TorontoBuilder
Sapientia et Doctrina Stabilitas
Has anyone used multiples of the typical hall effect sensor on the same spindle? Those typical cheap sensors with a detection distance of 10mm.
If so, how far apart did you place the read heads so they did not interfere with each other? I'm hoping 25 mm will suffice.
If so, how far apart did you place the read heads so they did not interfere with each other? I'm hoping 25 mm will suffice.
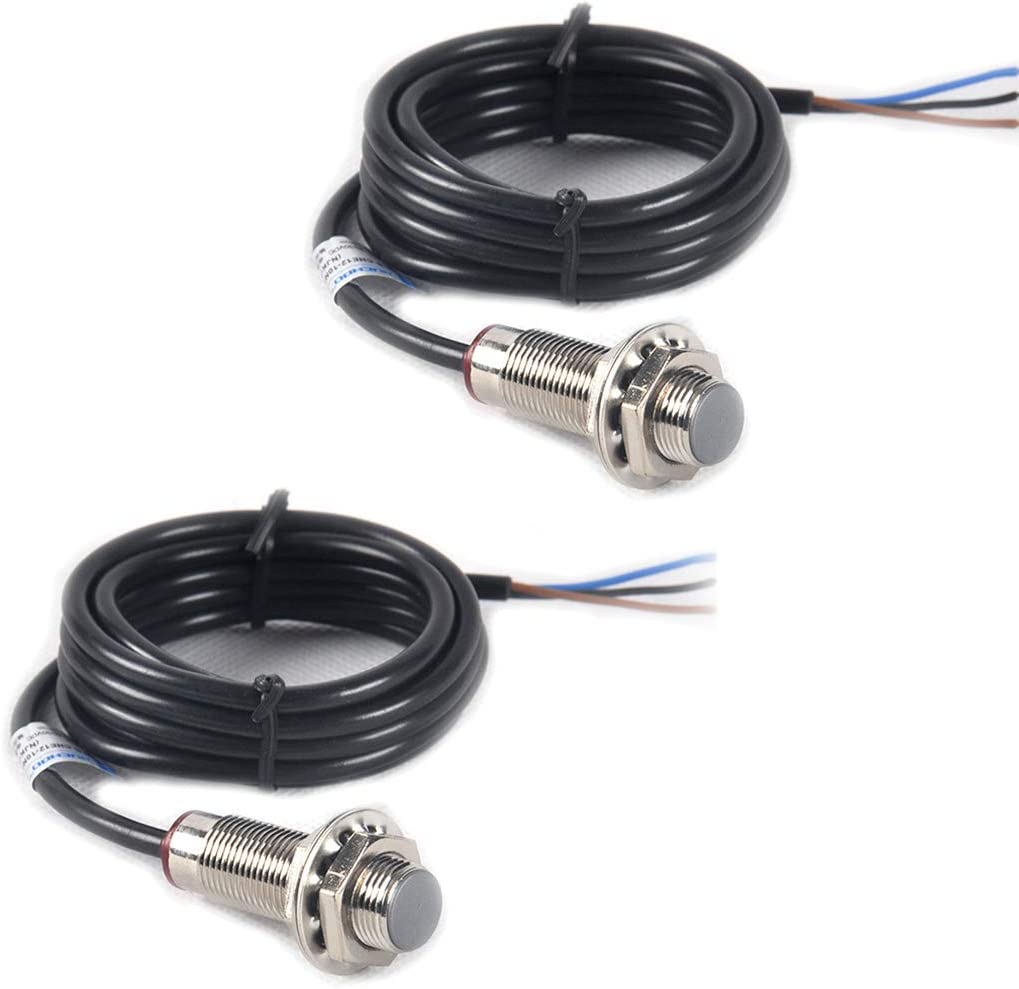