You know how one project is often interrupted by another project? Hand cranking the X axis is getting old (albeit, my mill is small, but I am lazy) so a power feed for it has jumped up the list. I started with trying a drill to see how well it worked. Great, so then making an adapter, which turned out well. I then used a small torque wrench to determine what ball park will be and 15 in lbs turned it. I don't trust the torque wrench to be deadly accurate but it gives me a starting point. I wanted to know if my stock NEMA 23 motor might work and it is on the border so all good so far. As most know, NEMA designation is the mounting size so to swap it out with a higher torque 23 should not be an issue.
I did want to confirm the torque values though so cleaned up the adapter shaft and will do a more accurate test today with weights before I cut the shaft off to make the actual adapter.
It has been a while since I did anything with microcontrollers, very little with step motors and I am new to the Arduino platform so I wanted to do some practice/experimenting. I made up this prototype module. I am thinking I might have a digital display to show set feed speed but practicality says a simple control will suffice. Time and my "gotta get it done" syndrome with a mild case of "the novelty has now worn off" syndrome will determine how elaborate it gets. The nice thing about ucontrollers is that you can add or change features relatively easily.
I did want to confirm the torque values though so cleaned up the adapter shaft and will do a more accurate test today with weights before I cut the shaft off to make the actual adapter.
It has been a while since I did anything with microcontrollers, very little with step motors and I am new to the Arduino platform so I wanted to do some practice/experimenting. I made up this prototype module. I am thinking I might have a digital display to show set feed speed but practicality says a simple control will suffice. Time and my "gotta get it done" syndrome with a mild case of "the novelty has now worn off" syndrome will determine how elaborate it gets. The nice thing about ucontrollers is that you can add or change features relatively easily.


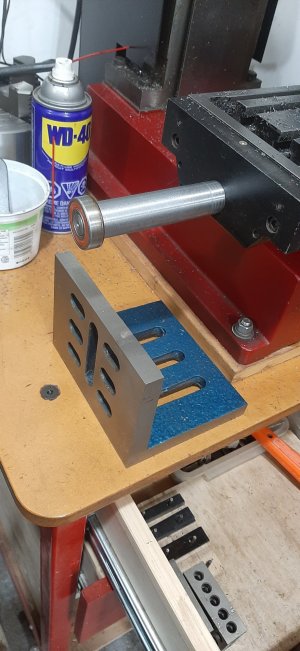
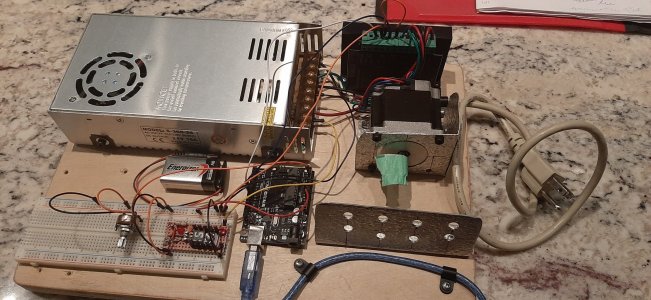