mprozycki
Member
Hey guys,
It's been a few months since I've posted but I'm nearing the point of moving forward with having a part from "Ball-Socket Joints" project CNC machined. I had some really good help from a fellow member (PeterT) with creating a clean technical drawings, which i implemented right away. I have completed the tech. drawings for the part bellow (not shown), but I recently decided to add one small detail to the joint as shown.
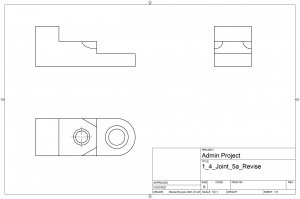
It's a slight cut on the corner of the part to allow for clearance. It's essentially a cut done with a ball-end milling moving across the piece at a 30 degree angle. However, I'm at loss as to how to describe it in terms of the tech drawing. The STEP file that I'm submitting has all the information but I'd like to also demonstrate the nature of the dimension in the drawing.
If someone could point me to a resource that discuss how to draft a complex dimension like this, I'd really appreciate it.
Or you can tell me that I'm way over my depth as a hobbyist and I'll begrudgingly opt out of the detail. Thanks for hearing me out.
P.S - Here is a quick link describing the nature of my project in a previous post.
https://canadianhobbymetalworkers.com/threads/question-regarding-coatings-on-s-s-balls.2849/
It's been a few months since I've posted but I'm nearing the point of moving forward with having a part from "Ball-Socket Joints" project CNC machined. I had some really good help from a fellow member (PeterT) with creating a clean technical drawings, which i implemented right away. I have completed the tech. drawings for the part bellow (not shown), but I recently decided to add one small detail to the joint as shown.
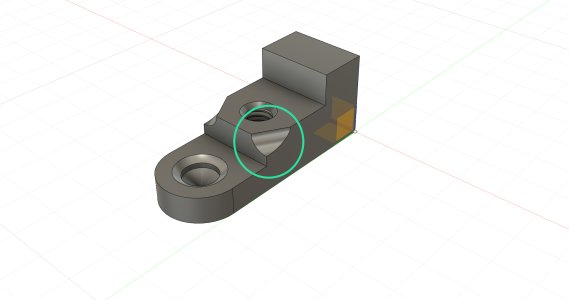
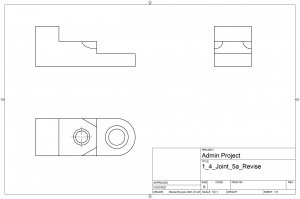
It's a slight cut on the corner of the part to allow for clearance. It's essentially a cut done with a ball-end milling moving across the piece at a 30 degree angle. However, I'm at loss as to how to describe it in terms of the tech drawing. The STEP file that I'm submitting has all the information but I'd like to also demonstrate the nature of the dimension in the drawing.
If someone could point me to a resource that discuss how to draft a complex dimension like this, I'd really appreciate it.
Or you can tell me that I'm way over my depth as a hobbyist and I'll begrudgingly opt out of the detail. Thanks for hearing me out.
P.S - Here is a quick link describing the nature of my project in a previous post.
https://canadianhobbymetalworkers.com/threads/question-regarding-coatings-on-s-s-balls.2849/