I started tearing apart the mill to do the motor swap to 1.5 hp 3ph.
I don't have a puller so I had to improvise with some all-thread couplers and 3/8" bolts which I used to jack to pulley off the shaft.
As I got close to getting it off the shaft I ran out of thread on the fully threaded bolts so I ran them back in and put the shouldered bolts in the other end.
The pulley was so tight I thought I was going to strip the threads. Even after heating it up with my propane torch it was a struggle to make it budge.
Finally got it off. Discovered what there was no keyway in the pulley, just a setscrew that seated in the keyway.
I think I'll be shopping for a new pulley as the bore is 15/16" and the new motor shaft is 7/8. I suppose I could bore it out and make a bushing but I have no means to broach the keyway.
I don't have a puller so I had to improvise with some all-thread couplers and 3/8" bolts which I used to jack to pulley off the shaft.
As I got close to getting it off the shaft I ran out of thread on the fully threaded bolts so I ran them back in and put the shouldered bolts in the other end.
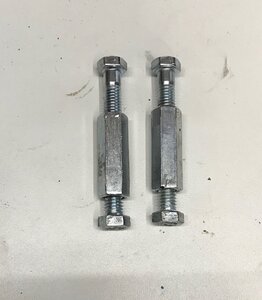
The pulley was so tight I thought I was going to strip the threads. Even after heating it up with my propane torch it was a struggle to make it budge.
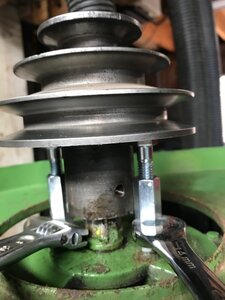
Finally got it off. Discovered what there was no keyway in the pulley, just a setscrew that seated in the keyway.
I think I'll be shopping for a new pulley as the bore is 15/16" and the new motor shaft is 7/8. I suppose I could bore it out and make a bushing but I have no means to broach the keyway.