slow-poke
Ultra Member
I often hear comments to the effect "I don't want CNC because I want to be able to use my machine manually.
So do I often. One does not preclude the other.
Images of manual controls for my lathe.
There are two rotary switches and a MPG.
- The MPG emulates the hand wheels, it's graduated in 100 "ticks"
- The first rotary switch, lets you select either: nothing, the X axis, the Z axis, or the compound axis
- The second rotary switch lets you select either: 0, 0.0001", 0.001", or 0.01" per tick
-Action video showing carriage moves with MPG (Z-axis) https://www.dropbox.com/scl/fi/vkkw...ey=k5ghuzzkk6mujk25axft44q8e&st=m2ldco40&dl=0
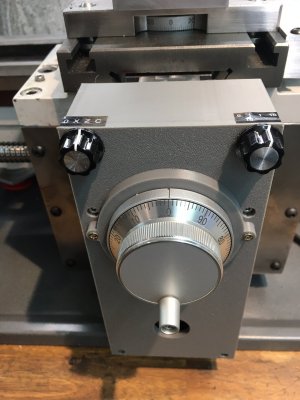
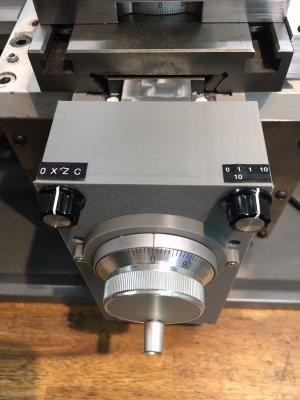
So do I often. One does not preclude the other.
Images of manual controls for my lathe.
There are two rotary switches and a MPG.
- The MPG emulates the hand wheels, it's graduated in 100 "ticks"
- The first rotary switch, lets you select either: nothing, the X axis, the Z axis, or the compound axis
- The second rotary switch lets you select either: 0, 0.0001", 0.001", or 0.01" per tick
-Action video showing carriage moves with MPG (Z-axis) https://www.dropbox.com/scl/fi/vkkw...ey=k5ghuzzkk6mujk25axft44q8e&st=m2ldco40&dl=0
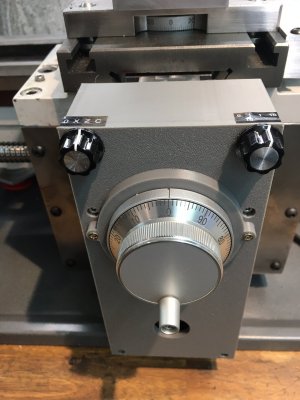
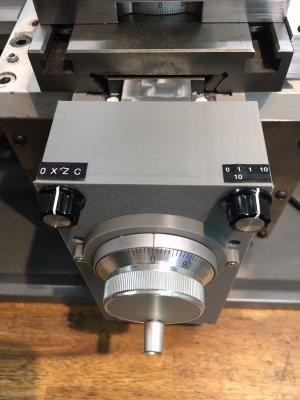