Dan Dubeau
Ultra Member
I'm still not done, but thought I'd throw up some pics of a blown ribbon burner forge I'm currently building.
Started a few weeks ago, and just tonight finished welding up the forge body. Things move slow around here sometimes.....
Started off with an old purged 20lb propane tank. Welded on the some angle scraps for feet, then started laying out my doors. and burner hole.
Plasma made quick work of it.
Then is was time to make the ribbon burner. It started life as a 3x3"x6.5" square tube. I made a diffuser plate, and capped the ends. Also welded in a 2" pipe stub.
Then is was time to make a mold box, and steal some of the kids crayons. Not shown is the bottom plate where I drilled a pattern of 5/16" holes to hold the crayons for the refractory pour.
Then it was time to let everything acclimatize in the shop for a few weeks before getting back to it again today.....I didn't take many pictures today as I was going, I just wanted to get it done, but here's where I'm at with it. It's all ready to be lined with 2 layers of 1" 2600* rigidised ceramic blanket, and a 1/4-3/8" kast-o-lite 30, with a poured floor. I have some itc-100 for a top coat too.
I still have to make a cart to hold the blower, etc, but hopefully it won't be 3 weeks until I get back to it again. I'll try and get on that, and lining it this week. Hopefully.
Started a few weeks ago, and just tonight finished welding up the forge body. Things move slow around here sometimes.....
Started off with an old purged 20lb propane tank. Welded on the some angle scraps for feet, then started laying out my doors. and burner hole.
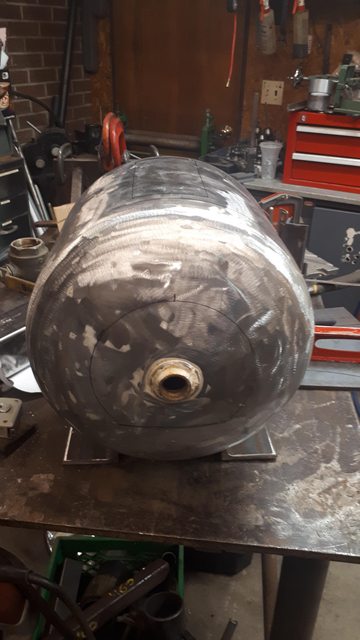
Plasma made quick work of it.
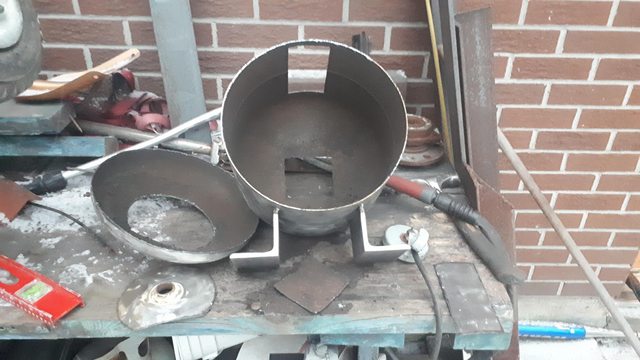
Then is was time to make the ribbon burner. It started life as a 3x3"x6.5" square tube. I made a diffuser plate, and capped the ends. Also welded in a 2" pipe stub.
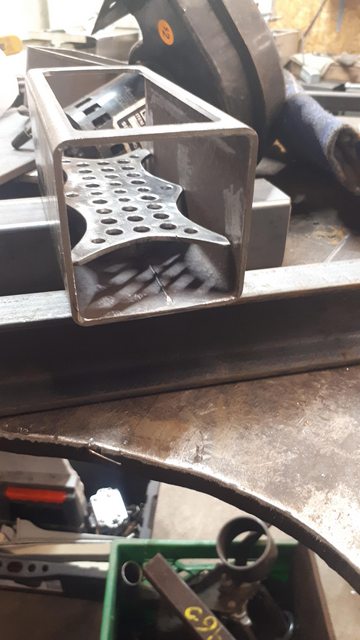
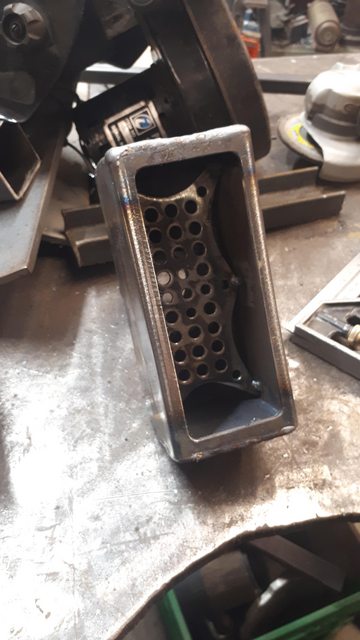
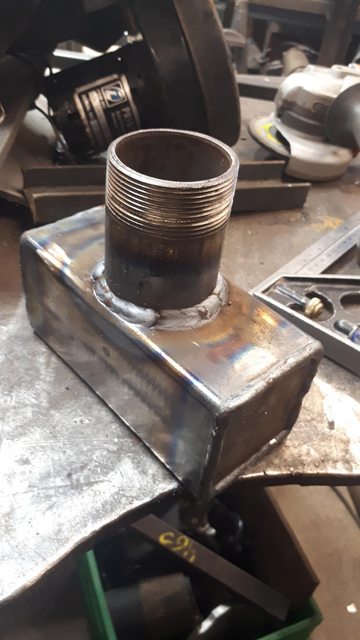
Then is was time to make a mold box, and steal some of the kids crayons. Not shown is the bottom plate where I drilled a pattern of 5/16" holes to hold the crayons for the refractory pour.

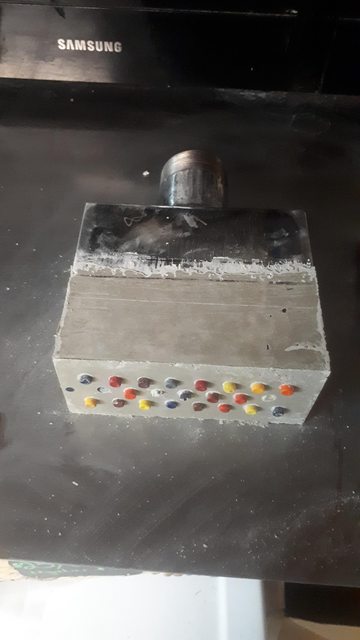
Then it was time to let everything acclimatize in the shop for a few weeks before getting back to it again today.....I didn't take many pictures today as I was going, I just wanted to get it done, but here's where I'm at with it. It's all ready to be lined with 2 layers of 1" 2600* rigidised ceramic blanket, and a 1/4-3/8" kast-o-lite 30, with a poured floor. I have some itc-100 for a top coat too.
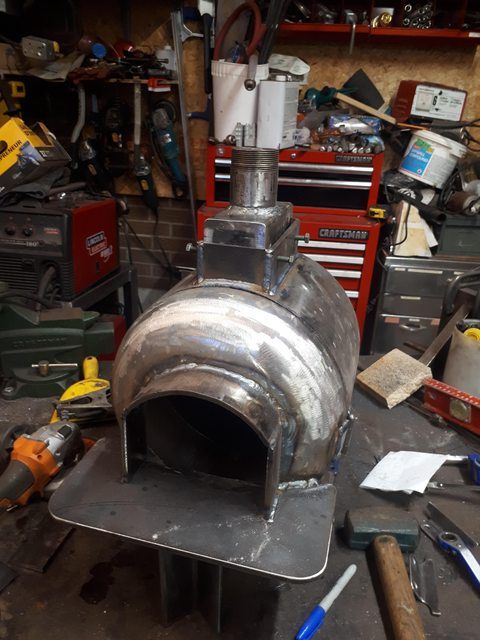
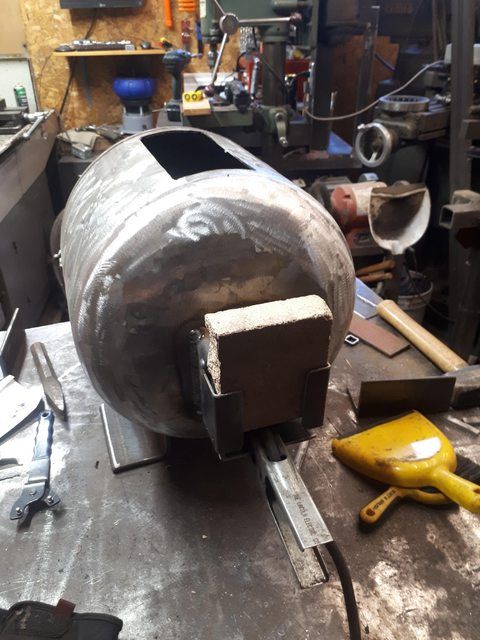
I still have to make a cart to hold the blower, etc, but hopefully it won't be 3 weeks until I get back to it again. I'll try and get on that, and lining it this week. Hopefully.