Redneck_Sophistication
Super User
My old McDougall lathe has an old school thread on chucks. With a floating threaded collar to hold it to the tapered spindle with a key.
The chuck has a lot of run out, and the jaws are worn, not straight.
I’d like to fit a new chuck on, luckily the millwright I bought the machine from had a similar plan and had a plate with the same thread/taper made.
So how can I attach a new chuck accurately and in a way that’s adjustable to be able to true it up?
I think the millwright’s original idea was to use a cam lock base. Is this the only adjustable way? It would also add to the length aswell.
I wouldn’t need it for changing chucks as i have a 4jaw and face plate of a matching thread on type.
Thanks, Dave
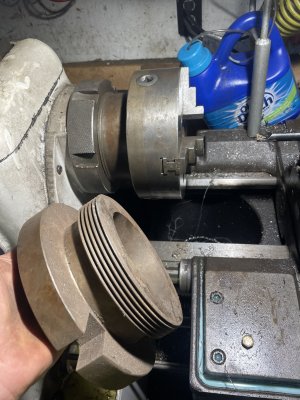
The chuck has a lot of run out, and the jaws are worn, not straight.
I’d like to fit a new chuck on, luckily the millwright I bought the machine from had a similar plan and had a plate with the same thread/taper made.
So how can I attach a new chuck accurately and in a way that’s adjustable to be able to true it up?
I think the millwright’s original idea was to use a cam lock base. Is this the only adjustable way? It would also add to the length aswell.
I wouldn’t need it for changing chucks as i have a 4jaw and face plate of a matching thread on type.
Thanks, Dave
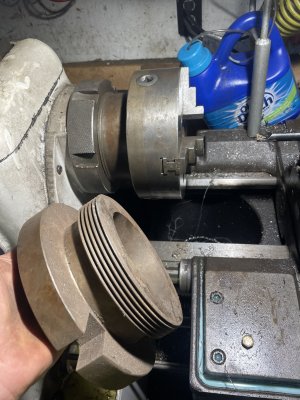