafin and toilet ring gasket, so I doubt that was an issue. Judging by the fillets and surface finishes I'm guessing they burned out fine.
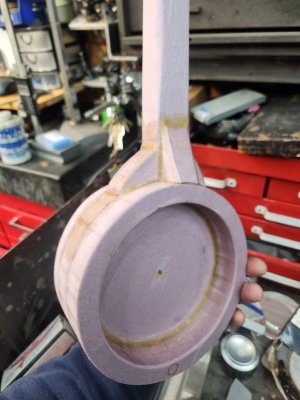
Those photos show the pattern a bit better. Those cold shuts are perpendicular to any glue seams that are there. The more I thought about it this afternoon, the more I think it happened when the basin filled up and stalled, there was probably some metal that already dropped down and filled the lower portion, then when the basin dropped it pilled in on top of it causing those cold shuts. Perhaps the straight vertical Sprue might be a contributing cause that prevented venting, as it choked off? Their placement would support that theory. I went back to vertical on this one to cure the overhang fill I had with the last one, but if I do another I'll tilt it again like everyone recommends. If I get some miss fill on the sand I can always machine it out.
As much as I just want this grinder done at this point, I want to figure this foam casting out too, so I'm going to give it at least another shot. Using this project to give lost foam a try was the whole reason I went with a casting in the first place. I think if I tilt it like the first time it'll actually fill and vent properly, and now that I have enough sand to cover it completely it "should" cast just fine. The first casting didn't have any fill problems, just that blowout from lack of sand coverage at the top.
I also don't think I'll go bigger on the sprue. Kelly Coffield, who has arguably the best results and most dialed in process to acheive them on the web for foam casting does some much bigger castings with similar, and even smaller sprues, so I don't think that was the issues. I honestly think it was the vertical routing that choked it off temporarily. Tilting it on the side would allow the molten aluminum to follow the bottom and fill the cavity melting the foam, and the gases to escape above it on the way back out. In theory anyway....
Just thought of a better way to vent it while typing the above....will have to wait till sometime this week, but I think it'll work just fine. I'll make the pattern very similar, but just tilt the sprue off at a tangent point on an angle so it will fill on an angle running down to the bottom, allowing a bottom up fill, while venting out the top more easily. Won't have any over hang problems packing the sand if I leave it in this orientation. Kinda mad I didn't think of that before....learning opportunity I guess....I've always had to do things the hard way....
Could maybe also make a vertical vent, but drill it out so that it's open from the beginning, not needing a burn out.....Drill out most of the sprue too might help as well. Shirley wouldn't hurt......I just picked up this big 5/8" twist drill and need to find
some use for it....I have a 3/8" one that long too.
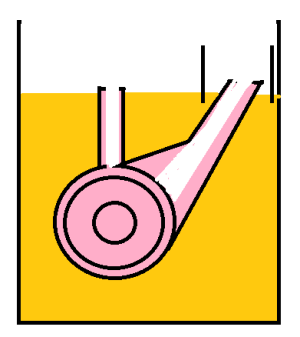
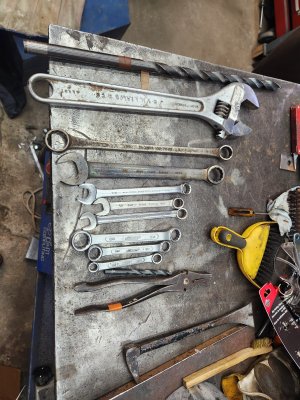