Hmmm..... I wonder how you can add a survey to this thread? @Janger can you shed some light?
In any event I vote keep the Hartford, ditch the Bridgeport.
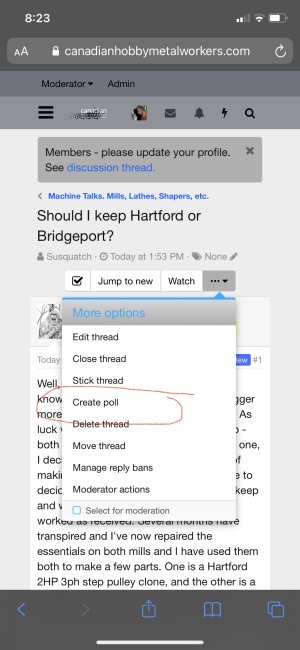
Visual answer Craig. -john
Hmmm..... I wonder how you can add a survey to this thread? @Janger can you shed some light?
In any event I vote keep the Hartford, ditch the Bridgeport.
Lads:
For some clarity: torque being the force and horsepower being the rate at which that force is done. The difference is torque is doing the work, while horsepower is how fast that work is being done.
Depending on the load being applied an electric motor only needs to develop enough Hp to overcome the applied load(resistive force) or counter torque. So if no load is applied to the electric motor only the Hp to keep it rotating will be developed and very little torque. A 2 Hp motor can develop up to 2 Hp at the rated RPM but may run at rated RPM at much lower Hp.
Right on. Torque is force, rpm is speed distance. A totally linear relationship.
Yup, torque has to go up to equal same hp at lower rpm. Linear math.
!
Perhaps you think HP is more important than torque and I feel they are both important
yup, thats all it is. P=T x Angular Velocity (speed). Of course power is the ability to do work, we don't want power going down as we slow the machine. i.e. if we want 1hp on our lathe at 2000 rpm, no ones going to be happy with 0.05 HP at 100 rpm. Same with a mill. If you are driving some big 4" fly cutter at 100 rpm, or a slab mill cutting in a horizontal or a large diameter piece in the lathe, its going to stall if you only have 1/20th the HP at normal motor speed @ 60 Hz. You want torque to go up as speed reduces to maintain the same power. A mechanical transmission does that, a VFD does not.
It may not be noticeable if you're going from say 1800 rpm to 1500, few of us drive machines much of the time if ever at capacity. However if the VFD is means of speed control, drop the speed to 90 and you won't have enough power left to make a cut. That's were my poor anecdote of trying stop it with your hand comes in, I shouldn't encourage doing so, but with just a pulley on a motor on a bench you can stop it that way at 1/20 of its 60Hz rpm - there is barely enough power to turn itself over. Ignoring losses, that 2hp is now acting like 1/10 HP motor. Reduce speed via mechanical means and your torque is now 20x what it was at 1800 (again ignoring losses)....exactly what you need to power a big diameter cutter or large diameter piece of work in the lathe.
What mostly would solve this electronic transmission issue would be using a servo motor - it feedbacks RPM and the controller increases current as needed to maintain RPM. The little consew motors are a great example. three magnets and a hall sensor. 3/4 HP (claimed), dial it down to 200 rpm and you cannot stop that motor by hand. I don't know of options in larger sizes as all the servoes I've seen are expensive and the feedback is intended for precision motion applications, not just simple feed back of rpm
It knows the motor rpm and it adjusts current flow to increase torque as required to maintain the rpm up to the limits of the VFD & motor.
@Susquatch : since you have a VFD rated motor on your Hartford you will be fine with any speed you choose to operate at. You will get more consistent torque at lower speeds and be fine running at higher speeds.
For NON VFD rated motors - just a standard type motor, it is designed for rated Hp at the RPM stated on the name plate and the duty cycle limitations. Using a VFD to control a standard motor above it’s rated speed and subjecting it to full load can cause issues with excessive heat. This can also occur at lower RPM’s than rated and trying to use all the available HP. Most of us will not use devices in this manner so a VFD on a Standard motor will be fine.
As a work around some folks will increase the Hp of the standard motor so it can perform more adequately for the application.
As you stated in your above comments, the VFD rated motor will behave along the lines of a servo type motor by delivering more consistent torque/Hp over a wide range of speeds.
The tone of your reply is GREAT. I always worry when I have discussions like this that I am upsetting the other party. .
The main thing I am getting from your points is that perhaps you don't realize that a modern VFD actually does have feedback just like a servo motor does. A VFD contains a microcontroller with all kinds of smarts in it. It uses its own knowledge of the timing and magnitude of the current flowing in the three circuits to know exactly where the motor is and how much load it is seeing. As the motor load goes up, the motor tries to slow down, but the VFD throws more current at it which causes more torque, to maintain the RPM.
If I am running THE SAME CUTTER at half speed, I am automatically and inherently doing half the work too.
Again, I think that the difference in our perspective in this case is that I would say you need more torque to keep the tip going, and you have said that you want more power.
The point that @Brent H made so much better than I did is that this doesn't matter either as long as the AVAILABLE TORQUE is enough to handle the load. Bigger cutters put more torque on the spindle exactly the same as a longer wrench on a nut does. So the motor needs to be able to apply that same higher torque from the other end.
Implicit in your point, assuming I understand it now, is that you don't believe that there is ENOUGH AVAILABLE TORQUE to drive the cutter when the cutter is bigger and the shaft has to turn slower to maintain the cutting tip speed.
It knows the motor rpm and it adjusts current flow to increase torque as required to maintain the rpm up to the limits of the VFD & motor.
My VFD Is a TECO L510. I really like it.
Actually, I believe, a VFD does not know the RPM of an induction (asynchronous) motor. It only knows the rpm of the rotating magnetic field in the stator windings it is sending to the motor. It “assumes” the rotor is keeping up with that rotation.
The only way a controller knows the rpm of a rotor is if you have a sensor on the rotating element and feed it back to the controller.
It is called sensorless vector control mode. Not all VFD's have sensorless vector control. The better ones do.
+1 from meonly use the VFD for fine tuning the speeds
I would say its not doing that except very close to its natural speed (@ 60Hz)
since you have a VFD rated motor on your Hartford you will be fine with any speed you choose to operate at. You will get more consistent torque at lower speeds and be fine running at higher speeds.
On a machine tool, work is essentially the removal rate - i.e. cubic inches per minute.
as many an old drag racer will tell you, horsepower sells cars, torque wins races.
that’s not quite true but I understand the point you’re makingas many an old drag racer will tell you, horsepower sells cars, torque wins races.
that’s not quite true but I understand the point you’re making
light car with a high revving small mill can dominate in bracket racing versus big blocks in heavy cars
it’s all in the setup to get across that line
I still maintain that torque does NOT drop off as rpm goes down. .
How far are you from Chatham?Speaking as a guy who raced bracket, and who later was involved in the design of engines for passenger cars and trucks.....
You are right.
But as you probably well know, bracket is a special case. There is a lot more to it than just big blocks in heavy cars VS small cars with high rev engines.
All that aside, @whydontu's point is still fundamentally right. The whole world loves HP and that's why the marketing folks push it. Everyone loves to talk about it, but very few really understand it.
Since you brought it up though, I would add that one of the holy grails in engine design is the best of both ie a high torque, light rotating mass, high reving engine in the lightest weight body and frame possible. What you really want is instant response high torque. That's totally different than machining which is mostly a steady state process. In any acceleration race what you really want is a rotating system (crank rods pistons, Cams, chains, flywheel, driveshaft axle wheels and tires) that weigh nothing and therefore have no inertia and can go from 600rpm to 6000 instantly!
...... and then you need to have some magic way of maintaining traction.
Anyway, that field is huge and I'm sure an entire library of books could be written on it.
More importantly, it doesn't change the fundamental importance of torque or my choice of mills.
Wanna grab a case of beer, join me beside my mill, and swap war stories? Actually, you can all just show up - I have lots of beer for everyone and I feel like sharing!