Still gathering parts n' supplies to get this mill running . I have a Huanyang 2.2 kw VFD , some cable , terminal strips , an E stop button , a junction box , a 24 volt digital tachometer and more .
I have gutted all of the old stuff out of the machine , the contactors , switches etc .
I kinda have a plan , gathering my info online because I am well outside of my comfort zone on projects like this , the end goal is to have it look professional , not like Homer Simpson was working on it .
I'm working on it when I have time , still working out a few details and not real sure about how I'm going to wire it . I want to use forward & reverse switches and an E stop button , like it was configured originally on the original panel , but wired to the VFD . I will need to figure out how to wire the FWD / REV switches , I am going to order new switches , the original switches are kind junky , I am not sure which switches I'm going to need just yet .
I also have a 24 volt digital Tachometer that I'd like to use , I still need to figure out how I'm going to mount the magnetic pickup , also , I am wondering if I can get my 24v from the terminal strip right on the VFD ?
Here's some of the old parts removed , the transformer , contactors , switches etc ........
I have other things going on as well ....... the framers were here yesterday and the garage repairs have begun .......... YAY !
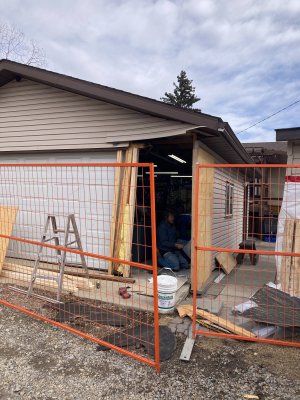