Still practicing with milling machine (trial and error) I made myself a spindle square out of salvaged material. I loosely used Dale Derrys video series, "Metal tips and tricks" as an inspiration.
The aluminum was cut from an 8" round log of extruded aluminum (soft, gooey stuff), the brass screws
were made from salvaged water valve stem, and the shank was rod salvaged from an old printer.
I did some "jeweling" on the back side with a small chunk of scotch Brite pad glued to a piece of wood doweling. If I would have changed out the scotch Brite pad several times I would have had a better more defined job.
It was a first attempt with a ball end mill and I'm not happy with the finish it gave but I think at least part of that is the material I was working with.
I have two different mounting distances for the indicators as I have only a 4" vise on my mill but wanted to get maximum distance for table squaring so I made 3.5" and 5" spaces.
The aluminum was cut from an 8" round log of extruded aluminum (soft, gooey stuff), the brass screws
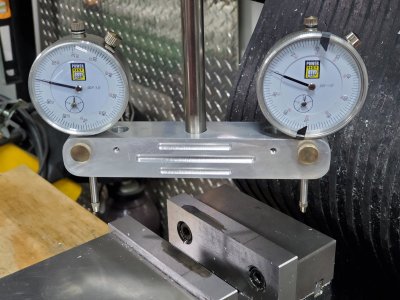
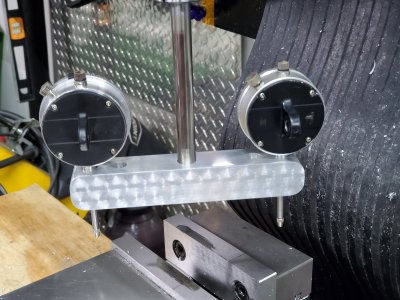
I did some "jeweling" on the back side with a small chunk of scotch Brite pad glued to a piece of wood doweling. If I would have changed out the scotch Brite pad several times I would have had a better more defined job.
It was a first attempt with a ball end mill and I'm not happy with the finish it gave but I think at least part of that is the material I was working with.
I have two different mounting distances for the indicators as I have only a 4" vise on my mill but wanted to get maximum distance for table squaring so I made 3.5" and 5" spaces.