Back in around 2006 when the monitors were still glass tube based and big and PCs were large and laptops really expensive many of us wanted to be able to do metric threading on our imperial lathe. I just wanted to be able to thread on my Gingery lathe without all the extra work of making gears first. For small lathes and the occasional threading no one wanted a PC etc larger than the lathe itself or actual CNC.Another reason for your interest in the Pi I guess. If I were doing it (and I'm not), I would probably develop a PIC or dedicated controller that took character based output (think printer or USB Communication) to generate code to control my hardware and move totally away from PCs and Macs other than for the printing/USB Control output.
So the ELS was born. The CAD_CAM_DRO group, MACH group, and DIY_CNC groups all said we were nuts and some members were actually quite abusive at the time. So we formed the E_Leadscrew group. Moderated to stay on topic, no abuse tolerated.
One member from Australia who was totally against the project even went so far as to whip up a simple display, two buttons and a rotary knob version. Kind of like the electronic gearing you see now. No one was interested in something like that. Using a knob to scroll through 0..9, click button, scroll 0..9 for the next digit etc. If my KitchenAid stove/oven had that interface for setting oven temperature or timer we wouldn't have bought it. Most members on the group agreed that human factors engineering was really important and that includes a keypad.
Your comment about duplicating a keyboard brings back memories too. Back in the 90's a client of mine needed what's in this photo. Microchip PIC based it duplicated the old style IBM keyboard protocol, before USB. I wrote the software for it. Even then his customer didn't want a rotary knob to enter in numbers one digit at a time.

But to return to your comment. The ELS, which even included a micro-stepper driver for the carriage was the inexpensive, non-PC solution. Now the two chips for the micro-stepper cost more than a leadshine drive from amazon.ca so it's no longer part of the kit.
I actually used a BeagleBone black along with a CNC cape that had parallel port emulation to first run my mill. From May 2018 a 30 second video show Y and Z motion run with the BBB. I had hopes of turning the BBB into an ELS that could, with monitor/keyboard/mouse added become full CNC or just back to LCD display and keypad the ELS. So simple power feed and all the DRO type operations or full CNC.
But the cape required Normally open limit switches and support for MachineKit (LinuxCNC on the Beagle) dropped so the project did too.
Here's the overall view with two axis controlled.
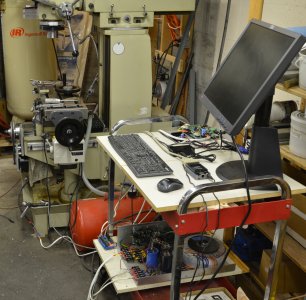
A close up of the Beagle right above the mouse there and in the background the HP_UHU DC servo drive run with a 105VDC power supply.
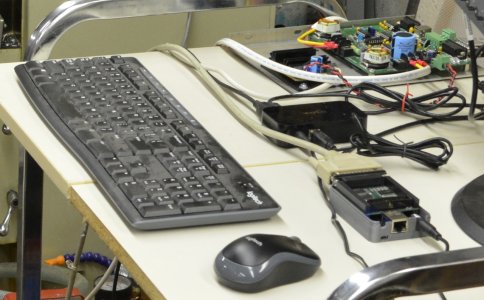
The knee was still run with a Gecko Stepper drive and a 60V power supply.
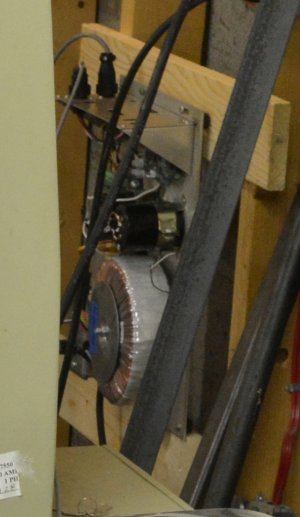
And finally the 105 VDC power supply with the BoB. The supply had over voltage clamping, reduced current startup and fast drain of the capacitors on shut down.
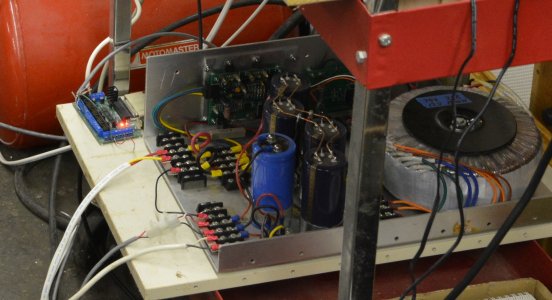
The point to all these pictures is the one we made often on the E-Leadscrew group. The controller can be very small. The infrastructure is pretty well always BIG.
Time to go do something constructive....