These two links are in the Library plans threads.
I've updated the info on the Atlas Micrometer stop as "tomstechniques" website seems to be gone.
I combined the two stops and made mine for V ways and has the threaded spindle stop.
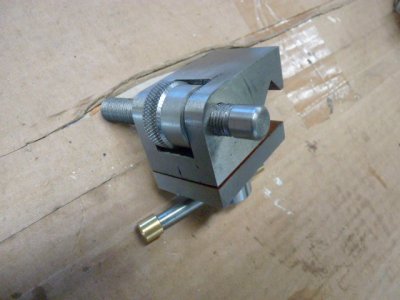
Here are two plans, I combined the two to fit the V ways and have the dial adjustment.
thecogwheel.net
tomstechniques.com

Carriage Stop
This is another project that has been on the to do list for quite awhile now. I’ve been needing a slitting saw lathe carriage stop every since I bought my first lathe and have managed to put…
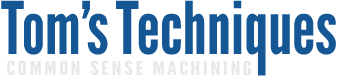
Micrometer Carriage Stop

- YotaBota
- Replies: 8
- Forum: Project Plans
I've updated the info on the Atlas Micrometer stop as "tomstechniques" website seems to be gone.
I combined the two stops and made mine for V ways and has the threaded spindle stop.
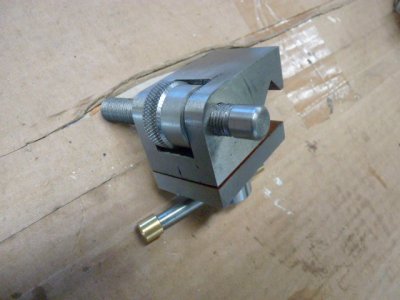