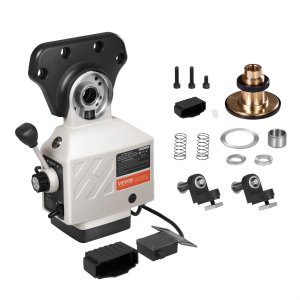
VEVOR Power Feed X-Axis 150Lbs Torque,Power Feed Milling Machine 0-200PRM, Power Table Feed Mill 110V,for Bridgeport and Similar Knee Type Milling Machines | VEVOR CA
VEVOR Power Feed Milling Machine offers high efficiency, precision, low noise, and long-lasting durability with easy operation and wide compatibility for various mills.