Also for you Toronto guys there is auction in Cleveland Ohio that has power flaker and bunch of surface plates and Camelback and few other things that a machinist would be interested in.
www.bidspotter.com

36" BROWN AND SHARPE 242-6 CAMELBACK STRAIGHT EDGE
Lot 93 at Zagar, Inc. from CIA Industrial, LLC.
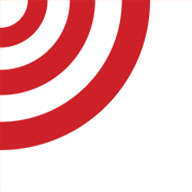