To carry on with the repairs, I found that 1 of the 4 bolts that holds the head to the ram was broken off. They are 1/2" by 7" with square heads so I had to order them from the bolt supply place. I used my Vertex super spacer and a 7/8" rod in a collet to move the head away from the ram. I put a small piece of plywood on the table in the center hole of the super spacer chuck and put the 7/8" rod in the chuck with the rod projecting all the way to the bottom and resting on the plywood on the table and tightened the chuck. I put a 7/8" collet in the spindle and raised the knee so the rod entered the collet and tightened it up. With the spindle all the way to the top of its travel and the spindle clamp tight I loosened the 3 remaining bolts holding the head to the spindle and raised the knee slightly to release the pressure on the bolts. Then I used the Y axis to move the table outward and bring the head away from the ram. The table has a 800lb weight capacity and the super spacer and the head weigh about 500 combined so I wasn't too worried about damaging anything.. I slid in the new bolts and cleaned and lubed the worm gear that allow tilting the head side to side and the reversed the process. Once I was started the head was away from the ram for about 15 minutes.
OK I was a little nervous as you can see I slid some wood blocking under the head but it really didn't do anything as the set up was very solid without it.
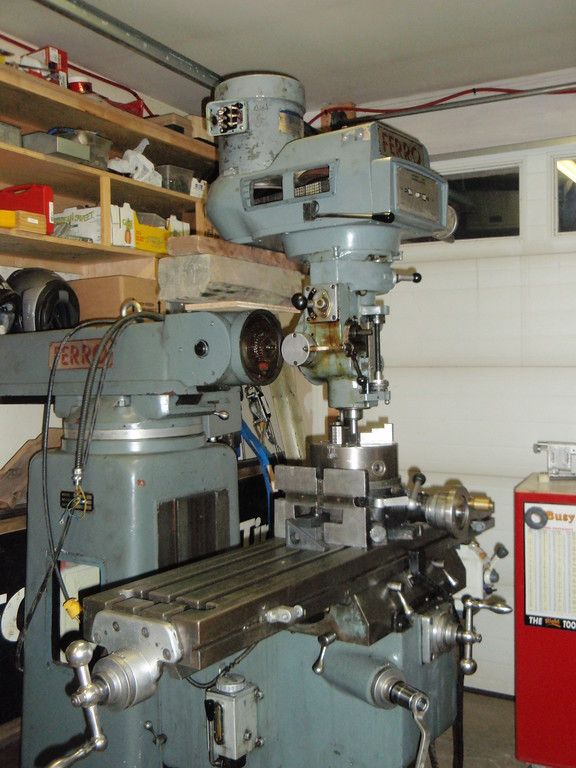
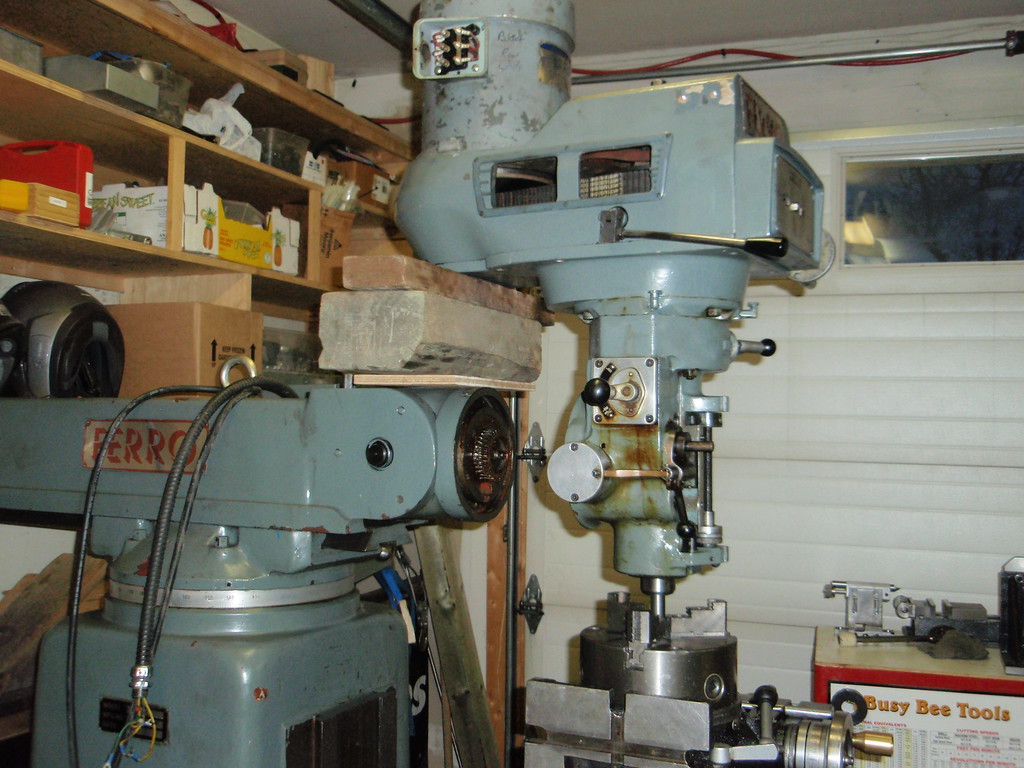
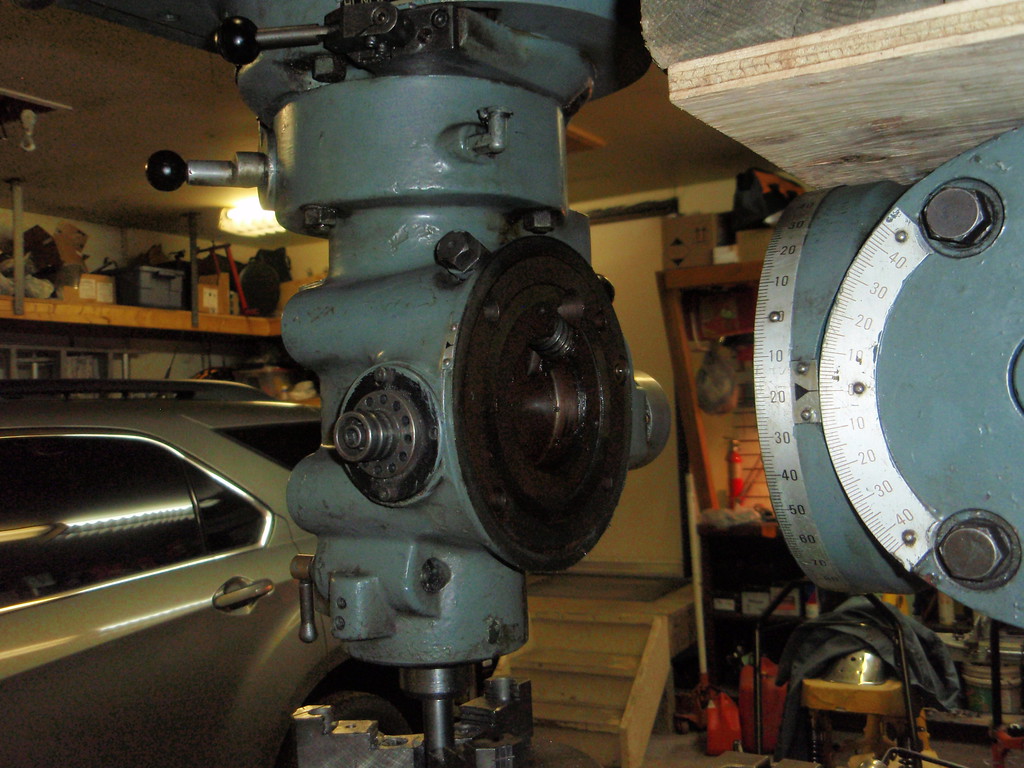
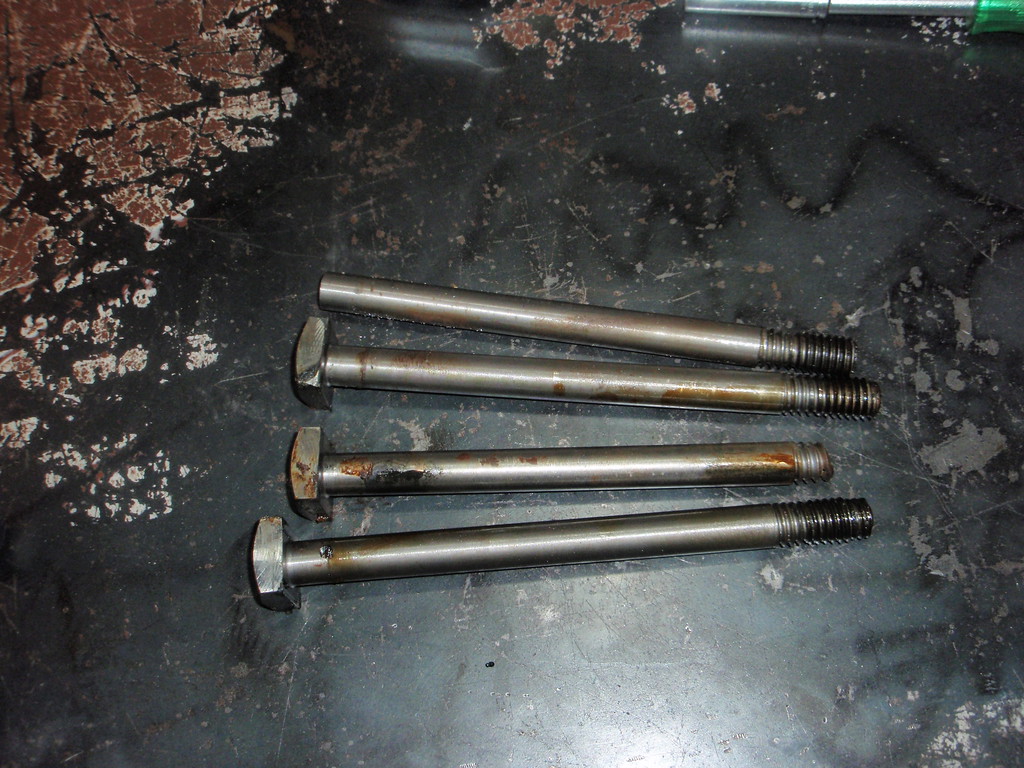
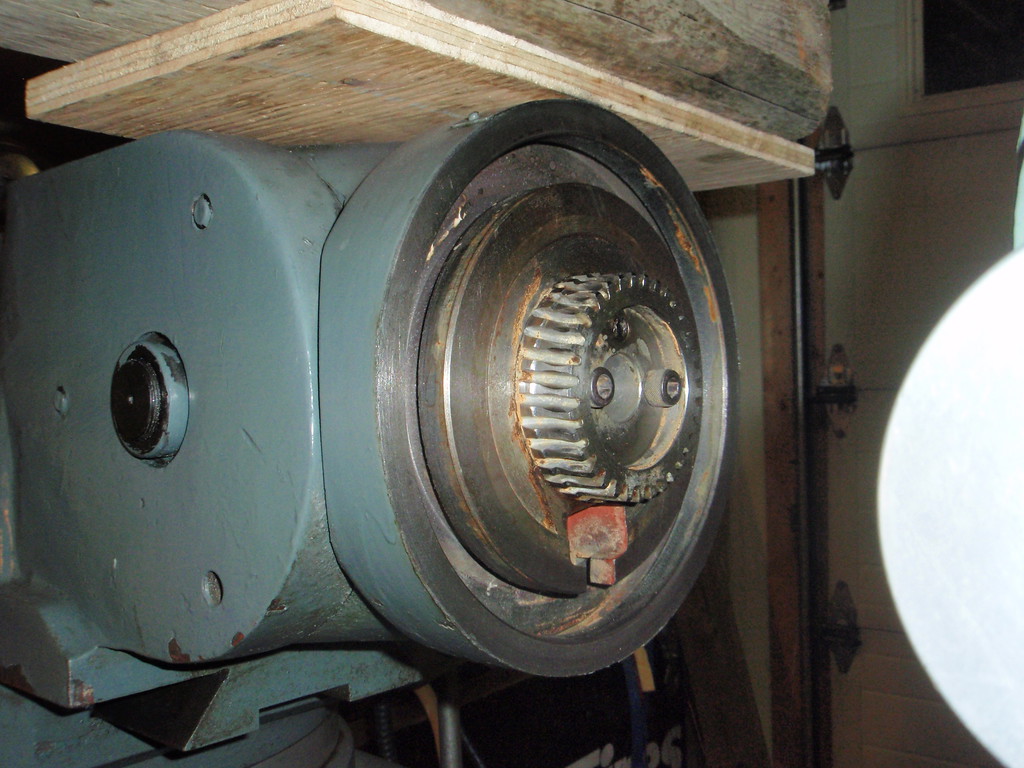
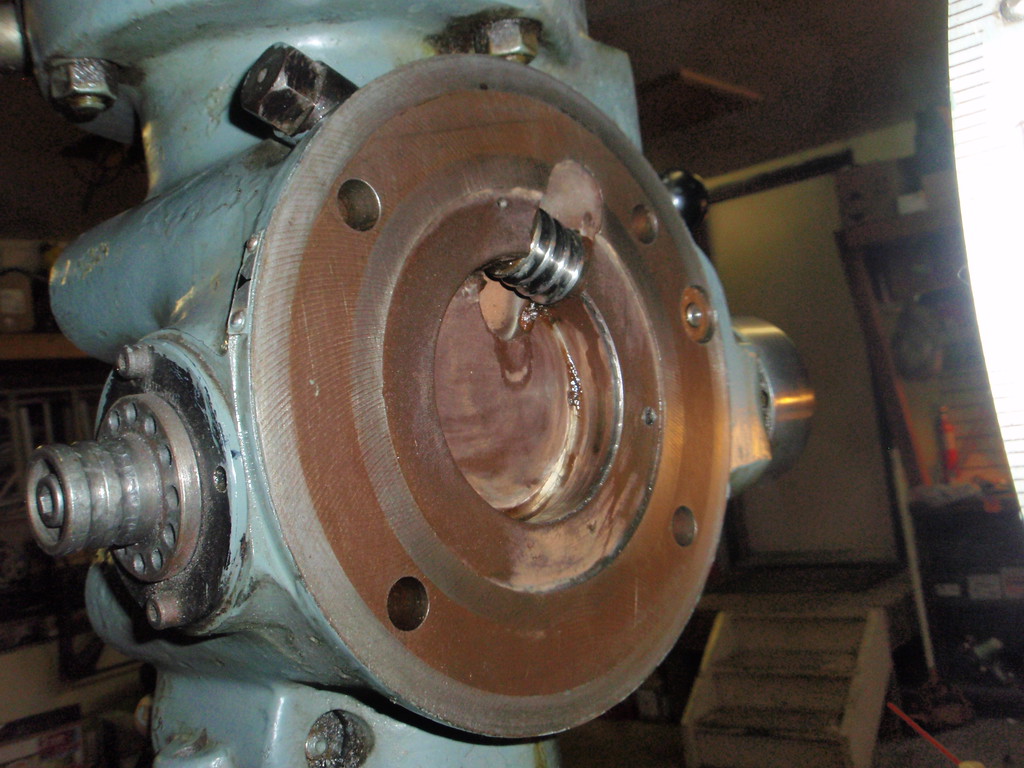
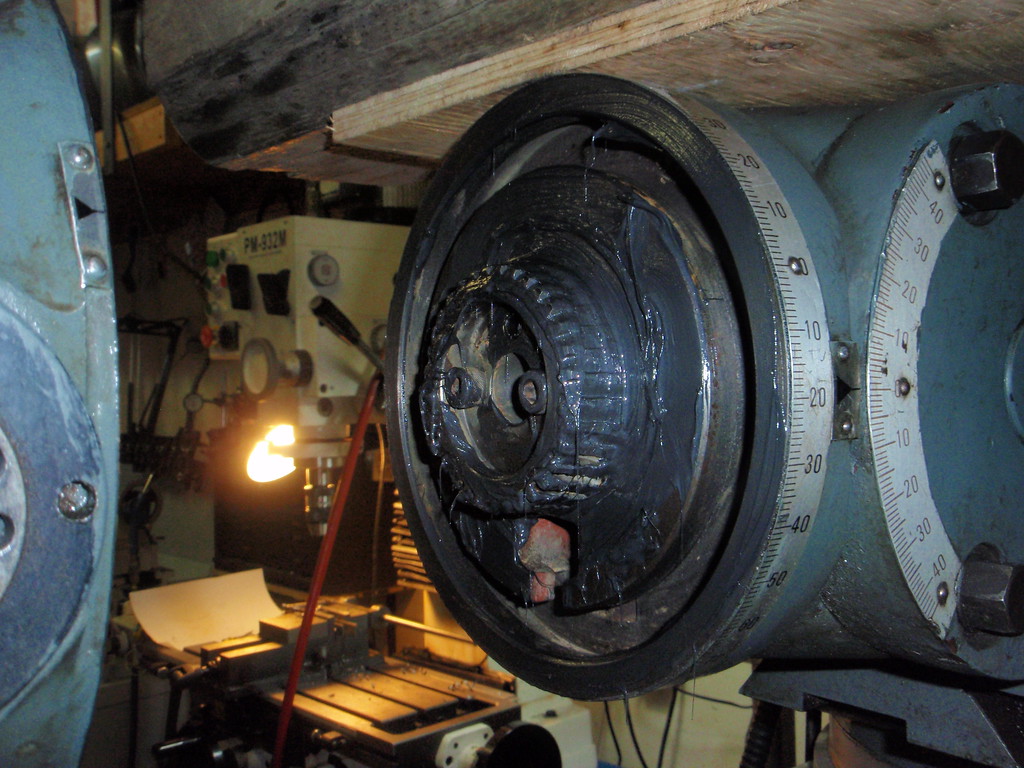
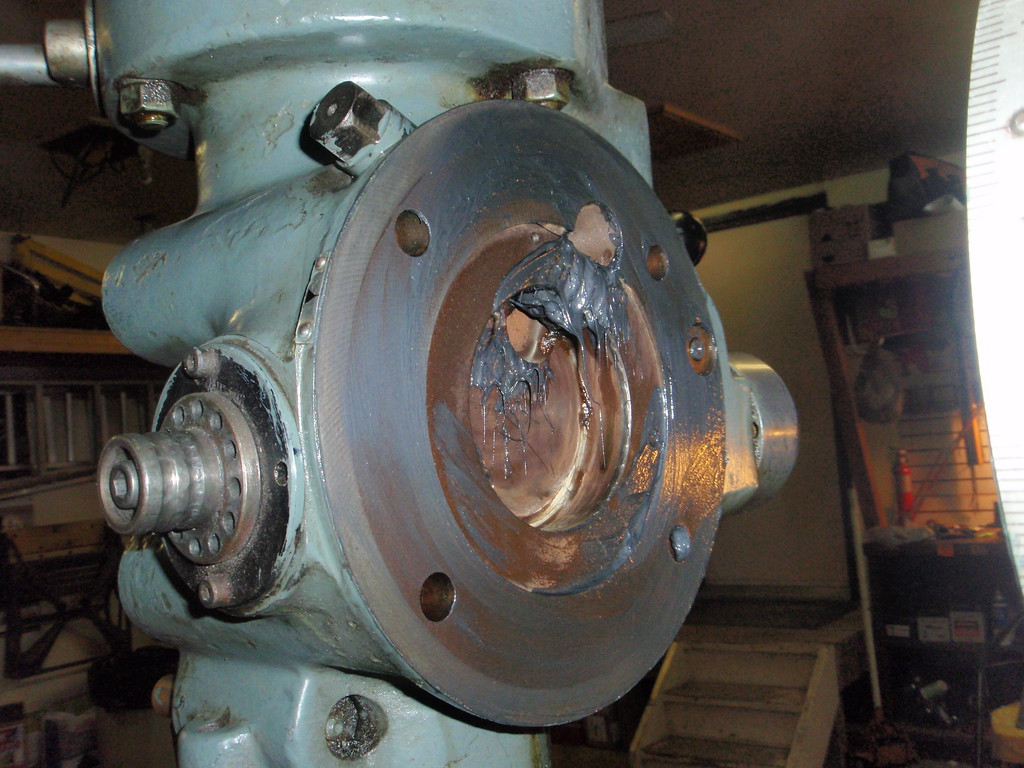
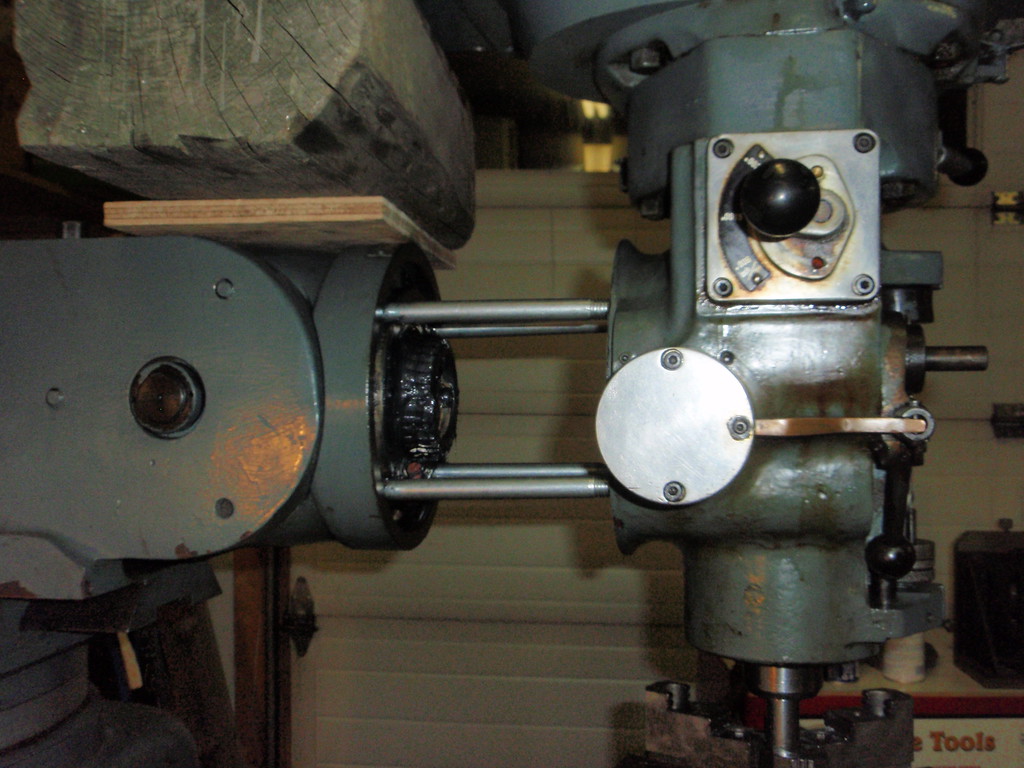
I used some hardened washers from big block Chevy head bolts opened up to 1/2" from 7/16" and long nuts to engage all the thread on the 7" bolts. I smeared lots of moly grease on the worm gears.
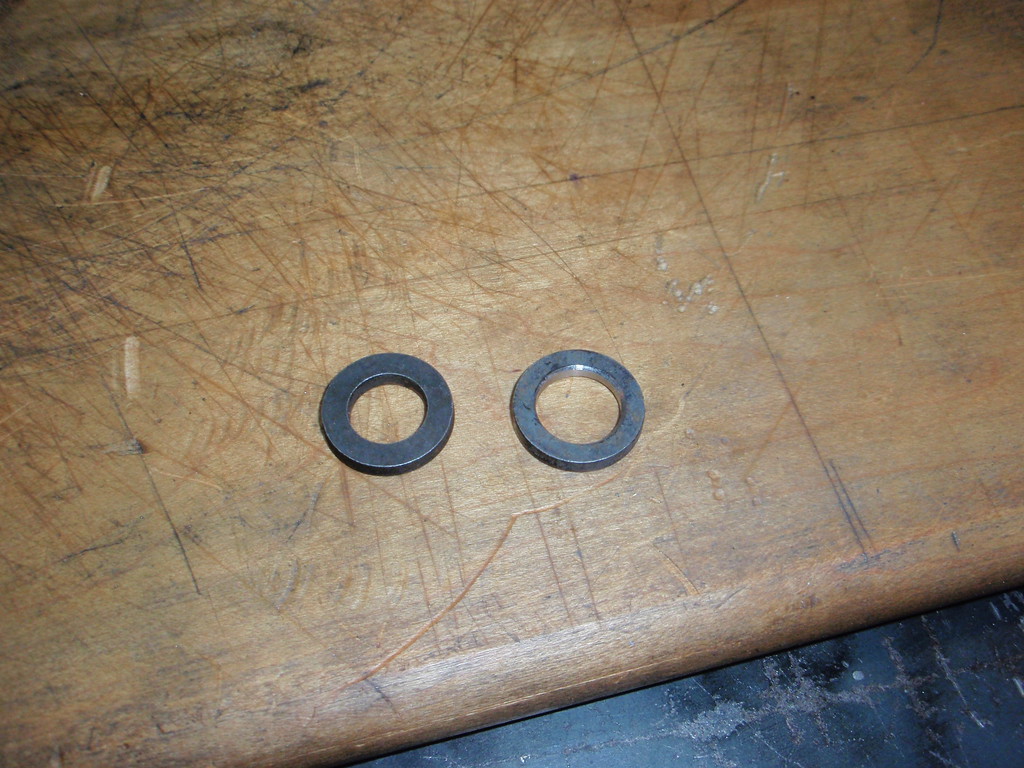
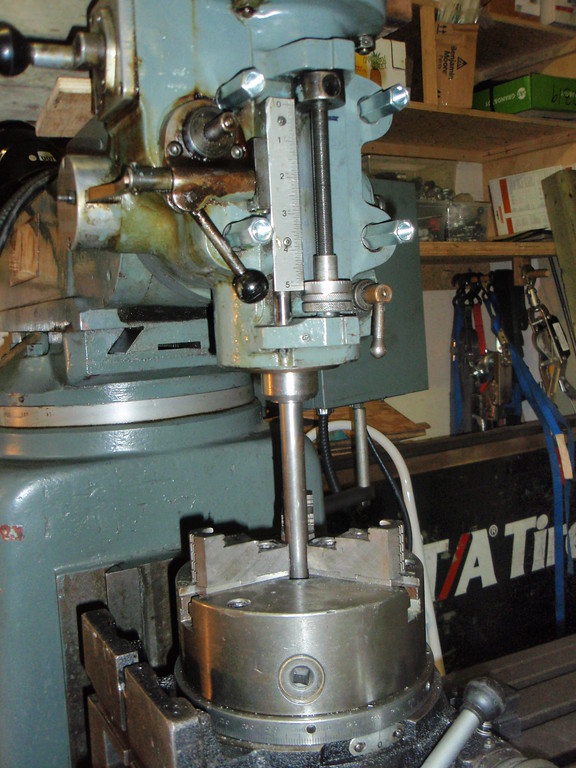
Then I loosened the chuck on the super spacer and lowered the knee, all done!
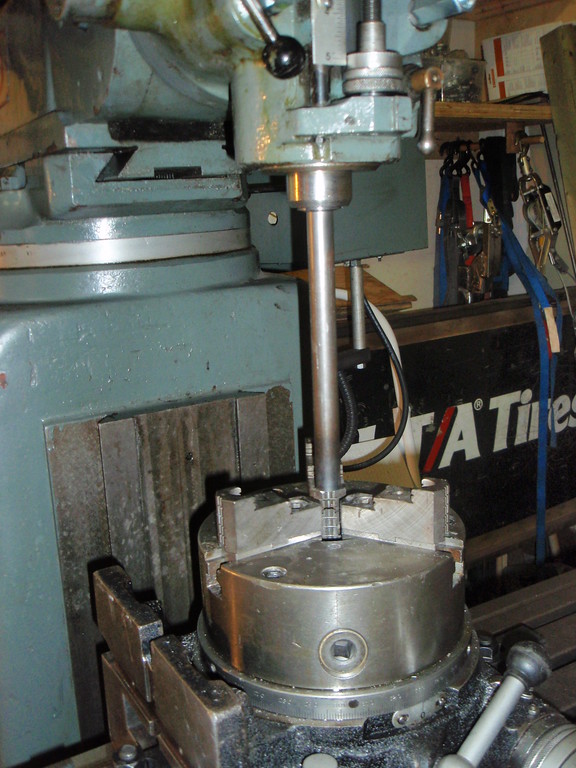
OK I was a little nervous as you can see I slid some wood blocking under the head but it really didn't do anything as the set up was very solid without it.
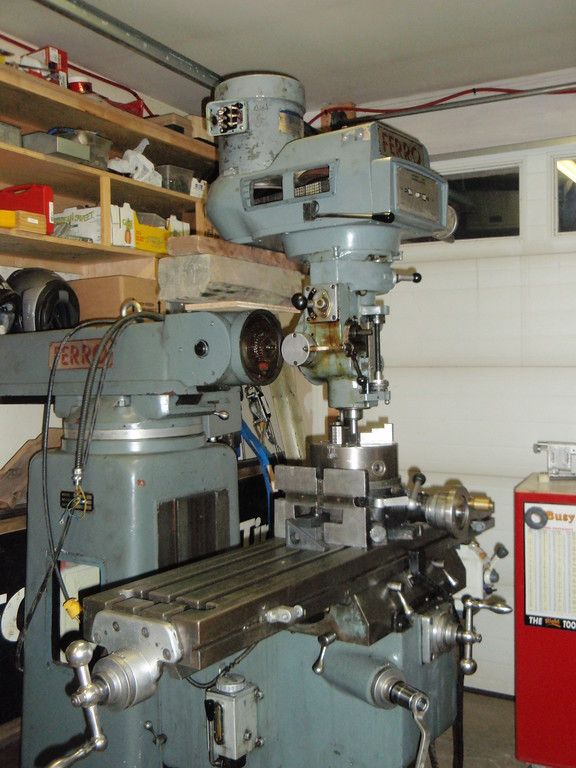
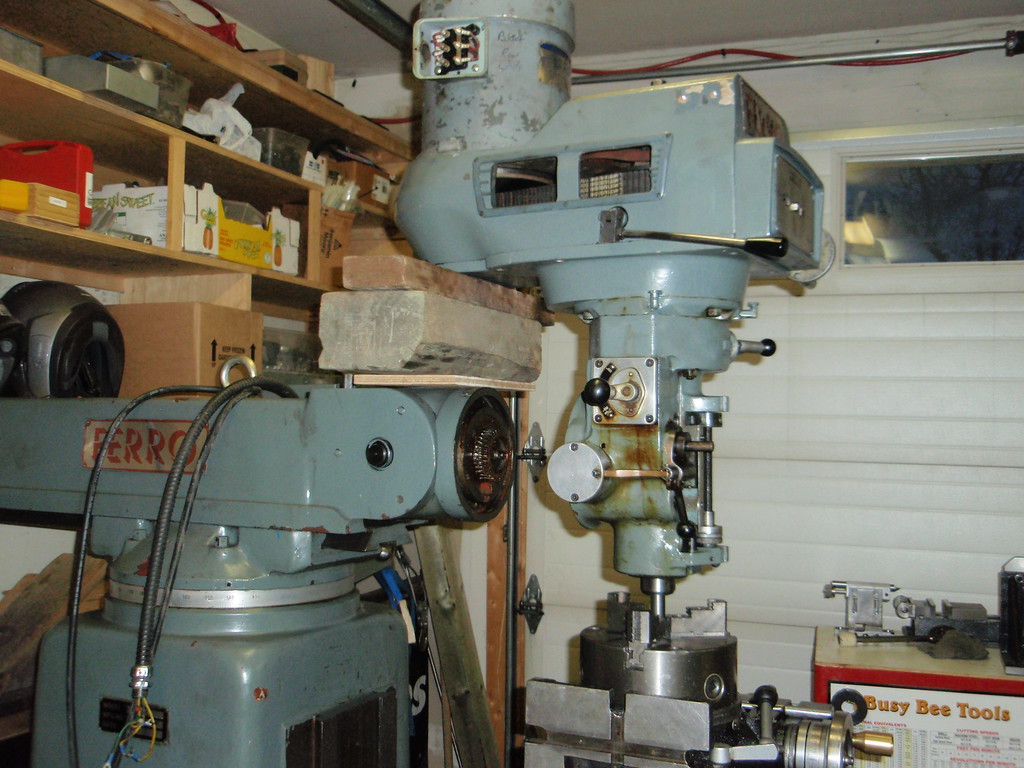
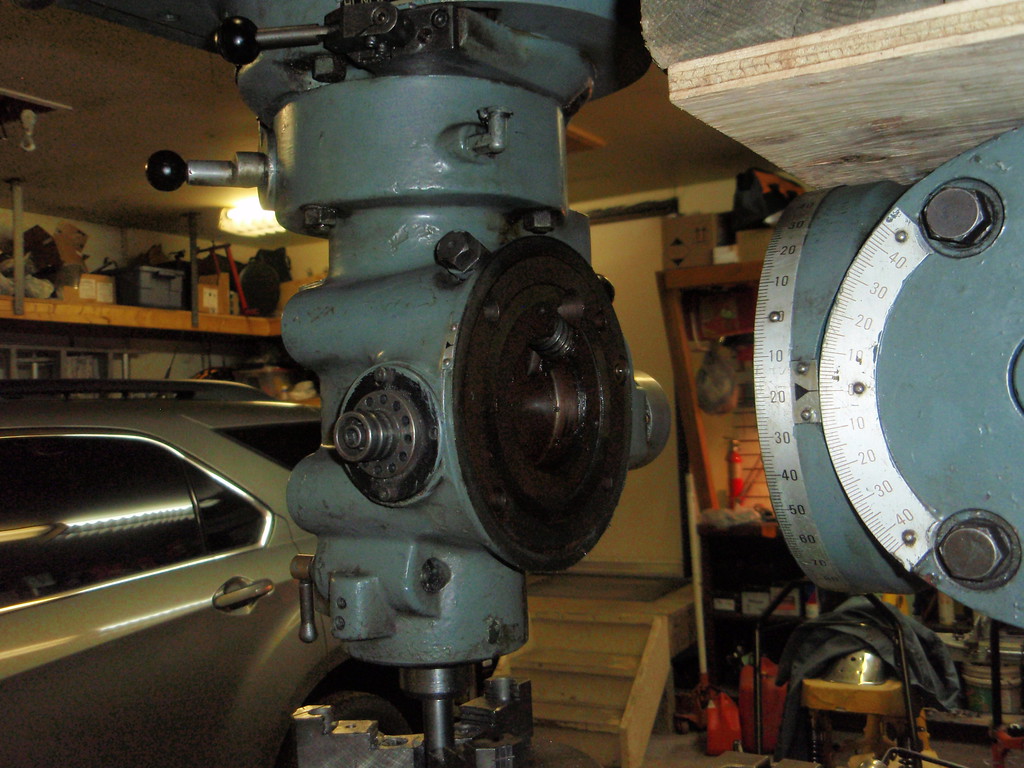
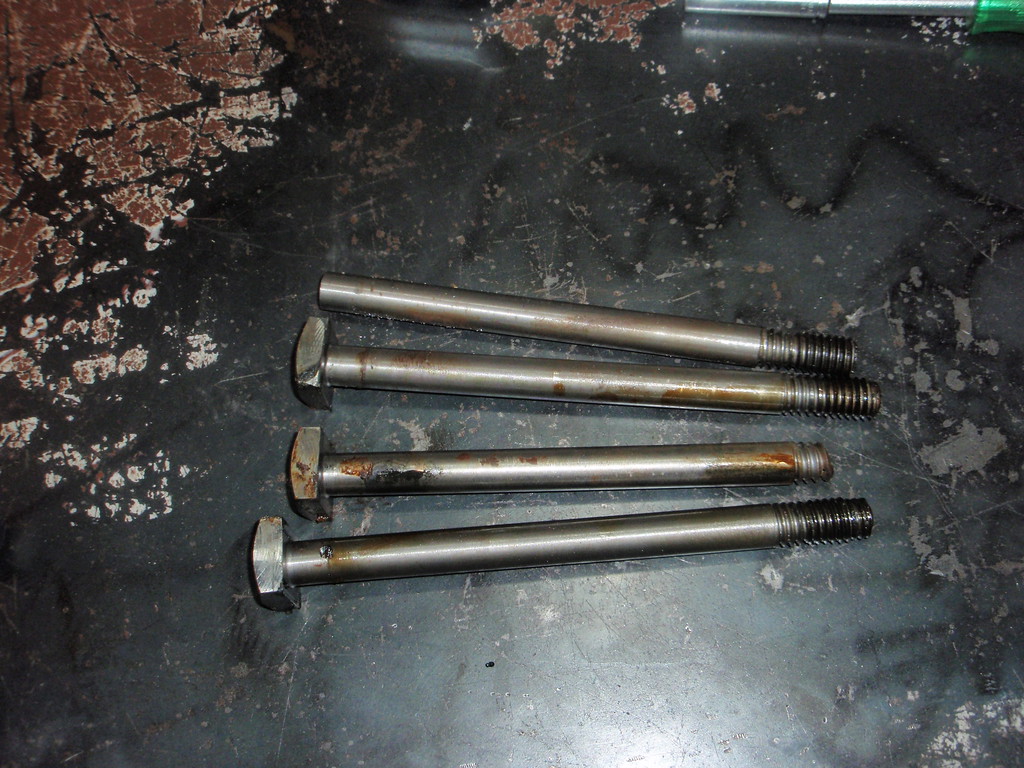
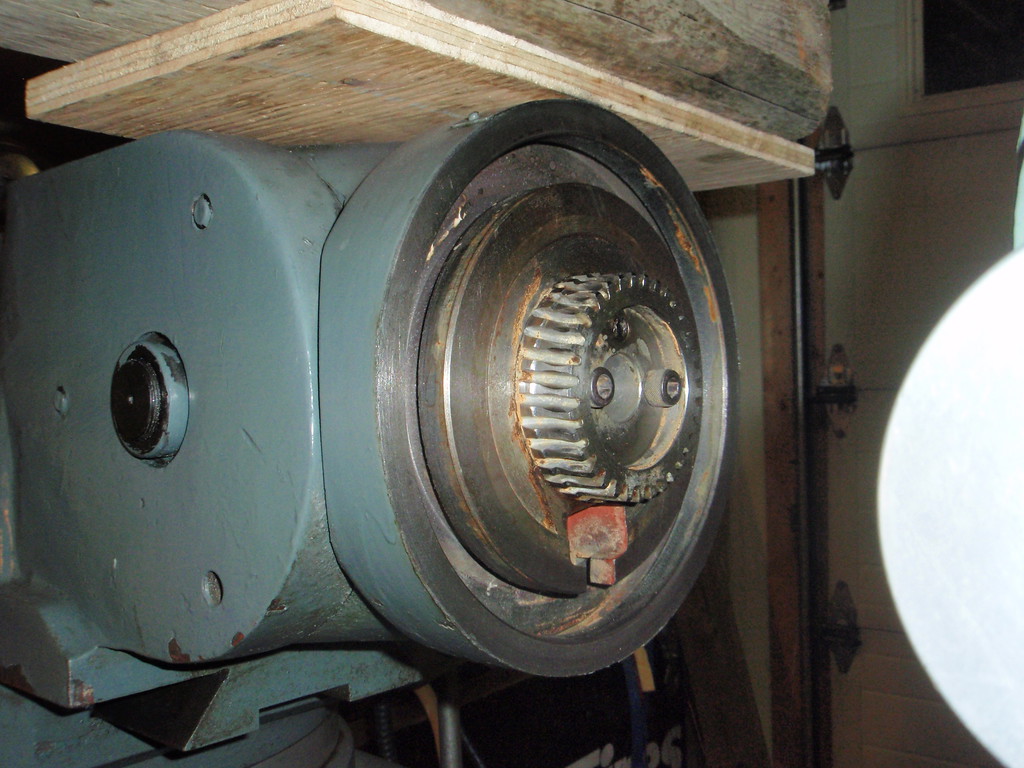
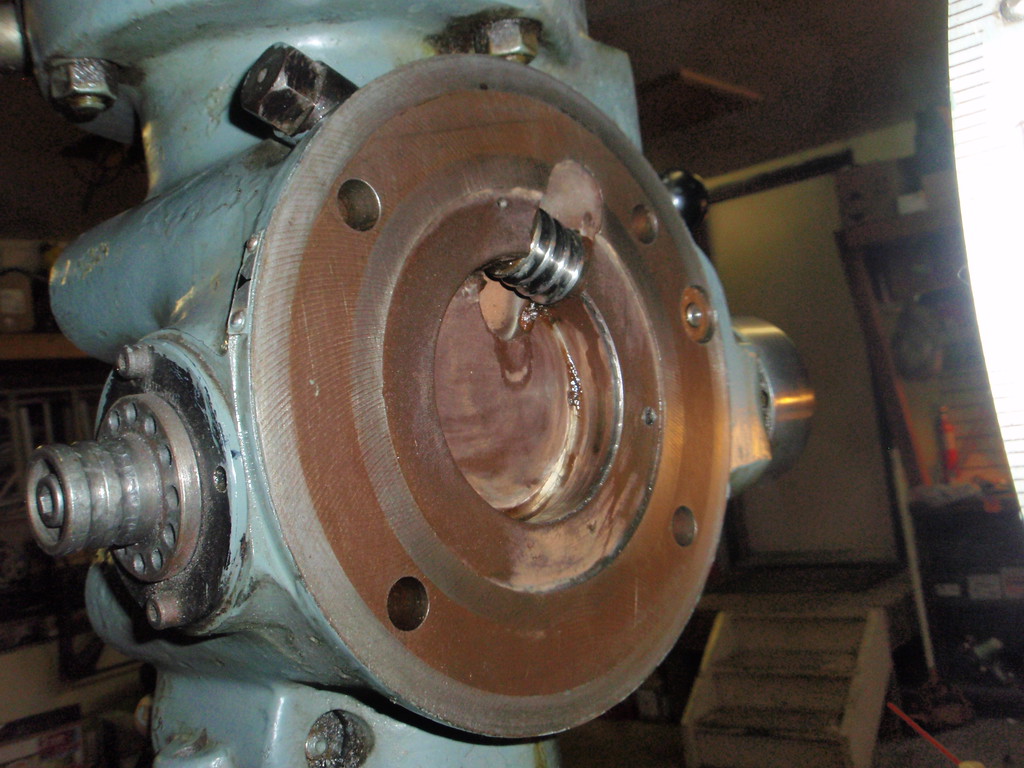
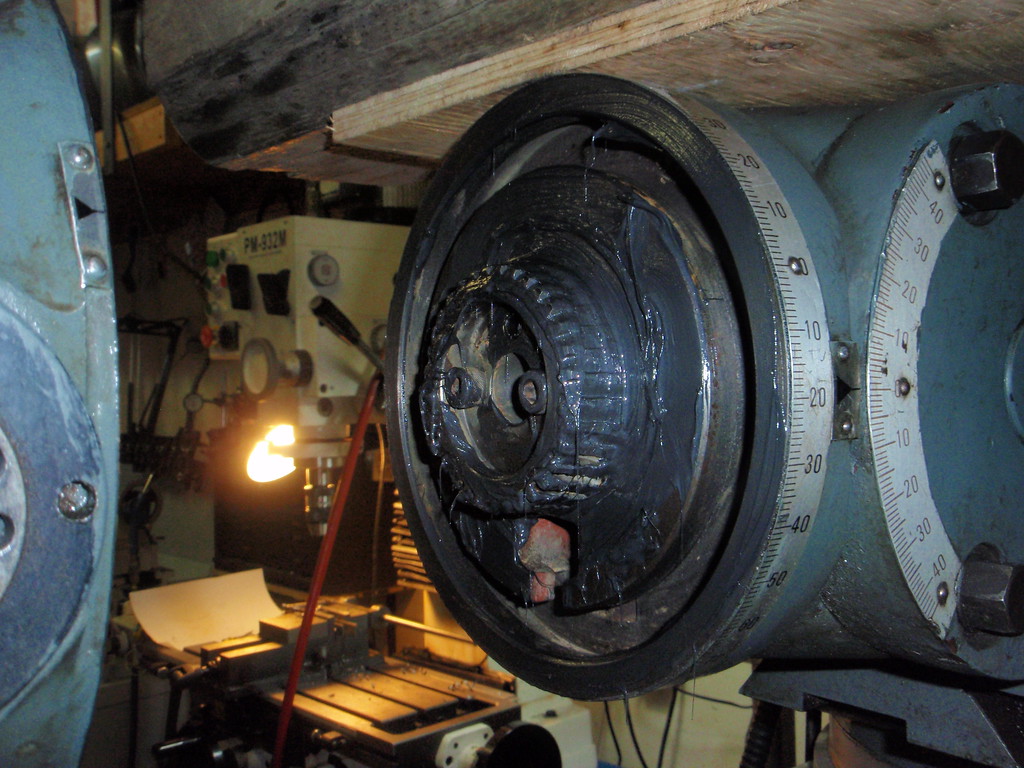
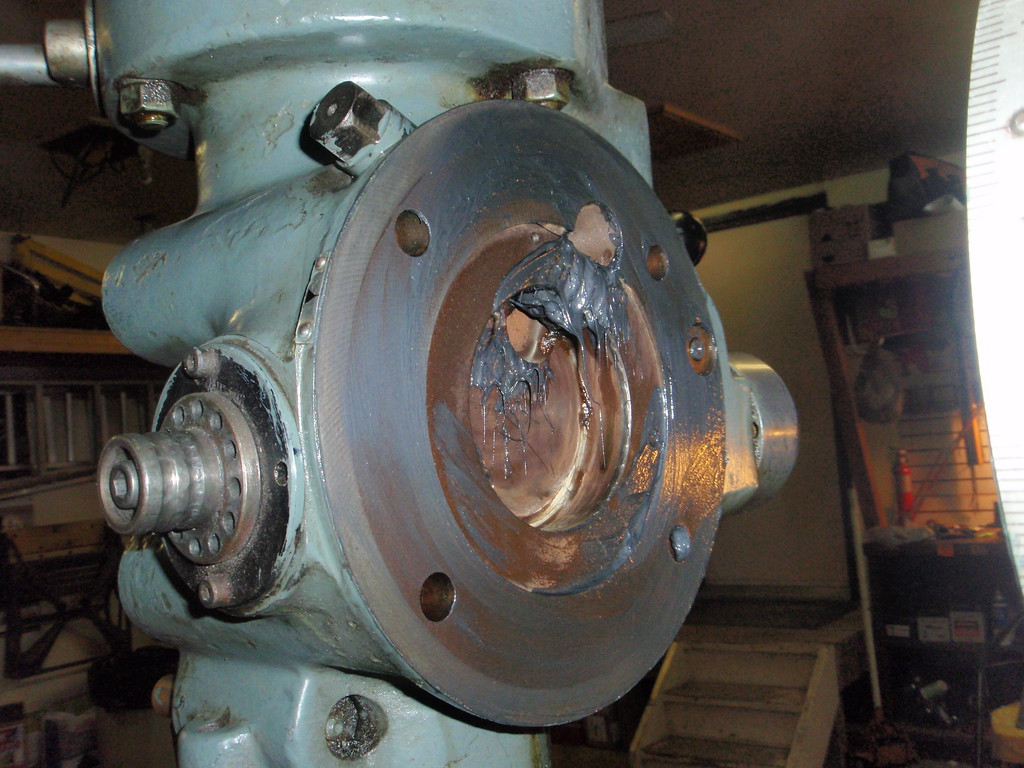
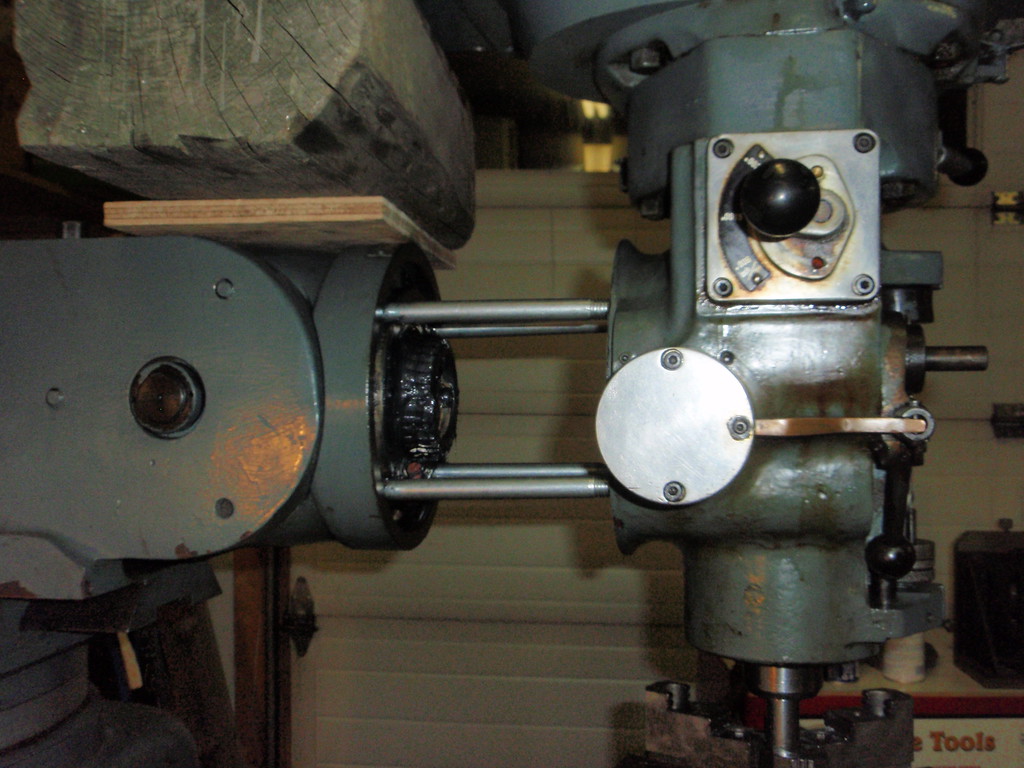
I used some hardened washers from big block Chevy head bolts opened up to 1/2" from 7/16" and long nuts to engage all the thread on the 7" bolts. I smeared lots of moly grease on the worm gears.
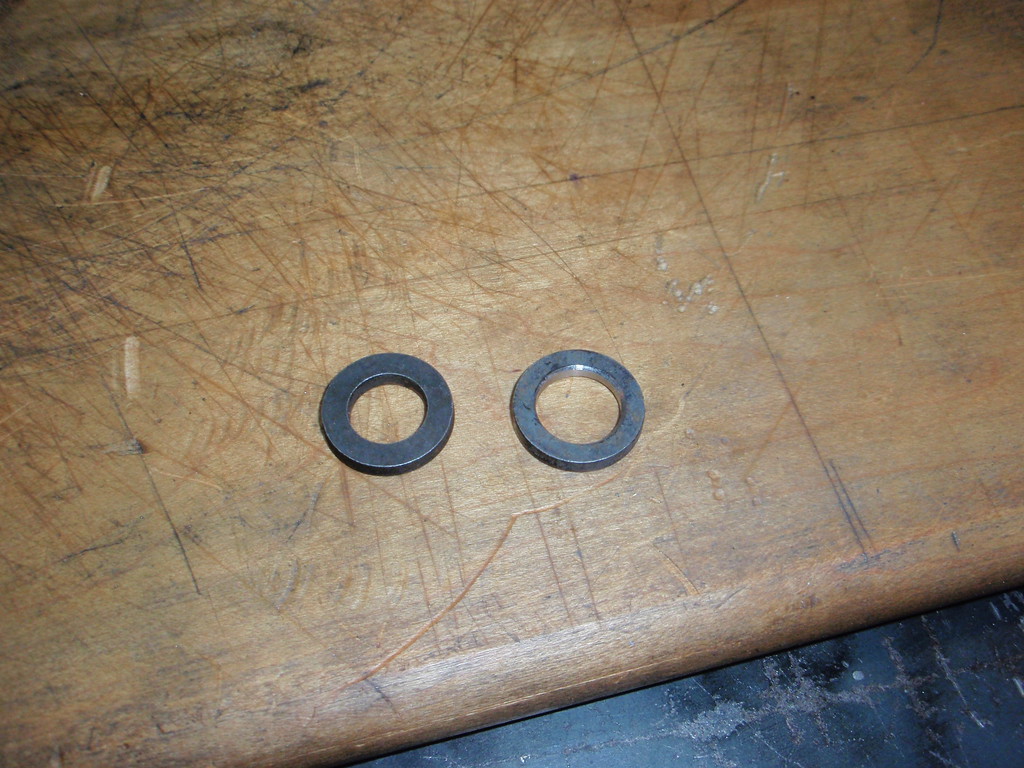
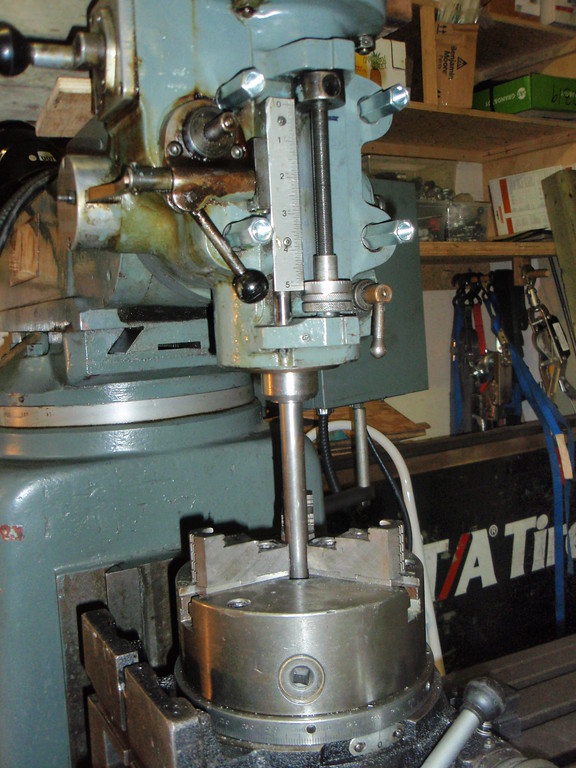
Then I loosened the chuck on the super spacer and lowered the knee, all done!
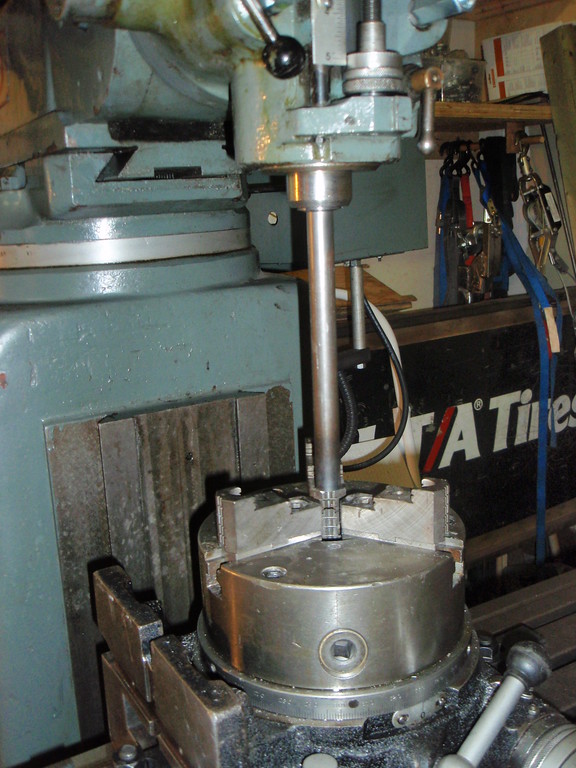