ThirtyOneDriver
Johnathan (John)
I'm following - what you're describing @Brent H is where my head was at when I took those parts out of the box the first time.
@Susquatch - I should have a "butt pincher" but we have a saying in this shop... once something hits the floor or goes behind something it's "gone forever" (realistically, that means at some point I'm going to lay on the floor to recover it, but it might not be right away)
Thanks for the reminder @Six O Two, sometimes you have what you have... speaking of which... ...
I think I need to make that adapter bar/rod/piece of hardware so that I can put the BXA QCTP on the tool slide for a couple of hours... I have something that I need ready for Thursday morning (start of day) that I don't think I have any tools (except the cheap boring bars(?)) here capable of doing it. I have 4 automotive hub adapters that fit a set of rims but don't fit the hubs on the vehicle those rims are for (hub bore needs enlarged) - they're aluminum and 1.5" thick (~2 1/2" center bore, 6 or 7" outer diameter) - I may be able to get away w/ one of the lathe cutting tools I have; the first attempt I only had the cheap 3/8" ones and there wasn't enough clearance... also, I may not need to go that deep to relieve(?) them for the lip of the hub.
I think I have all of the tooling necessary to make (adapter render)
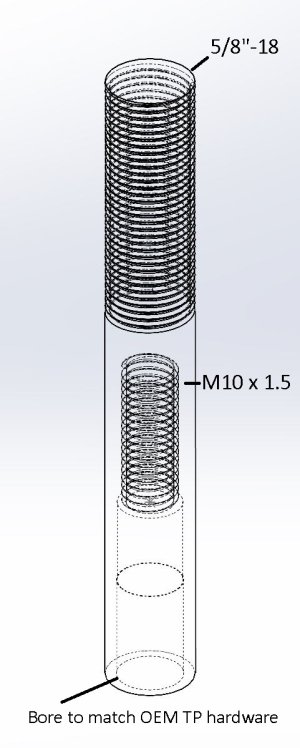
After the hub adapters, I'll get back to setting up the mill (and doing the lathe project, etc.) I have made a couple of parts here and there, mainly bushing type stuff, on the lathe, but I do need a good starter project or two.
Also, essential tools - I think I need a boring head in the future (maybe the lathe and the boring bar will work for the basic ideas) - a main component that I would like to stop paying someone else to make is a threaded bung that we use in the jack-bolt system of the racecar (basically levelling feet for the suspension - I'd like to use the same size for the levelling feet for my lathe and milling machine stands because it's easy for me to get the bolt side of it) - they're 1 1/8" NFT (already have the tap).
Thanks for the support - I'll check the thread later - there's some snow that needs moved so the propane guy can relocate the shop's propane tanks... hopefully I can get the shop warmed up a little in the near future.
@Susquatch - I should have a "butt pincher" but we have a saying in this shop... once something hits the floor or goes behind something it's "gone forever" (realistically, that means at some point I'm going to lay on the floor to recover it, but it might not be right away)
Thanks for the reminder @Six O Two, sometimes you have what you have... speaking of which... ...
I think I need to make that adapter bar/rod/piece of hardware so that I can put the BXA QCTP on the tool slide for a couple of hours... I have something that I need ready for Thursday morning (start of day) that I don't think I have any tools (except the cheap boring bars(?)) here capable of doing it. I have 4 automotive hub adapters that fit a set of rims but don't fit the hubs on the vehicle those rims are for (hub bore needs enlarged) - they're aluminum and 1.5" thick (~2 1/2" center bore, 6 or 7" outer diameter) - I may be able to get away w/ one of the lathe cutting tools I have; the first attempt I only had the cheap 3/8" ones and there wasn't enough clearance... also, I may not need to go that deep to relieve(?) them for the lip of the hub.
I think I have all of the tooling necessary to make (adapter render)
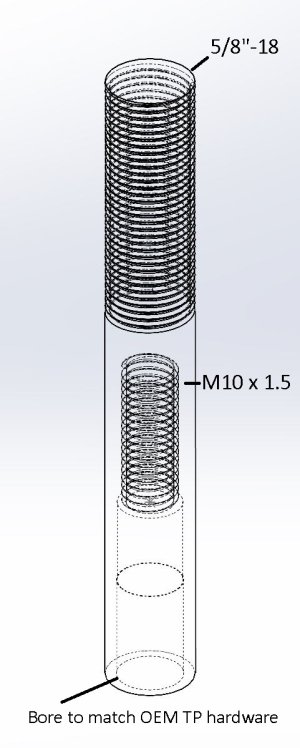
After the hub adapters, I'll get back to setting up the mill (and doing the lathe project, etc.) I have made a couple of parts here and there, mainly bushing type stuff, on the lathe, but I do need a good starter project or two.
Also, essential tools - I think I need a boring head in the future (maybe the lathe and the boring bar will work for the basic ideas) - a main component that I would like to stop paying someone else to make is a threaded bung that we use in the jack-bolt system of the racecar (basically levelling feet for the suspension - I'd like to use the same size for the levelling feet for my lathe and milling machine stands because it's easy for me to get the bolt side of it) - they're 1 1/8" NFT (already have the tap).
Thanks for the support - I'll check the thread later - there's some snow that needs moved so the propane guy can relocate the shop's propane tanks... hopefully I can get the shop warmed up a little in the near future.